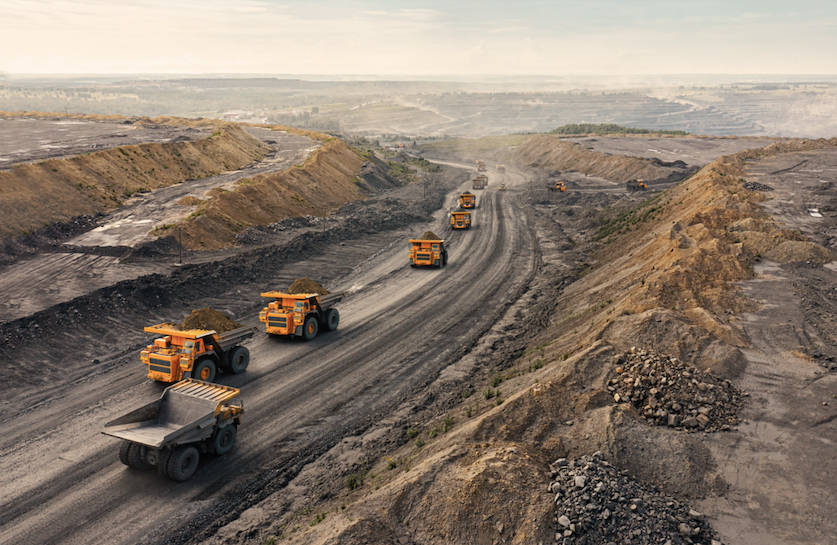
Mina Esperanza is a gold mine in southern Peru, situated in the Andes mountains among the Nazca-Ocona geological gold belt. In the past, the facility struggled to make profits due to the high cost of extracting metal from low-concentration ores. When the low-grade ores were discarded for lacking economic viability, it raised environmental concerns about metals left in the dumps.
Excessive metal extraction to meet industrial demand has, over the years, has led to a shortfall of high-grade ores. Studies find that a decline in an ore’s metal content is an indicator of resource depletion. A research analysis of major copper mines across the world found that the average decline in ore grade was 25% in just ten years of mining deposits.
However, mines like Mina Esperanza have turned their fortunes around with the use of a sensor-based sorting technology, making the mines profitable. Sensor-based ore sorting technology involves using sensors to detect the mineral content of each piece of ore and sorting it based on its composition. This technology has revolutionized the mining industry by allowing mines to extract more metal from low-grade ores.
In addition to the functional and financial significance, the use of sensor-based ore sorting technology has proven environmentally viable. The crushing and grinding of ores consumes around 60% of a mine’s operating and energy costs, while also adding to greenhouse gas emissions. The sensor integration allows the mines to reduce the waste produced, cutting their waste disposal, saving water and consuming less energy to process the ore.
El Teniente in Chile is the world’s largest underground copper mine using sensor-based ore sorting technology. Before the implementation of this technology, the El Teniente mine was only able to extract copper from ores with concentrations of 0.7% or higher. However, sensor sorting has allowed the mine to extract copper from ores with concentrations as low as 0.4%.
With increasing governmental compliance criteria and accountability of miners to environmental groups, the use of sensors can help mines create a circular economy of natural resources while addressing of their environmental impact.
How does sensor-based ore sorting work?
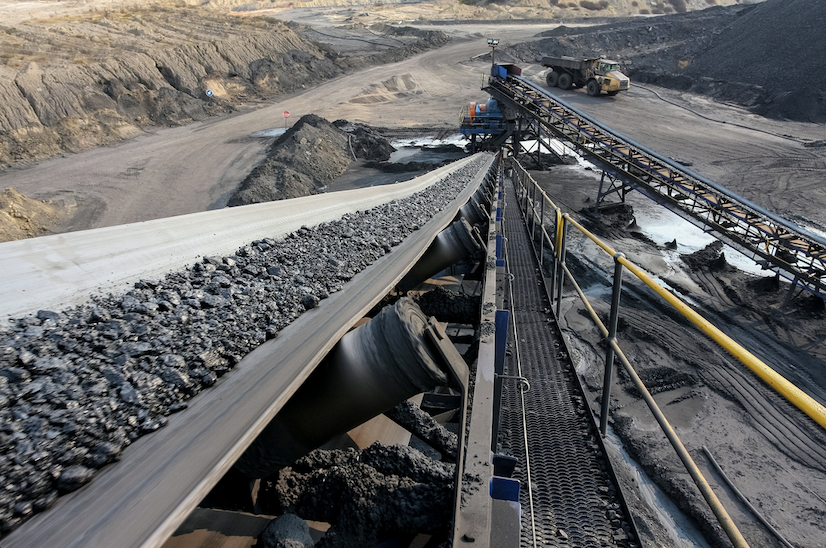
Sensor-based ore sorting relies on the basic principle that different minerals have different densities, shapes, and electromagnetic properties and these differences can be used to separate them from each other. The sensors are mounted on conveyor belts or chutes and as ore passes by, they emit a signal that is analysed by a computer to determine the composition of the ore. Based on this, a mechanical sorting system separates the ore into different streams.
Sensor-based sorting is typically used for particle sizes ranging between 0.5 to 300 mm.
By separating the valuable minerals from the waste rock early in the mining process, the overall efficiency of the mining operation is improved, as less energy is required to process low-grade ore. The most widespread sensor sorter in the mining industry uses x-ray transmission, followed by colour-based sorters and lasers.
Sorting ore densities using x-ray sensors
X-ray transmission for ore sorting is used when rocks vary in density. The application of x-rays ranges from separation of scrap metals into light and heavy metals to detecting the elemental composition of a material. This allows for more efficient and cost-effective extraction of valuable minerals from the ore, as only the portions of the low-grade ore with significant concentrations of the desired minerals are processed further.
Steinert, a German manufacturer of sensor-based sorting technologies has taken x-ray sorting one step further with fluorescence lighting. Its Steinert KSS XF-L fluorescence sorting system can distinguish copper from brass or zinc based on the presence of inherent elements. Though the heavily-soiled surfaces could confuse detectors, Steinert’s newer machines are installed with automatic cleaners for the scanning area. This ensures a consistent detection quality while reducing the manual labour and water usage involved in cleaning.
Meanwhile in China, the Fankou mine range containing Asia’s largest lead and zinc mines added $9.22m to their annual revenue with HPY Technology’s low-grade x-ray sorting sensors. Combining x-rays with high-speed air jets to sort waste rocks, Fankou has been able to achieve a zero-wastage target in its operations. Producing about 1.4 million tonnes of ore per year, the mine operators separate the waste rock as construction aggregate, yielding more than 1,500 tonnes per year, amounting to $9m in revenue.
Colour-based sorting detects beyond the human vision spectrum
Colour sorting has been traditionally used for separating valuable residues from waste rocks. However, the detection of colour is usually associated with the perception of the human eye. While our brains can perceive colours in the visible light spectrum, of approximately 400-780 nanometres, the spectrum ranges between ultraviolet and infrared, neither of which are visible to the naked eye.
Steinert’s colour sorting sensors can detect up to 16.8 million colours with rapid response times and high light intensities. One of the most innovative applications of sensor-based colour sorting in mining is in the sorting of diamonds. Diamonds are valued for their purity and colour, and even a slight variation in colour can mean the difference between a valuable gemstone and a worthless rock. By using advanced colour sensors, mining companies can quickly and accurately identify and sort diamonds based on their colour, allowing them to extract the most valuable stones from the ore.
In low-grade ore mining, the mineral content is often spread over a large area, making it difficult and expensive to extract. Copper is often present in the ore along with other minerals, such as quartz and feldspar, which have little value. By using colour-based sensors, the mining company can sort the ore and separate the copper-rich portions from the worthless rock, reducing the amount of material that needs to be processed and increasing the yield of valuable minerals.
Near-infrared sorting separates differences invisible to human eye
Near-infrared sorting sensors use light in the near-infrared spectrum (760-2500 nanometres) to analyse the chemical composition of minerals in the ore. This can allow mining companies to sort the ore based on its quality, value and complex mineralogy.
By analysing the chemical composition of the minerals, near-infrared sensors can distinguish between minerals that might otherwise be difficult to differentiate, allowing for more efficient sorting. With its high spectral and optical resolution, Steinert’s sensors can observe molecular vibrations at very fine resolutions.
Because low-grade ores point to a decline in resource deposit, sensor-based ore sorting can pave the way for a circular economy of zero wastage. According to the International Mining for Development Centre, sensor-integrated technology already facilitates a reduction in water usage of up to 30%. While the cost of investing in sensor-based technologies may be a factor of concern for small companies, the sensor automation market is expected to grow at a compounding annual growth rate of 8.4% until 2032. As the pressure on the environment and resources increases, sensor-based sorting presents an actionable model to utilise resources in keeping with sustainability.