
Although impressive strides have been made to improve worker safety in the mining industry, miners still face one of the world’s most perilous working environments on a daily basis. Mining companies have often been reticent to invest in non-core technology upgrades in the past, but new devices and software can make the difference between life and death.
Here we profile some of the industry’s most impressive safety technologies, both to respond to emergencies when they arise, and perhaps more importantly, to prevent them from happening in the first place.
How well do you really know your competitors?
Access the most comprehensive Company Profiles on the market, powered by GlobalData. Save hours of research. Gain competitive edge.
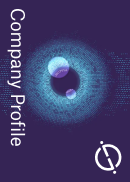
Thank you!
Your download email will arrive shortly
Not ready to buy yet? Download a free sample
We are confident about the unique quality of our Company Profiles. However, we want you to make the most beneficial decision for your business, so we offer a free sample that you can download by submitting the below form
By GlobalDataCaterpillar’s intelligent mine management
In response to the increasing need for improved safety systems in mines, Caterpillar introduced a new generation of integrated mine management software in 2011, Cat MineStar.
Following the theory that an intelligent, integrated management system, which combines several measures under the same roof, is the best form of incident prevention, the software builds on existing individual Cat systems.
The system consists of five sub-modules: Cat Terrain is an intelligent earthmoving system, Detect encompasses sensing and reporting systems that assist operators in avoiding collision and Fleet provides real-time tracking, scheduling, assignment and productivity management.
Cat Health delivers vital event-based machine condition and operating data for the mining fleet and Command includes remote control, semi-autonomous systems for surface and underground mobile equipment.
In order to cater to the individual needs of mines, the system’s five modules can operate in stand-alone applications or be combined with the other capability sets.
"Each of the capability sets has its own functionality and feature set, but they are designed to be flexible and scalable. Each mine can define its own needs, and add capability sets as required," said Cat’s commercial manager Annette Slyman.
Permit-to-work authentication
A key aspect of incident prevention is impeccable people management and a fundamental foundation of people management is ensuring that all workers are authorised to carry out their given tasks.
The permit-to-work system is a widely recognised safety standard in the mining industry as a means of tracking the authorisations and competencies of employees as well as identifying the key risks involved with a particular job. Mining permit-to-work systems have tended to rely on cumbersome paper systems, but a new generation of software is encouraging many mines to digitise the process.
South African software company ApplyIT’s IntelliPERMIT system, for example, integrates all aspects of permits-to-work, access control and risk assessment, improving visibility of all works taking place, tracking each employee’s authorisation levels and tying permits into access control with biometric fingerprint identification.
IntelliPERMIT was recently installed at Newmont Mining Corporation’s Boddington mine, currently Australia’s largest gold producer.
Intelligent injury response
If an accident does happen, emergency response has to be fast and effective, especially in remote mining areas. The use of an intelligent life care system can provide faster and more accurate on-scene support and diagnosis until professional emergency services arrive.
For this purpose, Honeywell Intelligent Life Care, in collaboration with UK-based Safe Patient Systems, recently launched the Safe Triage Lite, a small and robust, fully-automated hand-held triage solution.
The system uses multiple communication channels including WiFi, GSM, 3G and portable satellite integration to enable the delivery of patient information to medical professionals.
They in turn can assess a patient’s condition including the use of still images, video and vital signs, allowing the patient to receive diagnosis and treatment within minutes.
According to Honeywell, the device can easily be used by non-medical personnel due to its easy-to-use interface, its step-by-step guidance and the comprehensive built-in medical and drugs database, therefore saving lives in difficult to reach mining operations.
Mobile proximity warning systems
Installed in nearly every vehicle, mining proximity warning systems are an essential tool to keep mines safe.
In open pit mines, they work as traffic alerts and collision avoidance systems and warn operators with audio and visual indications of possible collisions, speeding or rollovers. In addition, the systems also help to improve drivers’ traffic awareness, especially in blind spots around their vehicle.
Nonetheless, the number of accidents involving people working near heavy machinery and powered haulage is still very high, accounting for a total of 84 deaths in 2003-2007 in the US alone, according to the National Institute for Occupational Safety and Health (NIOSH).
In response to the problem, the institute has now developed an active proximity warning system, called the Hazardous Area Signaling and Ranging Device (HASARD).
It warns workers as they approach dangerous areas around heavy mining equipment. The system consists of a transmitter that generates magnetic fields around hazardous areas, and a receiver that is a magnetic field strength meter.
The worker, who wears the receiver, gets visual, audible and vibratory indicators to warn of approaching machinery.
Wireless methane sensors
Methane gas, which is released in the process of coal mining, is a common cause for accidents in mines. The natural gas is odourless, colourless and highly flammable and can explode violently. Methane detection equipment has therefore been in place for several years and almost certainly prevented some deadly accidents in mines worldwide.
Tunnel Radio of America has now introduced a wireless detection system for methane gas and carbon dioxide (CO2), according to the company the first of its kind.
Designed for use with a RFID [radio frequency identification] tracking system, it deploys a multitude of sensors in coal mining environments. The information is transmitted wirelessly to surface computers from the primary methane sources deep in a mine, together with tracking of personnel location.
According to Tunnel Radio, the sensors may operate for months on battery power, working 24 hours a day. The biggest benefit is that it can be placed exactly where needed – a shortcoming of currently wired technologies. In addition, the CO sensor warns workers of unsafe thermal conditions, giving them time to react before the potential outbreak of a fire.
Locating trapped miners
One of the hardest tasks for rescue teams after a mine collapse or explosion is finding and communicating with survivors. Without relatively accurate information on the whereabouts of underground workers, drilling down into a mine could do more harm than good.
Current technologies based on RFID have an accuracy of around 50-500ft, making them of little use in a high-pressure rescue operation, while GPS satellite location systems can’t penetrate underground mines.
In the last few years, however, new declassified military technology called inertial navigation has brought underground location systems closer to the pinpoint precision that is expected of them.
Inset Systems’ new tracking and communication device, for example, uses inertial navigation technology to track a miner’s direction and velocity without needing external references and is accurate to within 25ft.
The tracking unit, one of the first to hit the market and approved for use by the US Mine Safety and Health Administration (MSHA) in February 2011, also enables two-way communication by voice or text. As sophisticated technologies like these mature on the market and come down in price, it seems likely they will become a staple in safety conscious mines that are aware of their benefits in a potentially life-or-death situation.
Dust monitoring
The build-up of various types of dust during the mining process holds a number of hidden dangers for underground workers. The two main health issues revolve around the explosive nature of airborne coal dust and the inhalation of harmful silica and respirable coal dust.
NIOSH, which has been spearheading mining safety technology efforts in the US since the MINER Act of 2006, has been taking the lead on developing and commercialising devices to help combat these dangers.
NIOSH’s coal dust explosibility meter (CDEM) provides real-time, instant feedback on the safety-critical ratio between inert rock dust and coal dust (MSHA stipulates that rock dust should constitute no less than 80% of this mix in all mined areas outside the return airway).
After years of extensive field testing, the device has now been made available to the market through Sensidyne.
NIOSH has also been developing and testing a new personal dust monitor (PDM) to give miners a tool to track their exposure to respirable coal dust in real-time. According to the institute’s tests, the PDM has proven its effectiveness in a coal mine environment and the immediacy of its data could prove key to miner safety, as current sampling equipment can take days or even weeks to provide feedback.
However, NIOSH is still looking into incorporating new filter materials into the device, as its original filter has thus far been unable to analyse silica, which can cause deadly outbreaks of silicosis, on dust samples.
Robotic rescue systems
In the event of a catastrophic mining explosion, like those that have occurred at Pike River in New Zealand and Upper Big Branch in the US in the last couple of years, rescue operations are incredibly difficult to conduct because pockets of deadly fumes or the potential for further explosions often prevent human rescuers from even making the attempt.
Although, for the most part, robotic rescue systems remain a future technology for the mining industry due to a lack of industry investment, the ANDROS Wolverine robot that Remotec developed for MSHA and which ventured into Sago Mine after an explosion in 2006, could provide a blueprint for the mine rescue robots of the future.
With deadly explosions still a major problem for the global mining industry – particularly coal mining – the ready availability of high-tech, sensor-based robots that are customised for dangerous underground environments seems like a more pressing need than ever.
By Elisabeth Fischer and Chris Lo