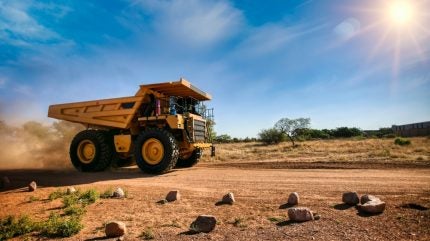
Under the Paris Agreement, signatories are committed to cutting greenhouse gas emissions (GHG) and keeping global warming below 2°C above pre-industrial levels. As countries work to fulfil their climate commitments, many business sectors are also looking to address their emissions reduction and broadly advance their sustainability-related ambitions.
The mining sector, a contributor to global carbon emissions, is no exception. For mining, the shift towards sustainable practices will include moving to renewable energy, making machinery even more efficient and long-lasting, as well as electrifying equipment, and increasing automation. Resource utilisation also needs to be tackled, reducing waste to landfill, as well as improving material recycling to help create a more sustainable supply chain.
As the race to net zero heats up, even small efficiency improvements can make a significant difference between reaching targets and missing them.
Ambitious targets
Many mining companies have set ambitious long-term goals for reaching net zero carbon emissions by 2050. In the interim, they are working to implement shorter-term emission reduction goals, typically aiming for around a 30% reduction by 2030. The main contributors to Scope 1 and Scope 2 emissions include the use of heavy machinery, ore transportation, various on-site processes and the purchase of electricity, making up around 40% of total emissions[i].
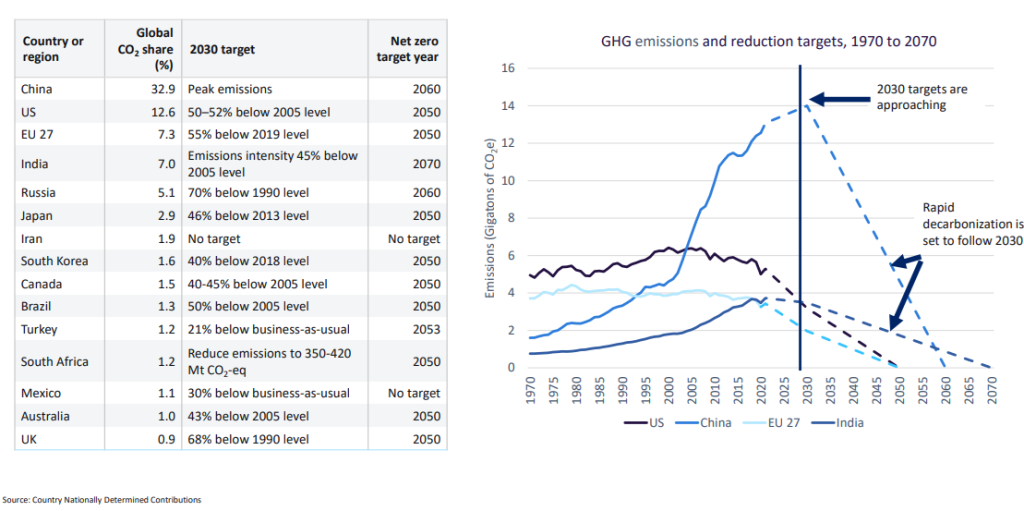
Mining companies are increasingly investing in renewable energy, with many setting short-term 100% renewable energy targets. This shift is enabled by a growth of renewable energy as part of the energy mix. In particular, solar power now accounts for 63.8% of the capacity in development, with the largest solar investments in Africa and Australia. While many operators are planning to transition to battery-electric or hydrogen-powered machines to help achieve their targets, the adoption of battery-electric machines is relatively low[ii] thus far, with broader adoption expected in the 2030s. In the meantime, companies are adopting renewable diesel and biofuels as a transition pathway to achieve interim emissions targets. Liquefied natural gas (LNG) is also being used to reduce emissions from fossil fuels like coal, diesel, and heavy fuel oil.
Another short-term win for reducing emissions can be found in supply chain collaboration, with companies working with downstream industries to develop and implement emission reduction initiatives.
Medium-term emissions reduction strategies include diesel displacement in favour of EVs. Automated systems and autonomous vehicles can run for longer, more safely and efficiently, without the need for downtime for shift changes or rest breaks. Meanwhile, the latest drone and monitoring technology is being used for more efficient surveying and site-safety checks.
And these initiatives are working, with miners already making important inroads towards net zero.
After analysing the performance of 85 mining companies, GlobalData observed that over the 2018 to 2022 period, there has been an overall 14.3% decrease in Scope 1 and Scope 2 emissions over the period, with 42% of miners reducing their emissions. One company managed to reduce emissions (MtCO2e) by 39% over the same period.[iii]
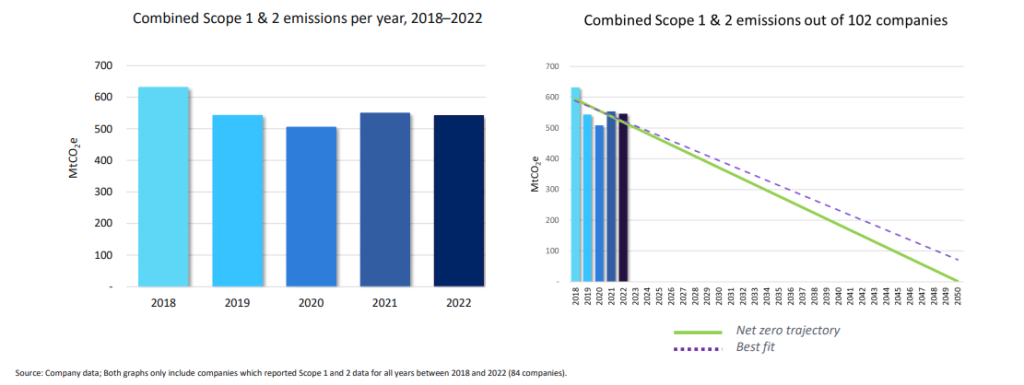
While this indicates progress, total sector operational emissions remained above 500 MtCO2e between 2018-2022 (with a trough in 2020 due to Covid-19 operational interruptions.) While overall emissions are decreasing, more work is needed to continue the progress.
Advancing miner’s ambitions
Key brands like Mobil™ are keen to help support mining customers in achieving more with less. Guido Spinelli is the Finished Lubricants Field Engineering Services Manager for Mobil North America and has years of experience working alongside customers to help them with their sustainability ambitions.
“Mobil can help miners to ensure their mobile and plant equipment are working at their optimum,” said Spinelli. “We collaborate with them on using less fuel and oil on mobile equipment and using all-season products to reduce or eliminate seasonal changes and improve all-year-round efficiency. In some cases that can mean reducing the size of the fleet to achieve more with less.”
As downtime reduces a site’s efficiency, ensuring vehicles and machinery remain in service for longer between services can have a major impact, both on efficiency and safety. Reducing planned downtime of mobile equipment also increases a customers’ shop availability to better manage other work such as unplanned maintenance.
“We encourage condition monitoring of oil where possible to optimise maintenance schedules.,” explains Spinelli. “That means machinery can stay in operation for longer between services, but it also means a better chance at picking up problems before they become a major issue.”
For example, Mobil lubricant solutions and expertise were recently used to help a mining customer extend oil drains and ultimately engine life on their fleet of 30 haul trucks from one of the major OEM brands, powered by Cummins QSK 60 engines. By using Mobil Delvac 1™ ESP synthetic engine oils, the mine has increased engine oil drain intervals up to 2,000 hours and safely extended engine rebuild cycles from 28,000 hours to 36,000 hours. As a result, the customer has realised increased equipment availability and production levels. This success is attributed to using the best Mobil lubricants combined with a disciplined, data-driven approach taken by their reliability team towards maintenance*.
Mobil’s lubricant condition monitoring platform also enhances safety and maintenance optimisation by allowing mine workers to take their own samples using the Mobil™ Lubricant Analysis (MLA) tool, streamlining oil analysis submissions using scan-and-go technology.
Increasing efficiency for off-highway vehicles
For Mobil, working in collaboration with their customers is a vital piece of the puzzle when it comes to increasing sustainability.
“We are constantly looking for areas of commonality,” said Spinelli. “Looking ahead and seeing where we can be proactive in developing new solutions for our customers. For example, we have recently developed some new products for hard-to-decarbonise, high-horsepower, off-highway engines in our Mobil Delvac™ portfolio.”
Increasing hours between drains and reducing downtime is a vital component to increasing productivity and becoming more efficient. As mining and construction equipment evolves, engines often become larger to increase efficiency, necessitating the right oil to maximise performance. To this end, Mobil has designed a range of new products that are specifically formulated for high-horsepower engines.
Mobil Delvac Ultra™ 5W-40 Extended Performance oil is an advanced full synthetic, providing extended Oil Drain Interval (ODI) potential up to four times the average OEM ODI recommendation, or up to 2,000 hours. It also offers 45% more wear protection than required in API engine tests and exceptional thermal and oxidation stability[iv].
Mobil Delvac Modern™ 15W-40 Extended Performance oil, meanwhile, is a premium synthetic blend, providing extended ODI potential up to twice the average OEM ODI recommendation, or up to 1,000 hours[v].
Leading by example
Mobil™ believes that when it comes to sustainability, working together can lead to real progress. Russell Dickhart is the Global Sustainability Manager within ExxonMobil’s Finished Lubricants business and has spent almost half his career working with customers on solutions to help advance their ambitions
Dickhart described how the right lubricant solutions can help play a key role in helping mining customers reduce their GHG emissions. According to Dickhart: “A key aspect in helping to reduce emissions in the mining sector comes from optimising energy and fuel use. Our Mobil high performance lubricants and solutions can deliver in-use benefits such as energy efficiency and fuel economy that in turn can help lower GHG emissions for our mining customers.”
Mobil recognises that mining companies are also looking for ways to reduce waste and optimise resources. According to Dickhart, Mobil’s advanced lubricants backed by its strong application expertise and services can help do just that, by optimising oil drain intervals and helping extend the life of critical equipment components.
While mining customers work to reduce the impact of their operations, they also want to know that their suppliers are working to do the same.
Dickhart explained that ExxonMobil is continuously looking at ways to reduce its GHG emissions. “As a company, we are pursuing more than US$20 billion in lower-emission investments from 2022 through to 2027,” said Dickhart. “About 50% of our lower-emission investments are targeted at reducing emissions from operated assets, with the balance going toward reducing the emissions of other companies.”
When it comes to waste reduction, ExxonMobil believes in minimising operational waste, and their Finished Lubricants business is leading by example. “Our global network of lubricants blending and packaging plants have a Zero Waste to Landfill Silver validation from Underwriters Laboratories” says Dickhart. “Each year we divert from landfills over 90% of the waste generated in our global lube plant network, and identify ways to redeploy it into new, productive uses.”
According to Dickhart, ExxonMobil is also tackling plastic waste through the expansion of its advanced recycling capacity. By year end 2024, over 80 million lbs. of plastic waste will have been processed at ExxonMobil’s advanced recycling facility in Baytown, Texas. ExxonMobil’s advanced recycling technology transforms used plastic at a molecular level into raw materials to create a range of valuable new products. “And we don’t intend to stop there,” says Dickhart.
For more information on how Mobil can help efficiency in your business, download the free paper below.
[i] https://mine.nridigital.com/mine_jun24/net-zero-strategies-mining-sector
[ii] https://www.mining-technology.com/features/fuels-lubricants-navigating-emissions-reductions-in-off-highway-mining-fleets
[iii] GlobalData: Net Zero Strategies in the Mining Sector
[iv] Figures from Mobil: https://us.lubricants.mobil.com/general/hub/synthetic-diesel-engine-oil?
[v] Please refer to the owner’s handbook for OEM application requirements and oil drain intervals for your vehicle or equipment.
* Results are based on the experience of a single customer. Actual results can vary depending upon the type of equipment used and its maintenance, operating conditions and environment, and any prior lubricant used.