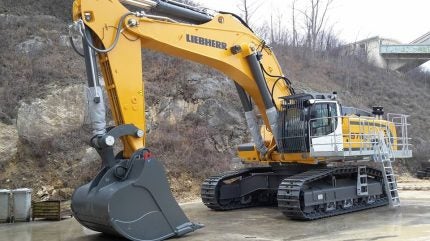
The total global population of tele-remote control and autonomous underground mining trucks and LHDs is estimated at 1,145, latest research from market intelligence firm GobalData reveals. This includes both autonomous-ready equipment as well as those operating autonomously. GlobalData’s mining analysts estimate 55% of those are in Australia and Canada, followed by the US with 6%.
The report says: “Underground mining activities are performed hundreds of meters beneath the ground, to extract the desired minerals in raw ore form. In hard rock mining, to extract and transport the ore to underground crushers or to surface stockpiles, LHDs and trucks are used. Blasting is conducted to enable access to ore bodies, which is risky and requires personnel to be moved to safer places, consuming significant time in transporting manpower.
“This means lost time or production, and hence the benefit to employ tele-remote or autonomous equipment which can be controlled from a remote location.”
Robotics in mining vehicles and equipment becoming critical
Interviews with major mining OEMs and operators reveal the extent that the use of tele-remote and autonomous machines improve productivity, machine utilisation, lower maintenance costs and cut operating costs. One OEM said automation had cut its operating costs by 50%. Other benefits cited include lower maintenance costs, reduced machine damage, increased equipment lifetime, reduced manpower and enhanced safety for workers.
David Kurtz, director of research and analysis for construction, mining and energy at GlobalData, says using robotics to drive down mining costs is “critical”, particularly with the cost pressures mining firms face these days with increasing scarcity of minerals, poorer grades, more remote deposits and a general trend toward mining underground.
He says pre-defined GPS courses and sensors to navigate haul roads and intersesctions is helpful, while robotic techniques can support operator safety in underground rock cutting and make going deeper into a mine easier and faster. Investment in surface haul trucks has also risen, with GlobalData suggesting that these now top 2,000 worldwide.
Automated loading and autonomous drilling will be a focus, says Leigh Carlson, chief executive officer of Fluid Control Services, based out of the US, who supplies many of the bigger mining businesses with a product that is designed to protect the hydraulic cylinders, and by extension the entire hydraulic systems, in haul trucks, excavators and other heavy mining equipment. This product is called the Seal Saver, and it is a custom designed cylinder boot that can be installed in the field without disassembling any cylinders and has an outsize impact on cost-savings as well as safety.
“Repairing a hydraulic cylinder can cost between US $2,000 and US $20,000,” Carlson says. “Almost all repairs will have a much higher cost than the purchase price of a Seal Saver. This is low-tech preventative maintenance, and it can really help bring operating costs down.”
While GlobalData suggests that the expense of automation is still holding some mining firms back, especially if a mine has a limited lifespan, Carlson says the Seal Saver delivers exceptional return on investment (ROI) as well as helping to create a better safety culture.
“Machine failures due to hydraulic system contamination can be devastating,” Carlson says. “Even though we have been operating for about four decades, our product, the Seal Saver, is still unique in the market due to the complete customization of each Seal Saver.
“Mining is becoming very sophisticated, with robotics and the internet of things (IoT) professionalising the industry and raising standards. Our product is not high-tech, but it will reliably and consistently protect the hydraulics of all your most expensive equipment.”
Discover how the Seal Saver can support your business in saving costs and boosting efficiencies in a challenging cost environment