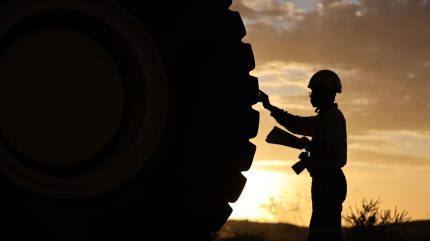
The mining industry is making substantial strides in adopting safety-related technologies to reduce accidents and improve overall safety and efficiency of operations. Automated collision avoidance systems and fatigue detection technology can help workers reduce risks, while technologies such as autonomous vehicles, robotics, and drones are helping by removing humans from hazardous areas.
However, not all safety technologies need to be sophisticated robots controlled by AI. Regular maintenance of vehicles and other mining equipment not only makes them safer to operate but can spot defects and potential safety concerns early. The latest generation of lubrication monitoring and oil analysis also ensures that machines remain in service safely for longer.
Trends in mining safety technologies
According to GlobalData’s Safety Trends in Mining 2024[1], there were mixed safety outcomes in 2023, with a rise in fatalities but a notable reduction in injury rates. The average number of fatalities among the 56 miners studied in 2023 increased to 3.8 from 2.8 in 2022. Total recordable injury frequency rate (TRIFR) data was available for 42 of the 56 companies analysed from 2019 to 2023. On average, these companies continued to improve their safety records, with the TRIFR falling from 2.8 in 2022 to 2.7 in 2023 (based on injuries per million hours worked) – the fifth consecutive year of improvement.
Future investment in technologies that can improve safety and efficiency further at mine and processing sites was recently examined by GlobalData’s H1 2024 mine site survey[2], which covered various technologies, particularly those designed to enhance safety. A total of 162 individual mine operators were interviewed, with almost 50% of responses from surface-only mines, 33% from underground-only mines, and 17% from where mines had both surface and underground operations.
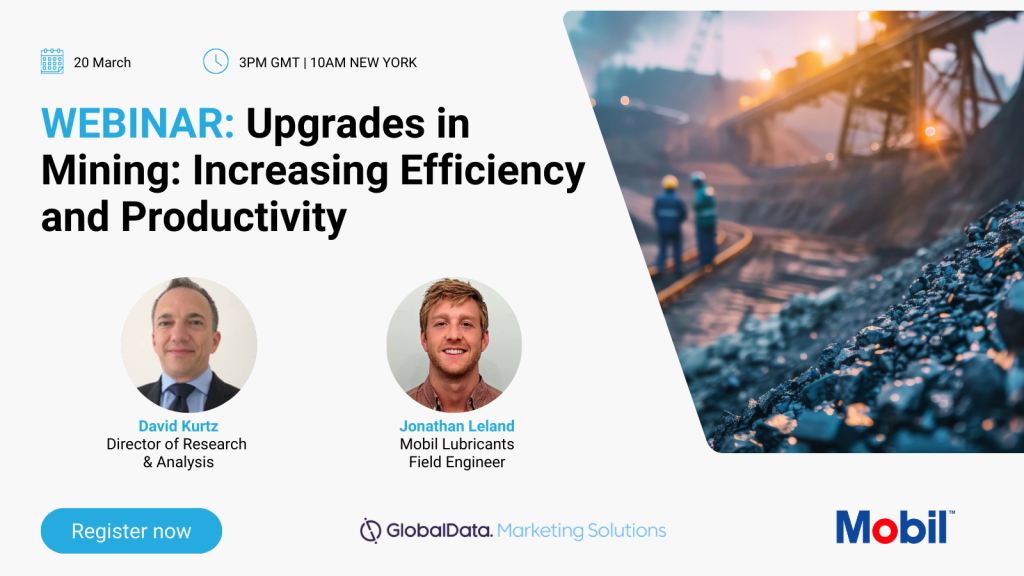
We explore the top five areas in mine safety poised for investment based on these findings.
1. Collision avoidance systems (CAS)
Collision avoidance technology is at the forefront of safety investments in mining. This technology includes proximity detection systems (PDS) and vehicle control systems (VCS), which work together to detect nearby vehicles or personnel and either alert them or intervene to prevent collisions. In the survey, 40% of mines indicated plans to invest in collision avoidance technology within the next two years, reflecting a significant commitment to improving safety on mine sites.
2. Fatigue detection technology
Fatigue detection systems are another critical area of investment, with 37% of mine operators expecting to invest in this technology over the next two years. The technology warns operators when signs of fatigue or distraction are detected, which is crucial in maintaining safety standards in mining operations. Investment in these systems has seen a notable increase, up by around 10% from the previous year.
3. Wearable technology at mines
Wearable devices that monitor the health and safety of workers are gaining traction in mining. These technologies can provide real-time data on the physical condition of miners, alerting them and their supervisors to potential health risks before they lead to accidents. The adoption of wearables is expected to rise as companies seek to enhance worker safety.
4. Robotics, autonomous vehicles, and drones
Investments in remote-controlled vehicles are also on the rise, as they reduce the need for a human presence in hazardous areas. This technology is particularly valuable in underground mining, where risks are intensified. The survey indicates a growing trend toward using these vehicles to enhance safety by keeping workers out of harm’s way.
The shift towards fully autonomous vehicles is gaining momentum, with many mining companies exploring robotics to further minimise human involvement in dangerous tasks. While still in the early stages of adoption, technologies such as autonomous vehicles are being increasingly implemented to remove human workers from hazardous environments, particularly in surface mining operations. This shift not only enhances safety but also optimises operational efficiency.
Other recent advancements are drones, which is one of the fastest-growing trends in mining. According to the 2024 survey, drones are increasingly being used for various purposes, including site surveying, monitoring equipment, and enhancing communications. Their ability to access hard-to-reach areas makes them invaluable for safety inspections and operational assessments.
5. Mine management software
While the survey indicates that investments in some technologies such as battery/electric-powered vehicles and fully autonomous systems remain relatively low, the trend is shifting towards predictive maintenance and advanced management software, which has been widely adopted. This technology is integral to improving safety protocols and monitoring compliance with safety regulations, as well as facilitating better decision-making and operational efficiency.
How lubricants can improve safety in mining operations
One key safety feature for mining equipment is effective lubricants. Designed to protect equipment in the harshest of mining conditions, they also contribute to keeping equipment working safely at optimum efficiency.
Jonathan Leland is a lubrication engineer and synthetic lubricant specialist at Mobil™. Mobil Field Engineers, such as Leland, help mine operators optimise lubrication and maintenance programmes to improve equipment safety, performance, and reliability.
Leland says that extending component life and reducing the frequency of maintenance tasks – such as engine rebuilds or wheel motor reseals – minimises the need to have technicians working on equipment. This decreases the risk of accidents or injuries.
“Pulling an engine from any asset is extremely labour-intensive,” Leland says. “By safely deferring and extending, you are eliminating the chance of somebody getting a pinched finger, scraping their arm or, God forbid, something worse. With these maintenance practices, it all adds up.”
Additionally, when equipment is running reliably without issues, operators are less stressed and can focus on safe operation. Unreliable equipment can lead to frustration and increased safety risks.
Further, using sensors to enable real-time oil monitoring can eliminate the need for physical oil sampling, further reducing the risk of accidents that can occur when technicians have to access mining equipment or work around it.
Countering fuel dilution with robust lubricant analysis
A crucial issue that field engineers must deal with in the mining space is fuel dilution. When fuel is not completely burned in the cylinder, it can leak past the cylinder and seep into the oil sump. This can happen when the injectors are not making a proper mist of the fuel.
“Fuel dilution is something that, if you don’t catch in time, thins out the oil to the point where you’re causing much faster wear than you should in your engine,” explains Leland. “However, sensors can recognise that fuel dilution before it becomes a bigger issue. That’s also when it’s important to time your oil samples correctly… in this example, when did that fuel dilution start?”
A cutting-edge tool that simplifies the procedure of sending samples for oil analysis is Mobil Lubricant Analysis (MLA). Scan-and-go technology removes the need to manually enter data and look up equipment specifications, resulting in up to a 66% faster submission time, as well as better data accuracy[3]. Users can also receive updates, reports, and recommendations on their mobile devices thanks to the program’s user-friendly design, which also makes equipment monitoring and account management simpler.
A robust safety culture ensures all team members are committed to identifying methods that decrease risks through best practices and promote continuous development. Lubrication contributes to safety in multiple ways, reducing maintenance and increasing equipment dependability.
Download the free whitepaper below to discover how to optimise your mine safety, efficiency and uptime.
[1] https://mining.globaldata.com/Analysis/details/safety-trends-in-mining-2024
[2] Source: GlobalData, Mine Site Technology Adoption Survey: 2024 (taken from GlobalData’s ‘Safety Trends in Mining, 2024’ report September 2024)
https://mining.globaldata.com/Analysis/details/global-mine-site-technology-adoption-survey-2024
[3] https://mobilserv.mobil.com/en/