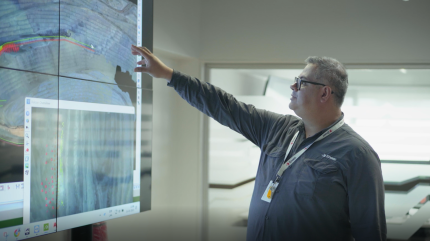
The mining sector has always faced challenges around conducting operations within remote and harsh environments. With limited connectivity, performing effective data analysis and ensuring the security of both the location and the people who work there can be daunting. Mining companies also need to assess and reduce the environmental impact of their business to comply with climate policies that are becoming more rigid as well as to reassure investors and society at large that they are playing their part in displaying environmental, social and governance (ESG) stewardship.
All this while striving to reduce costs and boost operational efficiencies at a time when extraction is involving the exploration of even more remote and hazardous locations.
Transformative effect
Against this backdrop, advancing internet-of-things (IoT) technology has had a transformative effect across the whole mining value chain. Describing the use of connected sensors and actuators to monitor the environment, the things that move within it, and the people that act within it, IoT technology is enabling greater automation across operations, from using drones in feasibility studies to tele-remote and fully remote logistics and haulage systems.
“Autonomous vehicles can use pre-defined GPS courses and sensors to navigate haul roads and intersections automatically, perform much longer hours than humans, and require less staff. Robotic inspection technology can generate higher-quality data than human inspectors, and do so more quickly,” says David Kurtz, director of research and analysis, for construction, mining and energy at market intelligence firm GlobalData, which tracks deal activity, investment and hiring trends in the sector as well as the state of mining projects in 150 countries.
Blasting is one of the most dangerous activities in a mine. It also can be time, energy and cost intensive and there are lots of aspects that can go wrong that can snarl up operations. For example, if the fragmentation distribution isn’t right for the crusher, the crusher could pack up and work could cease during repairs. In an extreme scenario, a bad blast could be a serious catastrophe if it spoils a part of the mine designated for excavation or on the site of an area where a road had been planned.
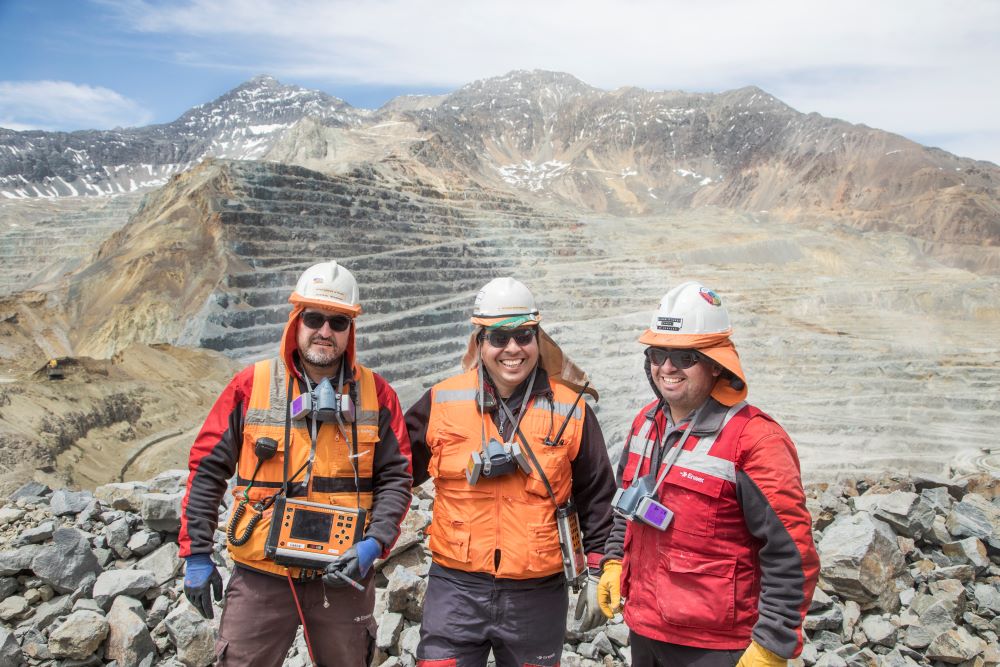
IoT technology has enabled Chilean blasting solutions company Enaex to create a unique digital platform that uses neural networks and machine learning to improve blast results and blast operations efficiency. It’s called Enaex Bright.
In a short Q&A, Enaex corporate R&D director Riaan van Wyk talks about how mining companies are navigating the modern world and the biggest challenges holding up digital transformation in mining.
Riaan, how does the mining industry stack up against other industries in terms of its willingness to invest in digital transformation?
I think most bigger mining groups do see the value of digital solutions to improve efficiency. The hurdle is not vision. The resistance to change is not really an issue anymore. Twenty years ago, the average mine worker was super conservative and did things by gut feel. But over the years, the whole culture of mining has changed. Now mine workers tend to be more sophisticated and working with digital tools is ingrained. The biggest challenge now is the difficulty in accessing a reliable data connection in such a dynamic environment. In open pit, Elon Musk’s Starlink satellite internet provider is helping with this as is Long-Term Evolution (LTE), but in underground mining, this is still a challenge. One of the things we are exploring are mesh networks. We are working on developing a store-and-forward system that will be able to capture much more data from the mine site that we can use to feed into Enaex Bright so that it can help mines make more effective decisions related to blasting.
Once there is resolution to the data challenge, I believe most mines will see the true value of how digital transformation can improve mining efficiency and planning.
Tell us about what you’re seeing in terms of innovations in data analytics and data-driven decision making in mining?
In terms of mining explosives and blasting, over the past years the industry has generally been using empirical design methodologies as a rule to make decisions. These were based on past human experiences and are static and generic. Enaex Bright is a fairly new model, which uses AI technologies to auto-learn and auto-correct and so the more a mine site uses it, it will learn which decisions were good and which could have been better. The neural network that powers Bright will use a generic geology model built from data ingested from other mines. It will then collect new data on drill speed and torque and other significant measurements, like rock hardness and fragmentation distribution, and then use this data to build a more relevant, customised model, supporting the mining company to drill fewer holes, deploy fewer explosives and therefore reduce energy and cost.
The better the data in the system, the more accurate predictions can be. With enough data, a better digital twin for the mine can be developed, and this will help to sustain the mine’s extraction capacity.
What’s the next step for Enaex with regard to innovating in this area?
At this stage we are using neural networks to plan drill patten density and explosive charge volumes using rock hardness prediction. We will soon introduce more models that can also predict presence of water in a blast hole. We are also working on neural networks that will optimise the explosive truck fleet deployment and we will soon introduce autonomous robotics blasting deployment systems in efforts to make mining safer for workers. Interoperability is the next step. I see a future where the whole process of mine planning, blast planning and automation is modelled in the digital domain.
Once you include all the movable assets in the mine planning process you can extract more value faster with less input cost.
Discover how Enaex can help your operation make better blasting decisions through Enaex Bright in this free guide