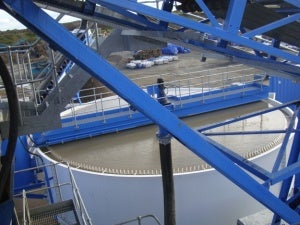
When searching for a turnkey washing solution, Skene Group again chose CDE to ensure their simple yet effective quarrying ethos to "Produce good quality products in a safe and economic manner" was upheld.
Skene Group was founded in June 1968. Originally involved in plant contracting, the company has diversified into being one of the UK’s leading independent operators in the construction supply sector. For many years sand and gravel has been a major source of Scottish aggregates and in Skene Group’s early years natural sands and gravel provided the largest proportion of commercially produced aggregates in Scotland. Today, the market for sand and gravel in central Scotland is thriving due to major infrastructural projects including the construction of the £1bn Forth road bridge, the new £500m Edinburgh Tramline connecting the City Centre to Edinburgh Airport and the overall increase in infrastructural investment.
The site of the CDE Washing Plant is Lomond Quarry, a hard rock quarry with a sand and gravel overburden, near Glenrothes, Fife in Scotland. The hard rock is a mixture of Whinstone and Dolerite and is notoriously hard to process. Skene Group operates sand and gravel resources supplying the construction and sports industries throughout Scotland and beyond. These include house building, as well as tar and concrete production including drainage and decorative stone for paths and driveways. These high quality aggregates are transported by road and sea and continue to be a valuable resource to the wider industry.
In 2011, Skene recognised that their existing washing plant on-site in Glenrothes required an upgrade. This led the company to speak to CDE about a new turnkey processing solution. Ideally, this solution would be a completely integrated package that would process material from crushing right through to producing clean washed products ready for sale and also for internal use. It was always important to Donald Skene, chairman of Skene Group, to ensure that the new solution would give Skene the ability to ‘blend’ natural sand, gravel and blasted rock in proportions to sustain the quarry. "Central to our requirements for the washing plant was the blending of materials to ensure that our natural sand and gravel and hard rock could be mixed in usable proportions to manufacture concrete specification sand, therefore allowing us to sustain the quarry. Sustaining the quarry means we can retain and support our employees for the foreseeable future."
Skene Group had previously purchased two CDE plants and so invited CDE to look at the existing site at Lomond Quarry with a view to replacing the existing plant. After initial meetings with Donald Skene and Neil Skene, managing director of Skene Group, Eunan Kelly, area sales manager for Scotland, believed that CDE could meet Skene Group’s specific requirements while keeping the cost of ownership low. "From the outset of this project we were confident that we could guarantee Skene’s requirements; the ability to successfully blend material in sustainable proportions, the capacity to increase productivity to satisfy internal demand and the capability to deliver high quality concrete and building sand for construction use whilst ensuring minimal environmental impact."
The CDE plant was installed and commissioned in Summer 2012. CDE produced an integrated solution combining both jaw and cone crushers with the washing plant. The process begins with a blend of the naturally occurring sand and gravel overburden being fed to the plant via the L55 feed hopper. The feed hopper includes a tipping grid with 250mm spacings and an integrated belt feeder to ensure the efficient transition of material to the next stage of material processing. The feed conveyor delivers the material to a grizzly screen with the +60mm material going forward to a jaw crusher.
The jaw crusher underflow re-joins the -60mm grizzly screen underflow and is conveyed to two ProGrade P2-75 rinsing screens. The ProGrade is an inclined circular motion screen designed to cope with the harshest conditions. The ProGrade screening phase consists of two rinsing screens complete with PU screening media. The +25mm oversize from the ProGrade is fed to a cone crusher via a S20 surge hopper and conveyor. This material is in a closed loop until -25mm. The +5mm-25mm material is stocked via a radial 26m conveyor as per their required specification concrete aggregate.
The P2-75 underflow (-5mm) is then fed to the EvoWash 152. The modular design of the EvoWash ensures highly accurate separation of silts and clays from material, guaranteeing production of specification sands. The primary product from the EvoWash 152 is the 0-5mm concrete specification sand. There is a facility to increase or decrease the bottom end 0-2mm in the concrete sand meaning that the concrete sand specification can be maintained easily on site. Any excess 0-2mm is stockpiled for other uses within the quarry operation.
The cyclone overflow including the waste water, silt and clay, is delivered to the CDE AquaCycle A600 high rate thickener. Here the silts combine together and drop to the bottom of the tank forming a sludge which is then discharged. This results in clean, reusable water that overflows into the CDE AquaStore, which is located close to the AquaCycle and stores water for recirculation around the plant. The sludge is pumped away to holding lagoons on a disused part of the quarry. Significant steps have been taken to ensure that consideration of environmental impact is at the forefront of Skene Group’s operations and the CDE AquaCycle illustrates this perfectly. The AquaCycle reduces the volume of fresh water required to feed the washing plant by up to 90%, meaning the potential environmental impact is kept at a minimum.
Donald Skene commented on the superior design of the CDE plant, "In certain areas of the quarry the material is dirty, but the combination of the CDE sand plant and the AquaCycle thickener is so effective that it is hard to believe how dirty the raw feed is. The nature of the material being processed has changed since the previous plant was installed and this could have meant more water was required to run the new plant, but the AquaCycle solves this problem and ensures water is constantly recycled around the plant."
Speaking about the final delivery of the Skene Project, Donald Skene believes the plant is excellent value for money, "I am confident that the cost per tonne of this plant is dramatically lower than for a crushing and screening solution. This turnkey system provides us with a long term processing solution that will allow us to meet our production requirements for more than a decade."
For further information on CDE and the products detailed in this case study, please visit CDE’s website.