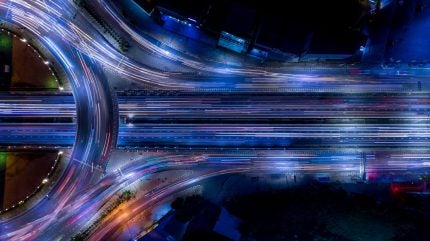
In part one of our five-part series, we take a holistic look at the environmental impact of the rechargeable battery value chain, before addressing sustainability within anode and cathode production in subsequent chapters.
The scale of the environmental impact of mining for battery materials
Electric vehicles (EVs) and battery energy storage systems (BESS) are vital parts of the energy transition and our net zero ambition. However, there is an urgent need to address the environmental footprint of the batteries themselves, to ensure we don’t do more harm than good in transitioning to an electric future.
It is now widely accepted that EVs have a lower lifecycle impact than internal combustion engine (ICE) powered vehicles, even though the carbon footprint to produce EVs is much higher than their ICE equivalents, with 40-60% of that footprint due to the battery.1
“The time it takes for an EV to offset its initial carbon footprint varies based on several factors, such as the electricity mix used for charging, the size and type of the battery, processes used in its production and the fuel efficiency of the ICE it’s compared to,” explains Darryn Quayle, Vice President at Worley
On average, it’s estimated that an EV can offset the emissions from its production within two to three years of driving. This is typically between 19,000 to 50,000 miles, or 30,000 to 80,000 kilometres, with the lower figure contingent on the EV being charged with a relatively clean electricity grid. However, this varies depending on country and electricity mix – and of course the carbon footprint you start with.
While EVs are undoubtably cleaner in the long term, more needs to be done to ensure the advancing decades address environmental challenges across their supply chain.
What makes up the lifecycle impact of a battery?
Focusing on carbon alone (recognising that true lifecycle impact considers a range of other impact categories), cathode and anode materials make up over 50% of the CO₂e contributors to a battery’s footprint. 2
“Upon examining the contributions from individual minerals and the processing steps from initial mining operations to the chemical synthesis of battery components, it becomes clear that the production of this crucial energy transition technology has a significant and poorly understood environmental impact,” says Quayle. By way of example, industry leading environmental consultancy and software development company Minviro estimates that every tonne of lithium mined from hard rock releases 15 tonnes of CO₂.
How demand for batteries is changing the mining industry
Legislation to reduce emissions to zero in major global markets drives EV growth, surging demand for lithium-ion batteries, and the materials that make them. GlobalData’s commodity data forecasts that global lithium production is on course for year-on-year growth of 37.5% in 2024, followed by further rises of 29.7% in 2025 and 21.5% in 2026. Yet amid the reported slowdown in European EV demand during 2023, year-on-year growth of lithium production is expected to soften to 14.2% by 2027 and reduce further to a 5.4% rise by 2030.
Nevertheless, the trend is upward. And the demand curves for other battery minerals are similar.
“The rapid expansion of lithium mining serves as a notable illustration of mining’s contribution to mitigating climate change,” explains Quayle. “We’re mining new materials that were seen as boutique as little as five years ago. Lithium was once largely used in pharmaceutical products and makeup, amongst others. Now, we’re using it extensively in EVs and attention is pivoting to what impact is involved.”
Along with lithium, demand is increasing year-on-year for nickel, cobalt, and manganese to manufacture battery cathodes. To manufacture the anodes, supplies of graphite are also going up. GlobalData’s figures project that the total global production of graphite will almost double from 980,392 tonnes a year in 2020 to 1,861,705 tonnes a year by 2030. It should not be overlooked that synthetic graphite production has the highest CO2e per kWH of all battery materials.
The role of technology and cross-industry expertise
While the ability to identify and quantify the problem using industry-accepted lifecycle analysis standards from firms like Minviro is now possible, a broader response is required to address the challenge. Advancing and deploying technology is essential to usher in an era of low-carbon mining and raw material processing.
“Developing a new technique to reduce the carbon footprint of mineral extraction or processing is futile without the ability to scale, commercialise, and deploy it. We collaborate closely with partners and stakeholders throughout the battery lifecycle – from raw material extraction to battery manufacturing and eventual recycling – to implement low-carbon mining technologies,” says Quayle.
Notable examples to decarbonise mining operations include electrification, streamlining water and energy consumption, adjusting fuel mix, deploying carbon capture solutions and using newer, more sustainable processing technologies. Hybrid power systems that combine renewable and traditional power sources can also ensure a stable and sustainable energy supply.
Worley recently partnered with BluVein to accelerate the deployment of their unique dynamic charging technology, paving the way for heavy haulage electrification solutions suitable for surface and underground mines globally.
“There are also lithium extraction companies and technologies that can get to net zero,” says Quayle.
A UK-based lithium company is well-placed to help change this. Their proposed Teesside, UK, facility aims to produce 50,000 tons of battery-grade lithium a year, estimated to be enough to provide downstream materials for one million electric vehicles while meeting six percent of material demand in Europe. The company claims that its processes will result in a 75 percent reduction in CO2 emissions compared with equivalent lithium refining facilities. The plan is for the facility to eventually run on renewables and hydrogen, with carbon capture technologies deployed where necessary.
“It’s all about the ability to scale, quickly,” adds Quayle. “This is where Worley can play a vital role – de-risking investment decisions and providing decades of experience in complex chemistries to commercialise and prove new technology.”
Quayle continues: “In addition, we look beyond traditional mining activity to identify and support new ways of making and recovering critical minerals. This includes alternative graphite feedstocks from bio-derived materials, using carbon capture and carbon as a by-product to create anode materials, and the opportunity to reprocess tailings to extract value from low grade deposits that were previously a waste stream.”
A green future: The need for commercial viability and scale-up
“Delivering on the ambition of a net zero battery requires new solutions. Often, innovations begin at smaller companies that may lack the resources to scale up,” says Quayle. “To bridge this gap, we’re working with many companies on transformative solutions to support their development and expansion.”
The goal is to establish a robust and sustainable supply chain while meeting demand for battery materials and facilitating the development of new technologies at speed and scale. “This is a new frontier for us,” continues Quayle. “There’s a lot more to-ing and fro-ing as we work together and develop the technology at pace for an industry that desperately needs it.”
The journey to the zero-carbon battery is not about sitting back and waiting. “It’s actively driving the industry in assisting the best in class. That’s a key part of our approach,” adds Quayle. “Worley is increasingly comfortable in that first-of-a-kind space. It’s a challenging place for engineering, but very exciting to be right at the centre of an industrial revolution.”
Join us soon for our upcoming webinar, The Journey to a Net Zero Battery. Registration will open shortly. Learn about the challenges and solutions from expert speakers representing Minviro, Nano One Materials, CarbonScape, and Worley.
To learn more about demand for cathode and anode materials for batteries, download the report below.
[1] McKinsey & Co.
[2] Minviro, Shifting The Lens_WhitePaper_Oct21.pdf