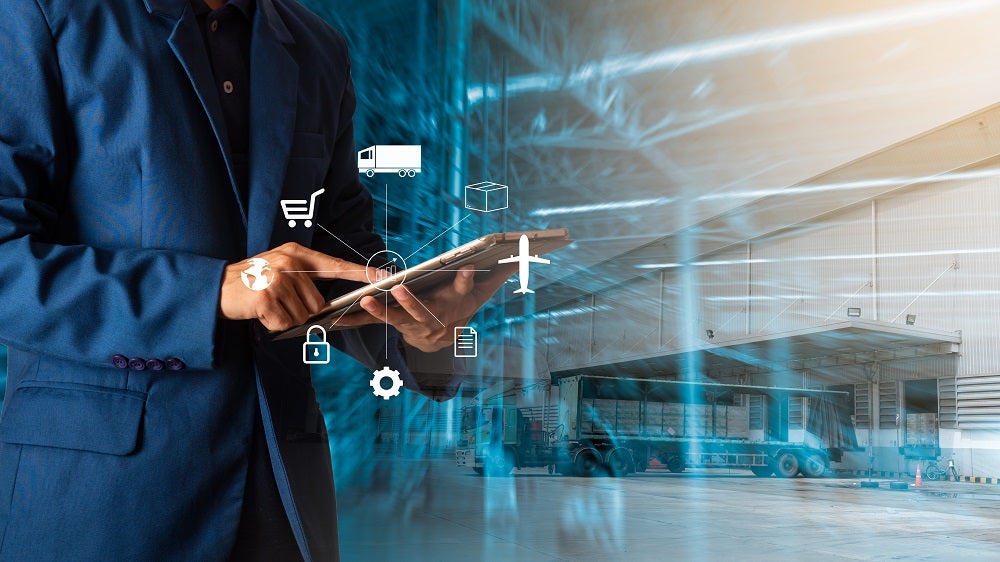
The effects of the Covid pandemic rippled out to industries globally, and the mining sector has been heavily impacted by the unpredictability that it brought in its wake. From suppliers to distributors to end-users, disruptions to production and transportation have introduced new challenges for us all.
For Normet, letting down its customers is not an option. Even in the depths of the pandemic, when mitigating disruptions was impossible, Normet worked closely with its suppliers to keep customers informed.
According to Lasse Mod, director of spare part business at Normet Group, who is responsible for the global spare part supply chain: “We have faced occasions currently where we have needed to say “we don’t know”. We are not used to tell that to customers. The Covid pandemic has been an unpredictable time.
“It has been difficult to plan for materials to ensure that they are in the right place at the right time, because there are so of many unexpected things happening in the transport chain. There are continuous disturbances, capacity restrictions which lead to an end result: some of the airlines are unable to fulfil daily delivery of our goods. On top of the unreliability of transports, the cost of airlines have doubled since before Covid.”
To further exacerbate disturbances, transport delays have impacted suppliers further down the supply chain, severely impacting availability even for parts that are in demand.
“Material availability from suppliers are facing the same issues. Obviously, we want to forecast these challenges for customers, but some suppliers cannot inform us about when the next delivery will be,” Mod explains.
So, is there a solution? According to Mod, communication and regular updates from suppliers has been particularly important during the pandemic. To further mitigate supply chain risks, the company has been investing in its inventory to ensure that the most in-demand products are available to customers.
“We have weekly, even daily communication and following up with suppliers. It’s a lot of updating information in the system. Since Covid, our team have a lot of focus on the daily operations of deliveries.
“Additionally, we have been focusing more on long-term demand and forecasting, especially what will be needed in the next 12 months. We purchase needed items in advance to manage the disturbances in the supply chain and freight transportation.”
In addition to procuring materials and spare parts from suppliers, Normet manufacturers a range of its own products. Again, managing internal supply chains has involved effective communication.
“We have really active communication with our production and local offices,” Mod explains. “We cross use materials if there are shortages, and we can use materials from our inventories to make up for critical demand. Normet has a shallow organizational structure, so we can be agile and get parts where they are needed.
“Also, Normet has the internal capability to be able to refurbish used components to their former glory (to give them second life). This has helped Normet to manage and patch material shortages all around the globe.”
Normet’s spare parts and logistic services have been supplying customers with the highest quality products long before the pandemic. Combining industry knowledge and more than 50 years of experience manufacturing industry-leading mining and tunneling equipment, Normet has built a distribution and supply network with the ability to provide fast and efficient delivery of spare parts and materials to its customers globally, even during unpredictable eras in the industry.
For more information about Normet’s products and services, download the whitepaper below.