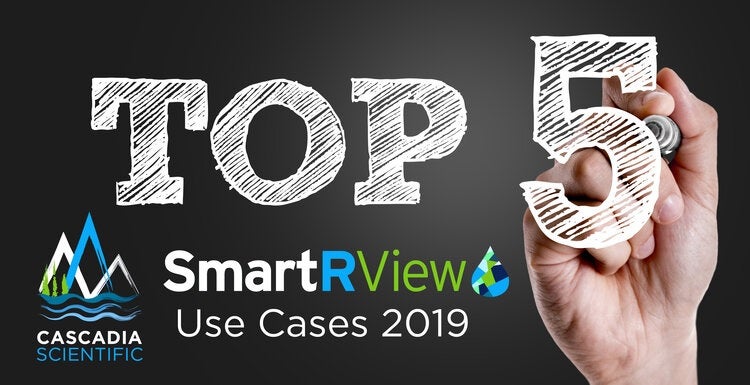
In keeping with the time-honoured New Year’s tradition of identifying and celebrating the best and brightest of the past year, Cascadia Scientific has selected its Top-5 customer use cases for 2019.
Each of these use cases was actively engaged by SmartRView subscribers to bring about improvements in profitability over the past 12 months. 2020 is shaping up to be even more exciting!
USE CASE 5: Operator Efficiency Ranking
Throughout 2019, Cascadia Scientific pushed ahead with new machine learning techniques and model-building strategies. Models are trained with haul cycle aligned observations and each observation is thoroughly characterized (tonnage, time, distance, vertical travel, fuel consumption, shift ID, equipment ID, operator ID etc.).
This approach allows the statistical models to isolate for the impact of each of these factors including operator behaviour while accounting for influences outside of the operator’s control.
On one mechanical drive fleet, the efficiency span between the most and least efficient operators exceeded 7% and the mean operator improvement potential was 2.7%.
Monthly scoring and ranking reports enable leadership to track operator performance, provide targeted retraining and to recognize top performers.
USE CASE 4: Synthetic Lubricant Efficiency Impact Analysis
Having considerable experience designing and overseeing studies related to premium or additized diesel fuels, Cascadia Scientific ran its first initiative to quantify the efficiency impacts of full synthetic lubricants in mining haul trucks.
The trial ran in two phases, a baseline phase and a reconfigured phase during which the population was evenly split between trucks running full synthetic lubricants and those running on mineral products.
While exact results cannot be shared in this forum, we can say that the data demonstrated a statistically significant efficiency benefit attributable to synthetic lubricants.
USE CASE 3: Model-driven fuel use and production forecasting
Using many of the same techniques discussed in use case 5, Cascadia Scientific is leveraging predictive modelling with mine planners to accurately forecast production levels and fuel demand. In one instance, the process was applied to analyse the impact of planned mine evolution on an active and deepening pit.
Cascadia data scientists used the SmartRView platform to build and train a linear regression model to predict cycle time and fuel use as functions of distance, vertical travel and tonnage. Next, the model was run with inputs based on planned bench height and ramp angle.
Using this approach, the team was able to forecast how mine evolution would impact production levels and operating costs. This data was then used to evaluate how additional equipment could be deployed to maintain the present mill feed rate.
USE CASE 2: Mine Road Energy Intensity Heat Mapping
When a customer asked us to render their haul roads overlaid with colours depicting energy intensity, we were thrilled to get started.
SmartRView’s hardware platform provided direct access to all the required data elements (high accuracy fuel consumption, geo-location, speed and road grade) but the use case did require an augmented data collection strategy. With the information pipeline in place, our data scientists rendered fuel intensity with a red-blue spectrum to visually highlight areas of highest energy intensity. Within a few weeks several hot spots emerged and were determined to be caused by unintentionally steep ramp angles. The tools have since been used to confirm the resolution of these hot spots through targeted road repair.
USE CASE 1: Preventive Maintenance Scheduling Strategy
Scheduling preventive maintenance as a function of engine hours is a well established and widely used practice in mobile mining circles. An hour of operation is used to approximate work performed and thereby as a means for estimating a developing need for maintenance. In the absence of a better metric, this approach combined with and a healthy degree of conservatism can keep equipment running, but typically leads to over maintenance, unnecessary expense and decreased availability.
A retrospective analysis was performed for a Cascadia Scientific customer to see how well hours aligned to total engine output (fuel consumed). The results showed that within historical preventive maintenance intervals the total fuel consumption varied by 56%. This highlighted an obvious opportunity for improvement which was exploited with a hybrid PM scheduling strategy based on both engine hours and fuel consumption.
Having hard caps on both fuel and engine hours with an increased engine hour limit is expected to result in one fewer preventative maintenance event per truck per year.