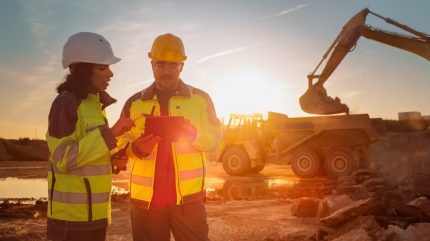
A new survey by marketing intelligence firm GlobalData reveals that 8% of miners worldwide are already noticing the impact of AI on their operations, but 37% expect AI to impact their operations within the next one to five years.
“AI enables mining companies to use autonomous machinery and data to improve efficiency and productivity and reduce downtime,” a GlobalData report on AI in mining says. “Autonomous machinery can also reduce the requirement for on-site workers, removing them from potential hazards and improving safety.
“AI can help companies better understand the environment and terrain where exploitation is to begin.”
Mining companies are focused on AI
GlobalData’s 2024 survey of 160 mines around the world finds that a large share of companies recognise the urgency of investing in AI-powered solutions. GlobalData’s latest mine-site technology adoption survey asked the question: “Which of the following do you expect to invest in/ invest further in, over the next two years?”.
The six options that received the most votes are all related to AI, showing how mining companies are deploying AI and what areas AI is transforming mining.
Over the next two years a high share of mining operations expect to invest in predictive maintenance for mobile equipment as well as mine scheduling, planning and management software.
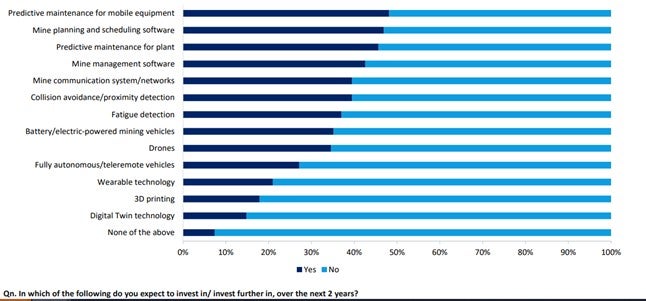
The survey, conducted between March and May 2024, shows that more than half of mines have already made significant investments in, or fully implemented, mine planning and management software, predictive maintenance for plant and mine communication systems. More than 70% of the respondents said they had already made at least moderate investments in predictive maintenance for their mobile equipment – that’s when AI is utilised to analyse sensor data from mining equipment and machinery, identifying patterns that indicate potential equipment failures or maintenance needs.
“By implementing predictive maintenance strategies, mining companies can schedule maintenance activities proactively, reducing unexpected downtime and optimising equipment performance,” says the GlobalData report on AI in mining.
“This approach minimises costs associated with unscheduled repairs and maximizes overall operational efficiency. Reactive maintenance costs enterprises billions each year in lost production.”
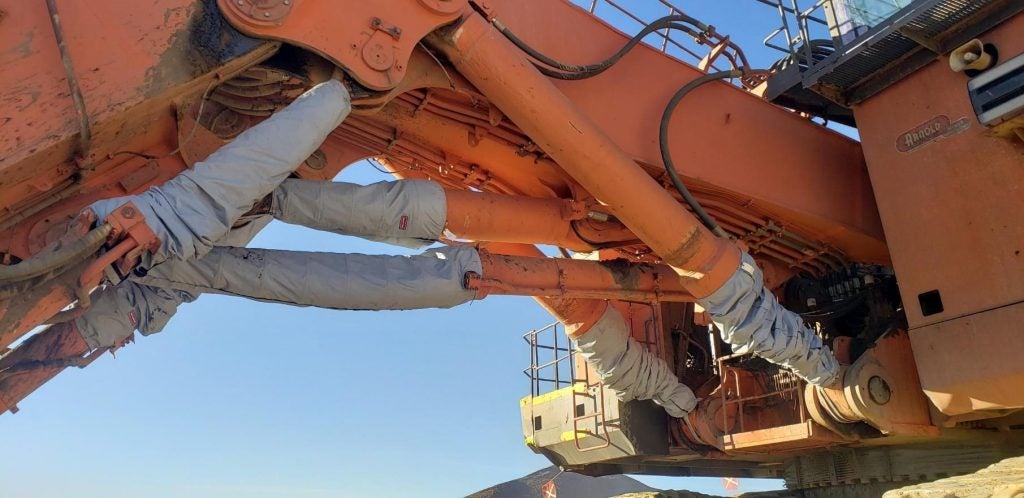
The goal is not to replace machines or parts too early but service them at the right time. AI-powered solutions can also be used to optimise resources such as fuel, water, and energy in mining operations. By analysing data from various sources, including weather conditions, equipment performance, and production targets, AI systems can optimise resource allocation and consumption.
Enhancing productivity is a priority
It seems mining companies recognise the powerful productivity and cost gains of deploying AI technology for this application – with almost half committing to invest further, or for the first time, in predictive maintenance. Mines are also investing in collision avoidance technologies (40%) and fatigue detection (37%) to improve uptime and prevent accidents.
This is perhaps not surprising when you consider that macroeconomic pressure ranked the top risk for the sector in the first three months of 2024, according to GlobalData analysis of mining company earnings reports over the financial quarter.
“Mining companies have a lot to deal with over the next few years,” says Leigh Carlson, CEO of US-based mining OEM Fluid Control Services. “There’s inflation in mining operating costs, labour shortages and an environment of declining ore grades, which means locating new mineral deposits and determining the economic feasibility of extracting viable resources is a big challenge and means longer haul distances. Productivity can be particularly impacted by machine breakdowns.”
Machine learning technology and algorithms can be used to determine how well a machine is functioning and flag signs of emerging problems, Carlson says mines and mine machinery suppliers shouldn’t underestimate much lower cost investments that can have outsize ROI in terms of proactive maintenance solutions.
Fluid Control Services manufactures makes a Seal Saver ‘boot’ which protects seals and cylinder rods on mining machinery against premature failure. Carlson says it’s an obvious solve to keep hydraulic equipment – this includes trucks, loaders and excavators – running in tough environmental conditions, proven to double or even triple the lifespan of a hydraulic cylinder.
Resistant to heat, oil, chemicals, and water, the Seal Saver is manufactured in the US, from a wide range of materials, and is custom designed for each application to ensure the best protection for each machine.
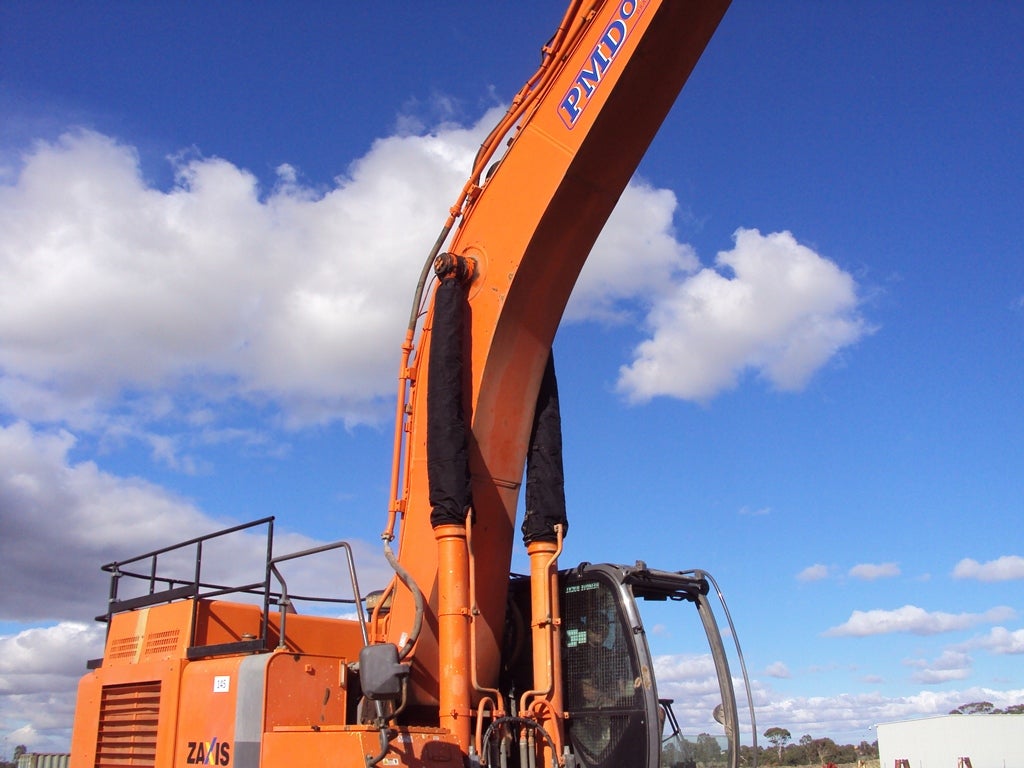
“Repairing a hydraulic cylinder could cost anything between US$2,000 and US$20,000. Then, of course, there are the costs associated with the machinery not being in operation. Almost all repairs will have a higher cost than the purchase price of a Seal Saver,” says Carlson. “It’s a low-tech product, yet unique and does an excellent job of protecting cylinder rods from dirt and pollution ingression.
“It seems the integration of AI into mining equipment and machinery could have a positive effect on the lifetime of these boots and therefore hydraulic systems. It’s logical that less operator error means fewer collisions into sharp rock walls for these machines, which means less debris clogging up the hydraulics.”
Discover how the Seal Saver can support your business in saving costs and boosting efficiencies in a challenging cost environment by downloading the report below.