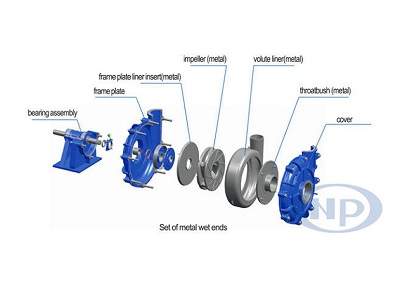
Wet ends are the main parts of a slurry pump, including cover plate liner, frame plate liner, rubber impeller or metal impeller, volute liner, frame plate liner insert and throatbush. Material of the wet ends is an important parameter, which determines the lifetime of a slurry pump. Naipu self-developed rubber largely prolongs the lifetime of wet ends.
Material of wet end parts
Wet end parts of slurry pump can apply many materials, which are mainly classified into metal wear-resistant material and natural rubber wear-resistant material. Practice has proved that rubber has the better abrasive resistance and better acid-resistance. Rubber is suitable for transferring fine or medium particles without sharp edges, so the max. diameter of particles transferred by rubber-lined slurry pumps should below 10mm. Meanwhile, rubber cannot be used to transfer slurries with hydrocarbon, oil or grease, or transfer slurries over 80°C. If the impeller is made of rubber, the rev. should be lower than 28m/s. In consideration of all these factors and conditions, the wet end parts of Naipu slurry pumps can be divided into the following four kinds:
R (Rubber impeller + rubber liners + rubber throatbush) is applicable for:
- Normal temperature, less than 80°C
- Slurries with fine or medium particles
- Low or medium head
- Mineral oil free
- Ball mill discharge, tails conveying
MR (Metal impeller + rubber liners + rubber throatbush) is applicable for:
- Normal temperature, less than 80°C
- Slurries with medium or coarse particles
- Froth slurry transferring
- Heads over 60m
- Mineral oil free
- Discharge of AG mills, SAG mills and grinding rollers
M (Metal impeller + metal liners + metal throatbush) is applicable for:
- High temperature, over 80°C
- Heads over 60m
- Transferring mineral contained oil
MMR (Metal impeller + metal throatbush + rubber liner) is applicable for:
- Slurries with medium or coarse particles
- Froth slurry transferring
- Heads over 60m