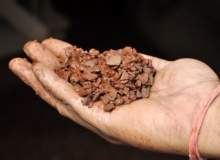
CDE Global’s experience in the delivery of turnkey processing plants across four divisions ensures the company understands clients’ requirements and delivers a processing system that is fit for purpose.
CDE Global’s building block structure allows for modifications to the plant set-up to be made quickly and easily, as and when required.
This enables changes to capacity, final product specification and feed grading to be accommodated and to achieve the following:
- Maximise yield
- Reduce alumina and silica levels
- Simple operation
- Consistency in final product specifications
- Minimum cost of ownership, maximising plant life through the specification of high-quality components:
– Xtril cyclones
– Modular polyurethane screen panels
Developed over many years, CDE Global selects only the best materials suited to the demanding environment and abrasive nature of iron ore, which includes the following:
- Increase in thickness and strength of polyurethane screen media to increase wear life but also to support the heavier ore
- Xtril lined cyclone, proven to increases life to typically one to three-years compared to two to three months for rubber on similar applications
- Replaceable Hardox liners in hopper bin
- Conveyor belts upgraded to a tougher more durable mining specification belt with additional top cover thickness
- Tungsten tip scraper blade for increased life on abrasive crushed ore, while providing superb clean ability
- All mining duty slurry sumps are rubber-lined and only use a mining pump
- Conveyor feed boots lined with polyurethane to maximise production time
- Feedboxes’ with replaceable 20mm polyurethane liners