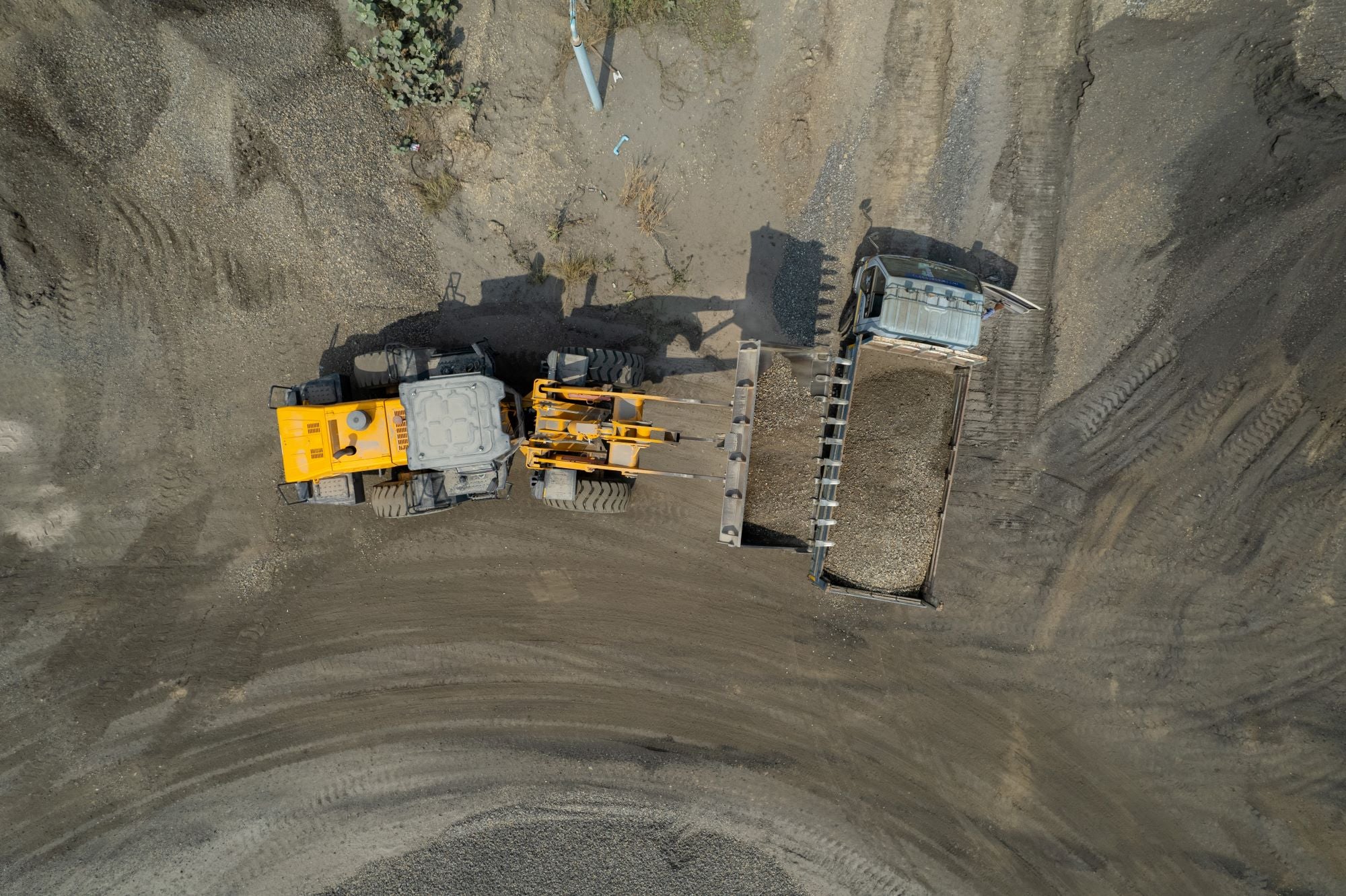
Mining’s reputation as a dirty industry is almost as old as mining itself. Yet in recent years, an interesting paradox has emerged: as demand for the raw materials required to make electric vehicles and other battery-powered technology skyrockets, the world needs a large global mining industry more than ever.
In wrestling with this problem, the global mining community has set itself various targets for reducing its carbon emissions. BHP, for example, has committed to reducing operational greenhouse gas emissions by 30% before 2030, with a net-zero target set for 2050.
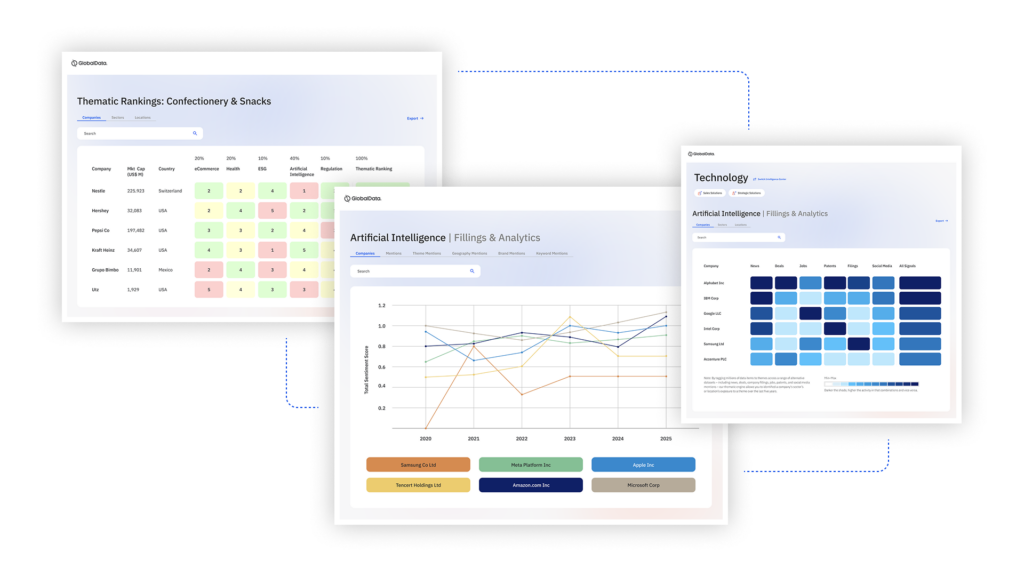
US Tariffs are shifting - will you react or anticipate?
Don’t let policy changes catch you off guard. Stay proactive with real-time data and expert analysis.
By GlobalDataWhile some may argue that these targets are not ambitious enough, it’s important to remember that the process of decarbonisation for an industry so reliant on heavy machinery is no simple task; according to a McKinsey report, only 0.5% of mining equipment is fully electric.
One of the more immediate ways that the industry can decarbonise its operations is by focusing on their transport and haulage operations. With electric vehicles widely available, this could be a fast-track to reducing emissions.
Battery-powered trains in the Pilbara
In 2022, Rio Tinto announced plans to trial four battery-electric powered trains in the Pilbara starting in 2024. The four battery-powered locomotives have been purchased from the Wabtec Corporation, and production is due to start in 2023, ahead of trials in the Pilbara in early 2024.
The trains, which are used to transport ore from the company’s mines to its ports, will be recharged at stations at each end of the route. Additionally, the locomotives will be able to partially recharge their own batteries thanks to a braking system that takes energy from the train and uses it to recharge the onboard batteries.
Rio Tinto managing director of port, rail and core services, Richard Cohen is optimistic that the trains will help them meet emissions targets.
“Battery-electric locomotives offer significant potential for emissions reduction in the near term as we seek to reduce our scope one and two carbon emissions in the Pilbara by 50% by 2030.”
Biofuel potential
Several companies are taking a different approach. Rather than replacing their fleet with electric vehicles, BP, Rio Tinto and BHP have looked to use biofuels in their existing fleet. In May 2022, Rio Tinto announced a partnership with BP, in which they will trial sustainable biofuels to power its marine fleet for 12 months.
Using a combination of fatty acid methyl esters – a fuel derived from recycled cooking oils – and very low sulphur fuel oil , Rio Tinto hopes to reduce its emissions by 26%, in comparison to standard marine fuel oil.
BP is also collaborating with BHP in a biofuels trial, in which hydrotreated vegetable oil (HVO) fuel is being used to power haulage trucks, as well as other mining equipment over an initial three-month period at its Yandi iron ore operations in Western Australia.
HVO is made through one of two processes: hydrocracking, in which large molecules are turned into smaller ones, or hydrogenation, where hydrogen is added into existing molecules in vegetable oils. HVO can be made from a number of different substances, including canola, algae and tallow; according to BHP, their HVO will be produced from more sustainable sources, such as waste products.
According to BHP, approximately 40% of its operational greenhouse gas emissions came from diesel-powered equipment in 2020. With HVO fuel offering an up to 90% reduction in carbon dixode emissions compared to regular diesel, this could mean a major step closer to a low-carbon mining industry.
“Ultimately, our aim is to have fully electric trucking fleets at our sites, but alternative fuels like HVO may help us reduce our emissions in the meantime while the electrification transition takes place,” said BHP Western Australia Iron Ore (WAIO) Asset President, Brandon Craig, who sees the trial as a key part of the net-zero transition.
“This collaboration with the teams at Yandi and BP is really exciting to see, given the potential application in our WAIO business and BHP’s operations globally.”
A major advantage of biofuels is that, in most cases, no modification of existing equipment is required, making implementation a relatively simple process. Both Rio Tinto and BHP’s trials will compare the performance of the biofuels against standard fuel, and if successful, could be widely implemented across the fleets.
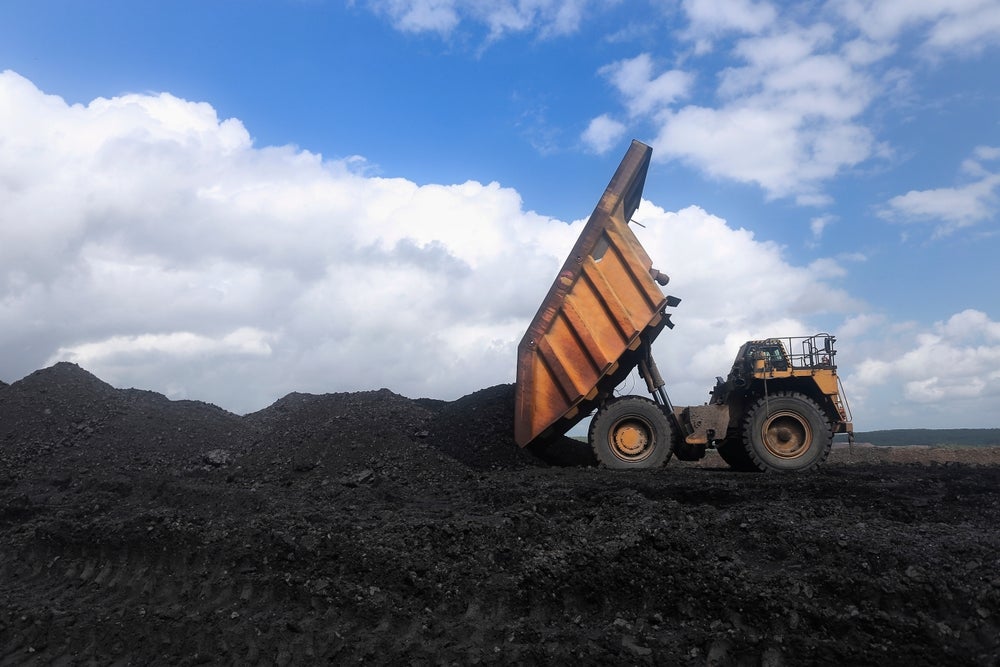
Monitoring fuel efficiency
Yet the question remains as to how to make sure that these greener fuels are being used in the most efficient way possible. One of Indonesia’s largest mining contractors has turned to the world of motorsport for answers.
PT Pamapersada Nusantara (PAMA) recently partnered with McLaren Applied to introduce new technology to monitor the efficiency and fuel consumption of PAMA’s mining vehicles.
Using multiple sensors onboard each of PAMA’s mining trucks, McLaren Applied’s Formula 1-derived technology can collect highly detailed data in real time, before transmitting it to cloud-based servers and feeding it into a machine learning algorithm. Specially-developed AI tools then cross-reference this data against a digital model of the mine, calculating the necessary changes the driver needs to make to optimise fuel efficiency and relaying it back to the driver within milliseconds.
The benefits of the system are more than just environmental. With up to half of a mine’s operating expenses being spent on fuel, even small gains in fuel efficiency can bring massive savings, and the effective use of a variety of innovative processes – from data analysis to digital twins – is a positive development for the future.
As a result, there is no one-size-fits-all solution for mining operations trying to decarbonise their fleet. Even the seemingly obvious answer of electrifying transport vehicles is far more complex than it seems, not to mention the logistical and financial pressures involved in switching to an all-electric fleet. The climate crisis requires immediate action to be taken, and taking a proactive approach to decarbonisation means considering what can, as well as what should, be done. Undoubtedly, the industry needs to do better, but progress on the road to net-zero is to be celebrated, even if the solutions aren’t yet perfect.