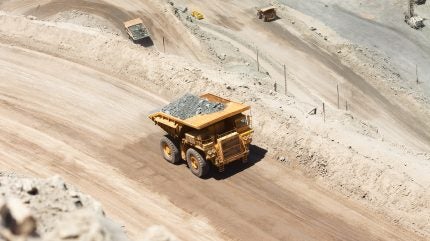
Our partner, a taconite mine in northern Minnesota, has a long history with using Mobil Delvac 1ESPTM synthetic engine oils in their fleet of 30 Komatsu 830E haul trucks, powered by Cummins QSK 60 engines. Over time, the mine has increased engine oil drain intervals up to 2000 hours and has realized increased equipment availability and production levels. This success is attributed to using the best Mobil lubricants combined with a disciplined, data-driven approach taken by their reliability team towards maintenance.
The mine has already realized over $900K in annual savings from this program.
The mine strives to be a leader in the iron ore industry through safe workplaces, operational efficiency, and environmental stewardship. As part of meeting this ambition, the Mobil ServSM Engineering team and the reliability team at the mine wanted to know what else could be done to improve efficiency at the mine.
The challenge identified: Can we safely extend our engine rebuild cycle beyond 28,000 hours?
One truck was selected for extended testing – which represented the typical condition of the fleet’s engines. This unit was at 28,000 hours and oil
analysis continued to show very low wear metals with no notable wear progression. In addition to oil analysis, an in-truck load test was completed to gauge engine output horsepower. This test confirmed no power loss in the engine, which helped
confirm the lack of wear shown in oil analysis.
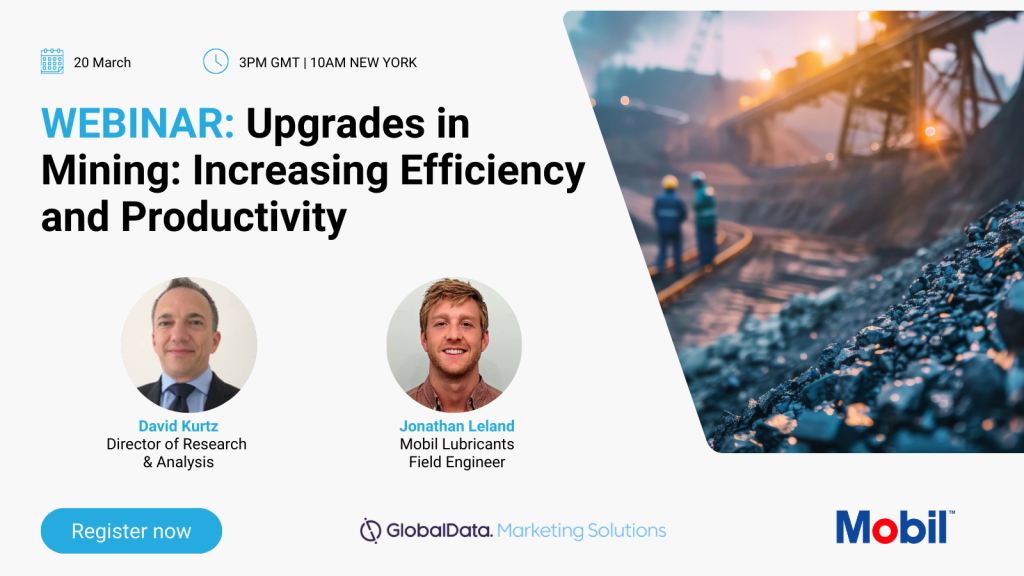
The team was confident that the engine could still perform well, and decided to leave it in service until it reached 36,000 hours. And they were right! Extensive testing on the engine at 36,000 hours proved it could even have gone further.
The results
“This new strategy will deliver significant savings to our partner, as the total benefit calculated is over $1.7 million dollars.” Jonathan Leland, Mobil Serv Lubrication Engineer, Minneapolis, MN
Engine dynamometer testing: The first test completed after the engine was taken
out was dyno-testing at a Cummins facility. The results were impressive – crankcase blow-by was still within spec of a new engine. Horsepower ratings also confirmed the outstanding condition of the engine. Again, the engine was still within specifications of a new engine showing a horsepower output of 94%.
Engine rating: The next step was to inspect the engine after it was taken apart. This was done in collaboration with the ExxonMobil Research and Engineering (EMRE) team of experts. EMRE employs ASTM certified parts raters including Victor Veiga, who has over 30 years of experience working with engine testing and evaluations.
Main bearings: The majority of the bearings have very minimal wear and are in very good condition. 10-15% worn area is very good for this engine and duty cycle. This
indicates consistent protection from the oil throughout the life of the engine. Based on the full results, the average wear and exposed copper is very impressive for an engine of this age and operating under severe duty cycle.
Pistons: This is an area where poor engine oil will lead to more carbon deposits and more wear. As a whole, these pistons are very, very clean — this is proof of how Mobil Delvac 1ESPTM has helped maintain cleanliness of the engine.
Piston liners: The interface between the pistons and liners is an area where poor oil performance will show itself in a telling wear pattern. If the oil is not protecting well and begins to break down at longer oil drain intervals, this area of high heat and combustion materials will show the oil’s lack of performance. The original cross-hatching is still visible and the travel vs. non-travel areas look the same.
Valves: Intake valve rating gives a sense of the air quality coming into the piston, while exhaust valve rating tells of the quality of combustion gas leaving the piston. Without proper air filters and poor combustion, these valves can become very dirty
and begin wearing the valve seats (sealing surface). Again, we see very impressive results! The majority of the valves from this engine show less than 20% coverage and all intake and exhaust valve surfaces were clean, and free of wear on the valve
face and stem.
Conclusion
The overall condition of the engine was extremely good based on the number of hours and severe duty cycle. Based on the team’s findings, the mine is going to extend haul truck engine rebuild strategy to 40,000 hours. This enables increased haul truck utilization and decreased haul truck operational costs and advances the mines ambitions through proven engineering data.