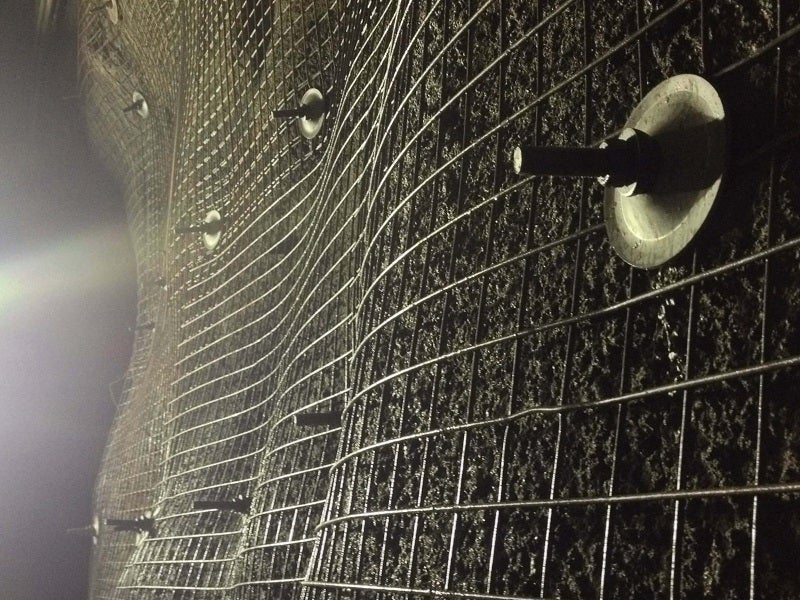
The mining industry is ever-evolving, and rock mechanics are turning to innovative methods to improve the safety, productivity and sustainability of their mines with rock reinforcement. A number of methods have been developed to reinforce rock stability and maintain strata load-bearing capacity of underground excavations.
Rock reinforcement refers to internal strengthening of rock using bolts and injections of resin or cementitious grout to regain competence, which is essential in squeezing and burst-prone strata conditions. External strengthening such as shotcrete and mesh is known as rock support.
Active and passive rock reinforcement
Active reinforcement uses rock bolts and anchors which are pre-tensioned. Bolts are inserted into a drilled hole and pulled, pre-loaded, so that they accumulate energy. The hole is then grouted and the pre-tension is released so that the energized bolt is working against external forces right from beginning. This tightening reinforces and presses the strata together.
Passive reinforcement is a method where a hole is drilled and filled with grout before the steel/glass fibre bolt or cable is inserted, reinforcing the rock like a ligament. Using this method, the bolt is fully-grouted and forces are not being actively applied to the bolt; instead you wait for the strata to start moving or dilating, passively anticipating changes in forces.
Normet’s D-Bolt
The D-bolt is a unique rock bolt, which comprises a smooth steel bar with several anchor points along its length. The full length of the bolt will be inserted into the hole, but it is only constrained to the grout/resin along the anchor points. This enables the smooth sections to deform unrestricted and absorb energy as the strata dilates.
Commonly used fully grouted rebar, made of construction steel, can only stretch up to about 5% until it breaks. The D-bolt’s high-strength, low-alloy steel can stretch more than 20%, enabling greater deformation and a higher load capacity.
The D-bolt has been on the market for more than ten years, and has proven itself to be effective and reliable. Competitors have reverse engineered aspects of the material and design, but few other bolts on the market offer the same properties.
Locally anchored self-drilling hollow rock bolts
Self-drilling bolts are designed to be used in fractured ground or unstable strata where it is not possible to drill a hole before filling it due to the risk of collapse. A self-drilling bolt is drilled into the rock and is left there, and as it is hollow, grout can be pumped through it.
Normet’s self-drilling dynamic bolts (SDDB) are partially threaded so that they can be extended with a coupling, meaning they can be used in place of long cable bolts that are difficult to install.
The SDDB bolts reinforce strata by limiting dilation between anchor points. When the rock mass expands, the anchor points bear the load and the smooth section elongates. Due to the steel material’s strength and deformation properties, the bolt can effectively absorb dilation energy.
Normet bolts also offer high shear resistance. When excavating underground tunnels, strata needs to tightened together to stop it moving or sliding. Standard bolts usually have a shear strength that only matches up to 60% of its tensile strength. Normet SDDB systems have shear strength between 80-90% of its tensile strength, making underground conditions much safer.
Visit Normet’s website for more information about the D-Bolt and Self-Drilling Anchor systems.