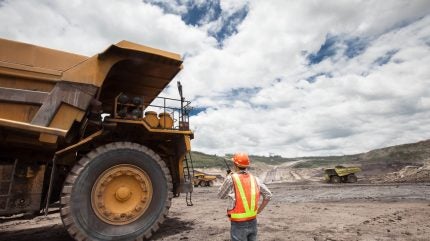
Innovation has played a crucial role in the evolution of lubricant technologies within the mining sector. Automated lubrication systems, for example, enhance equipment reliability and reduce operational downtime, and the development of lubricants with high viscosity indexes has become essential for high-quality engine and transmission oils used in mining equipment.
Significant performance and efficiency gains have come from improvements in fuel efficiency and engine longevity. When machines are properly lubricated, they operate more smoothly, efficiently and consume less energy. According to data supplied by Mobil, this can lead to an improvement in fuel economy of up to 5.1% and a huge reduction in waste oil consumption[i].
Intervals between oil changes and engine rebuilds are also reduced, due to more accurate monitoring of machine wear, highlighting the critical role modern lubricants play in enhancing operational efficiency in mining.
The specialist knowledge deficit
Jonathan Leland is a lubrication engineer who has been with synthetic lubricant specialists Mobil for almost six years, having previously worked in refining. In his current role, Leland helps mine operators to optimise their lubrication and maintenance programmes to improve equipment performance, reliability, and safety.
According to Mobil field engineers, some of the key challenges mine operators face when it comes to lubricants include knowing which lubricants to use and having the correct specifications for their equipment. Leland says that the current labour shortage of highly skilled workers in mining – as more experienced personnel retire – means less expertise in lubricants. Lubricants should be seen as a specialty that requires specific knowledge to fully optimise equipment performance, he says.
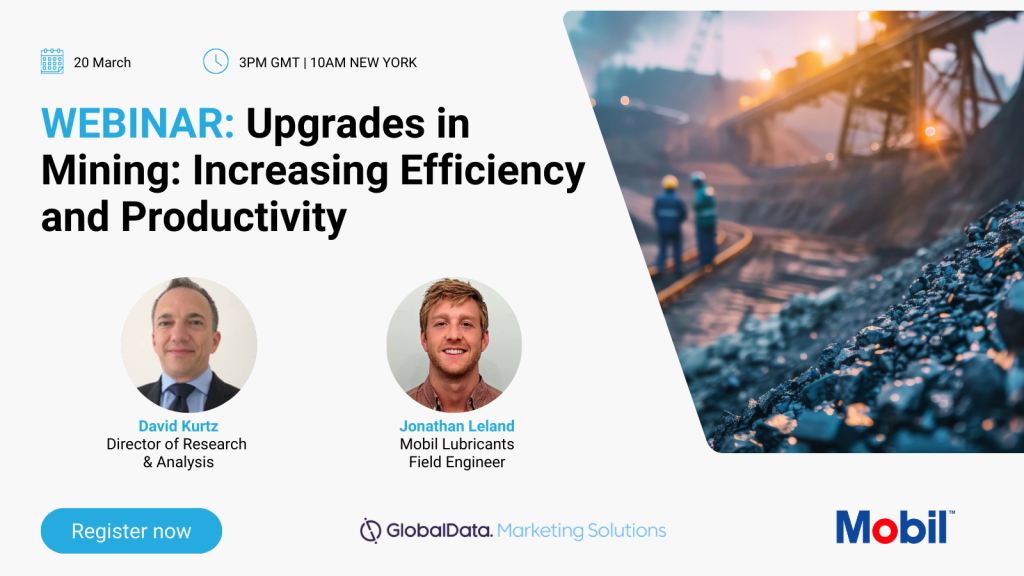
Another challenge is keeping up with the latest technology developments, such as the impact of equipment electrification and the need for specialised fluids for battery cooling.
Extending component life and maintenance intervals
Leland provides a specific example demonstrating how lubricant solutions and expertise allowed one customer to dramatically extend the life of critical components, leading to significant cost savings by avoiding the need for early rebuilds.
“One of the major OEM haul truck brands has electric wheel motors that are [usually] made by GE,” says Leland. “For this particular model, GE recommends a reseal of the electric motor at 24,000 hours and rebuild at 48,000 hours. However, we [Mobil] worked with the customer to use our full synthetic gear oil, walking through why keeping it clean is so important and adding supplementary filtration.
“Then, instead of going into the shop and putting the mechanics at work, we worked with the customer to take samples and saw that the product was fine. Fast forward, they did not have any seal leaks and so at 24,000 hours, they kept going. The oil analysis looked good and they did not have to do the rebuild at 48,000 hours. In the end, they had a wheel motor that they took out to 80,000 hours before it was rebuilt, almost doubling the time between rebuilds.”[ii]
Leland emphasises the role of Mobil™’s lubricant condition monitoring platform in enhancing safety and maintenance optimisation. This innovation from Mobil is allowing mine workers to save considerable time by taking their own samples.
Mobil Lubricant Analysis: a pioneer in this space
Mobil Lubricant Analysis (MLA) is an innovative tool that streamlines the process of submitting samples for oil analysis. It uses scan-and-go technology, eliminating the need for manual data entry and searching for equipment information. This results in better data accuracy and a 66% faster submission process than standard methods[iii]. The programme also offers an intuitive interface for easier account management and equipment monitoring, allowing users to receive updates, reports, and recommendations on their mobile devices.
The state-of-the-art Mobil Lubricant Analysis programme offers many advantages including:
Flexibility: managing and updating equipment registrations online, choosing the specific analysis that fits your needs, and creating and sequencing unique sample routes.
Expertise: using proprietary test control limits set specifically for your equipment to identify problems, establish causes, and recommend actions.
Quality assurance: through regularly audited practices and methods and commitment to consistent, accurate analysis.
The MLA is a crucial tool for mining, providing in-service oil analysis to assess the health of equipment and help increase productivity, reduce downtime, improve equipment durability, and reduce lubricant consumption. With extensive knowledge of Mobil™ products and equipment, it can help lead to cost savings, productivity, and peace of mind.
To illustrate, a Minnesota mining company recently aimed to improve haul truck availability and reduce fuel and operating costs. The Mobil Technical Team recommended optimising preventative maintenance strategies and improving fuel economy, particularly in the vehicles’ transmissions. After analysing data – collected over three years – the team recommended new monitoring strategies, optimised filtration tactics, and switching to Mobil Delvac 1™ Synthetic Transmission Fluid Arctic.
The implementation of these recommendations led to a 2% improvement in haul truck availability and a 5.1% fuel economy, reducing waste oil consumption by nearly 6,000 gallons, and resulting in an annual revenue enhancement of US$2.1 million[iv].
In collaboration with miners and engineers
Mobil’s global network of engineers works closely with customers, equipment builders, and mine operators, to develop and implement new and innovative solutions such as the MLA system.
“It’s part of our processes, to talk about opportunities or where they want to go,” Leland says. “It’s important to sit down with the customer at the beginning of the year to discuss opportunities and priorities, defining value and goals for any potential changes – whether it’s production, safety, environmental, or other objectives. We ask: ‘Why are you doing it the way you’re currently doing it?’ and ‘What’s the case for change?’ Defining the value is always part of step one.”
Mobil and their highly skilled engineers aim to instil a belief in the customer that there are always better ways to do things through best practice and by using a technical collaborative approach. Together with the importance of truly understanding the customer’s needs, engineers work together to optimise their operations, rather than just providing off-the-shelf solutions.
Download the free whitepaper below to discover how to optimize your mine safety, efficiency and uptime.
[i][ii][iv] Results are based on the experience of a single customer. Actual results can vary depending upon the type of equipment used and its maintenance, operating conditions and environment, and any prior lubricant used.
[iii] https://mobilserv.mobil.com/en/