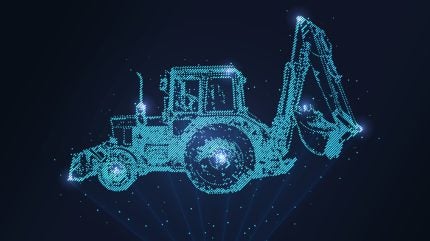
The failure of mining equipment can be devastating. By any measure its impact can be staggering, both in terms of financial cost and lost productivity.
Although estimates often widely vary, breakdowns can halt production to the tune of thousands. A failed dump truck, for example, can cost as much as $1,000 per hour; while the breakdown of a reclaimer could result in $1,000,000 in lost production each day it is out of service, according to software and technology provider Akselos.
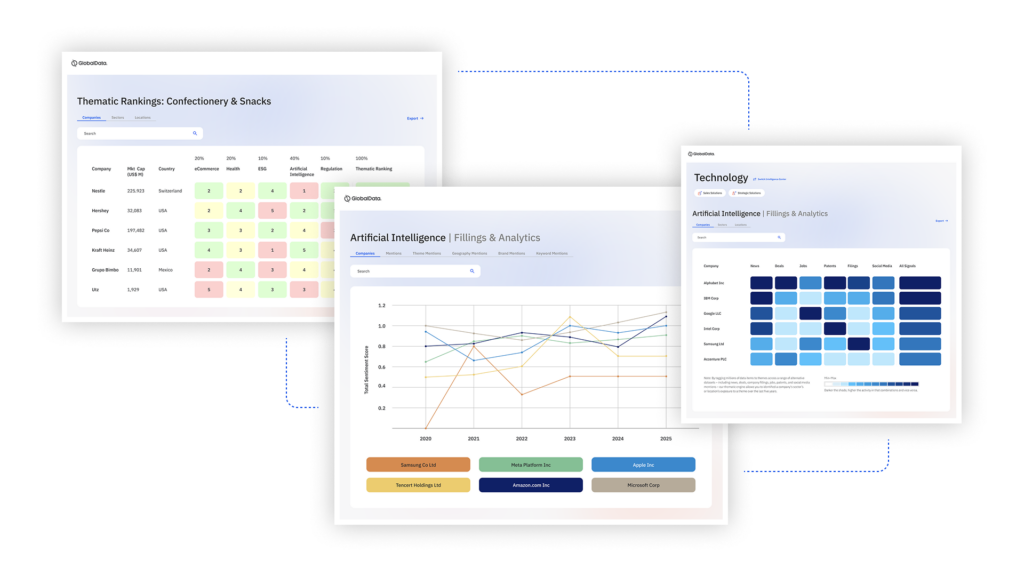
US Tariffs are shifting - will you react or anticipate?
Don’t let policy changes catch you off guard. Stay proactive with real-time data and expert analysis.
By GlobalDataWith these troublesome statistics, it is little wonder that 30–50% of total mine operating costs can be down to maintenance.
“Mines represent complex, multi-domain and multi-stakeholder operations where low agility and high uncertainty significantly impact profitability,” explains Nokia Bell Labs’ Lelio Di Martino, head of network application research.
It is not uncommon for mines to experience millions of dollars in lost productivity due to unplanned equipment maintenance, or suboptimal decisions made manually with a limited view of the mine’s real-time status, he says.
Mines increasingly employ predictive maintenance
Because they result in such costly upheaval, it seems mining organisations are becoming clear on the need to protect against losses caused by mechanical failures.
Market intelligence provider GlobalData says that over the next two years many mining operations expect to invest in predictive maintenance for mobile equipment, mine scheduling, planning and management software. In its recent survey of mining stakeholders, asked which of 14 areas companies believed they would prioritise investment in, the leading category was predictive maintenance.
Di Martino says predictive maintenance – which involves using sensors to collect data, modelling and, increasingly, AI – as opposed to preventative maintenance helps identify equipment with the potential to cause downtime in the coming hours or days.
Predictive maintenance is not new; the use of these technologies has ramped up over the past decade or so thanks to their advanced analytics capabilities which, as mines are finding out, when used properly can lead to improved decision-making and increased efficiency.
Digital twins: a workhorse for predictive maintenance
Although predictive maintenance makes use of a network of sensors, huge amounts of data capture and the ability to distil and interpret it via models, the digital twin is the workhorse. These digital representations of real-world assets and operations, with precision accuracy, are gaining interest and traction across multiple industries – mining being no exception.
Crafted to understand, optimise and predict the performance of assets or processes, Di Martino says gathered information, alongside AI, can be used to develop and feed digital twin models, leading to actionable intelligence that can inform decisions.
“The primary role of digital twins in mining is to offer AI-powered data correlation, quantifying and predicting the impact of operational decisions across various dimensions to achieve planned business goals, such as the number of tonnes of ore produced per day,” he says.
Benefits of digital twins beyond mine maintenance
Digital twins don’t just offer maintenance benefits: they can optimise processes and increase productivity across the mine, such as in blasting and drilling; improve mine sustainability through the collection of actionable data on operational emissions, energy and water consumption, among others; and above all, improve safety, from training to increased remote operations.
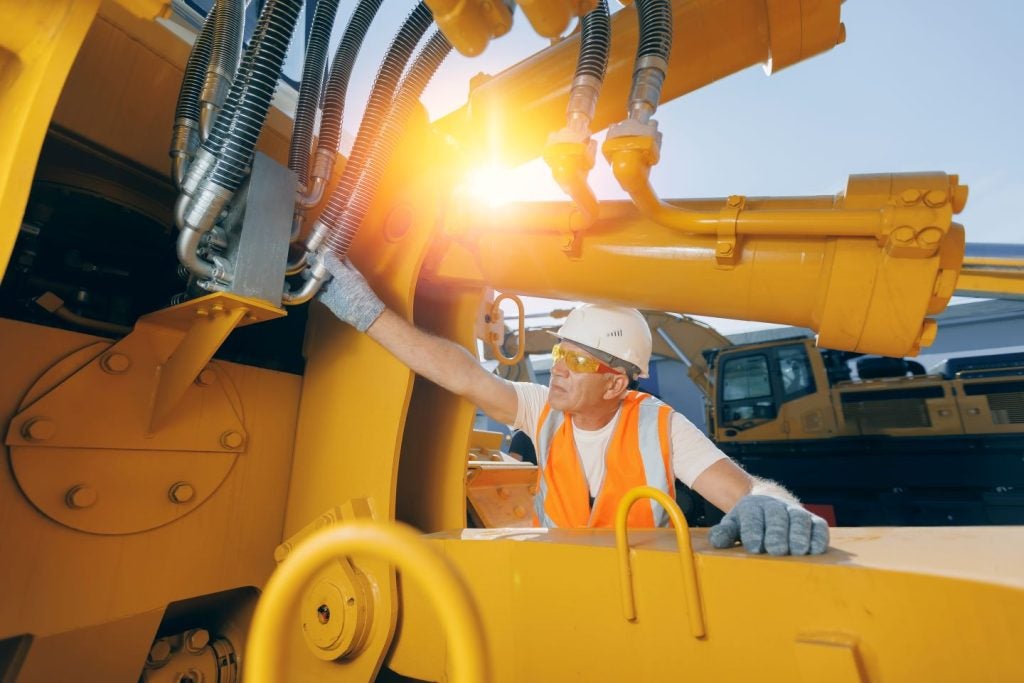
As well as helping prevent breakdowns, the availability of predictive maintenance can further save money and increase efficiency by helping to extend the lifespan of machinery.
“Digital twins enable continuous monitoring of mining machinery and processes, allowing operators to assess performance, detect inconsistencies and prevent potential breakdowns in real time,” Di Martino continues. Gathered data – the key element of any digital twin – can offer users comprehensive, real-time snapshots of operations through live dashboards and visualisations.
Using AI and machine learning models, digital twin technology can analyse data and identify patterns that may indicate the risk of breakdowns or safety issues such as equipment failures, connectivity outages and equipment misuse. In doing so, timely interventions can be made to cut the potential damage caused by downtime.
Barriers to adoption of digital twins in the mining sector
Despite significant benefits, adoption of digital twins comes with several challenges.
There is no one-size-fits-all methodology, meaning mining organisations and their mines must take a customised approach to development of digital twins. That starts, Nokia says, with a clear vision and strong commitment – even perhaps a cultural change. If it is to succeed, collaboration among all parties including operators, engineers, managers, suppliers, regulators and customers is a must.
Di Martino cautions that a robust digital infrastructure is vital for data collection, transmission, storage, analysis and visualisation – essential if digital twins are to usher in meaningful change.
A key ingredient is the availability of data collection application programming interfaces (APIs), which enable seamless data integration, real-time ingestion and interoperability between systems.
Alongside the clear advantages they offer, he says: “Overall, digital twin APIs optimise operations, improve efficiency and facilitate better decision-making by ensuring continuous and effective data flow.”
Taking a holistic approach to adoption of digital twins
Another vital element too, fraught with what Di Martino describes as “many intricacies”, is the fusion of IT and operational technologies (OT). “Everything is connected, everything is critical in a mine, trucks are remotely controlled,” he explains.
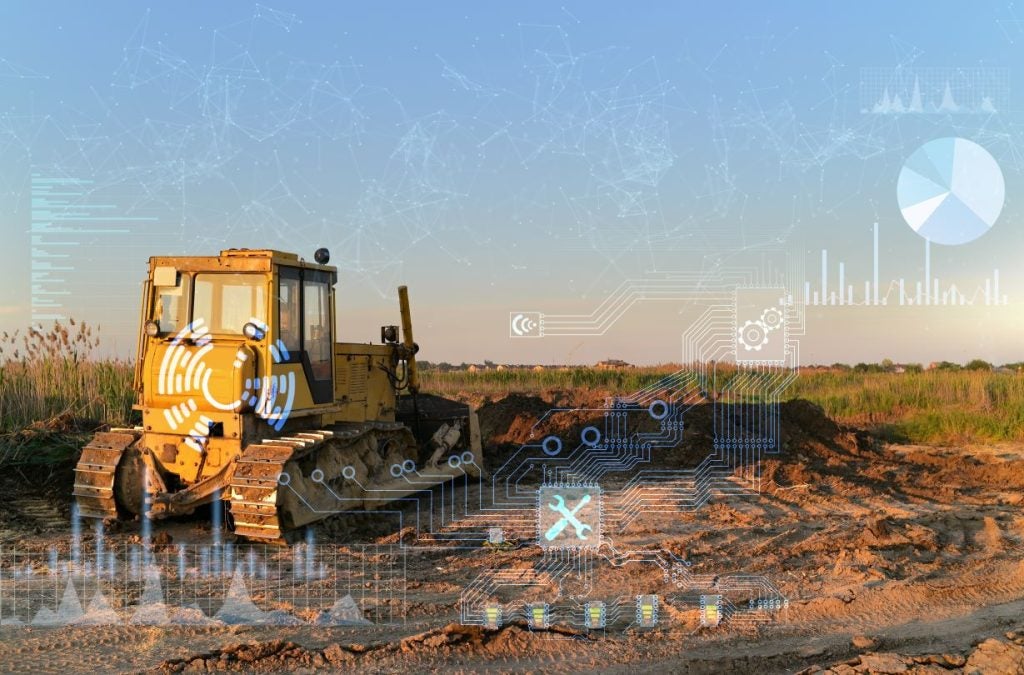
“The network influences the operation, and the operation influences the network. The mine changes every day, blast after blast. The IT network, as a central element in the operation also needs periodic maintenance to adapt to the new working condition. So, IT and OT maintenance can’t be addressed in silos. You need a holistic approach; a joint IT and OT digital twin, and that requires breaking many silos”.
For this reason, organisations wishing to utilise digital twins should clearly communicate across their organisation, describing the intended results and their benefits in the hope of avoiding what Di Martino calls “organisational hurdles”.
“The OT teams that usually look for innovations like these are spread across several areas or domains and fail to align the needs collectively with the IT department,” he warns, adding if there is no clear and holistic view shared across departments it might result in subpar solutions that only meet the initial requirements; perhaps even leading to a bottleneck at the latter stages.
“A lean, agile cross-functional project team, combining deep supply chain knowledge and an excellent development team is essential,” he says.
Poorly designed digital twins could threaten benefits of predictive maintenance
If any digital twin implementation project failed to address these concerns, the outcome could threaten the potential benefits of predictive maintenance, including increased productivity, lowered safety risks and greater agility.
“Predictive analytics solutions leverage data to forecast future outcomes,” says Di Martino. “This technology assists maintenance planners, systems engineers, controllers and other mine personnel in making real-time decisions that enhance performance, reliability and profitability.”
He adds: “Maintenance tasks are scheduled based on these predictions, ensuring timely interventions and avoiding both premature and delayed maintenance. Continuous feedback and data integration enhance the system’s accuracy over time, making predictive maintenance more effective.”
Empowering miners to embrace predictive maintenance tech
Engaging and empowering end users such as operators, engineers and managers is also vital. Employee buy-in is as important as the technology selected but can often be as big a challenge.
“Commodity industries, like mining, are naturally risk averse,” according to Di Martino, “and the efforts can quickly drive up a collective sense of anxiety and dissolve into disconnected projects that ignite a sense of wasted focus.”
That need to train and develop skills has perhaps never been more pressing, with Di Martino simply saying he doesn’t believe the workforce is as able as it could be.
“I’ll be very honest and direct,” he says, “I don’t think we have the skills. Why? There is one single reason: we have the mining experts, and then we have AI experts; we don’t have one person that understands both domains.”
Describing this issue as the elephant in the room, he says this goes right back to training, and indeed, what training provision there is. Organisations must provide user-friendly interfaces, tools, training, support and feedback mechanisms.
Can digital twins help break down silos in the mining industry?
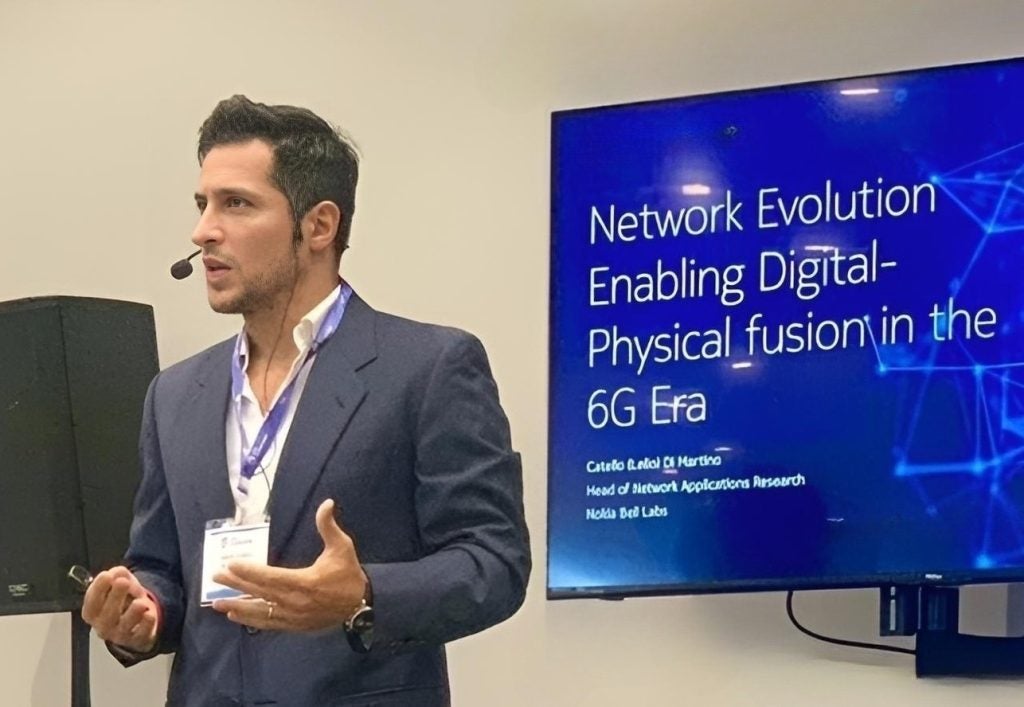
Another concern for Di Martino is the legacy of siloed working approaches in the industry. He warns that although a huge amount of data is produced each day across modern mining operations, it is often stored and analysed in metaphorical silos. “Much of this information is wasted – either unused or poorly implemented for providing insights to mine operators,” he says.
By using digital twins and other technological advances such as the cloud this data has the potential to reduce unplanned downtime, streamline processes, improve asset performance and boost a mine’s environmental, social and governance credentials via predictive analytics. It also has the capability to breakdown siloed practices, ensuring everyone, anywhere in the world is seeing and utilising the same information and visualisation dashboards.
Di Martino says as mining operators face a future of dwindling resources and the challenges presented by deeper mines, rising energy costs and infrastructure shortages, there has never been more pressure to improve efficiency and cut costs. Innovation and research will play a crucial role in finding new ways to increase efficiency.
“Barriers must first be understood. A digital twin is not an application that provides results to users, but it serves as a platform for other applications, to create actionable intelligence and situational awareness,” he says. That can only happen if we break the ultimate silos, bridging research with real-world problems, lived every day in a mine, to be able to find solutions. “This is where the true value of digital twins can be unlocked to lift the future of mining.”