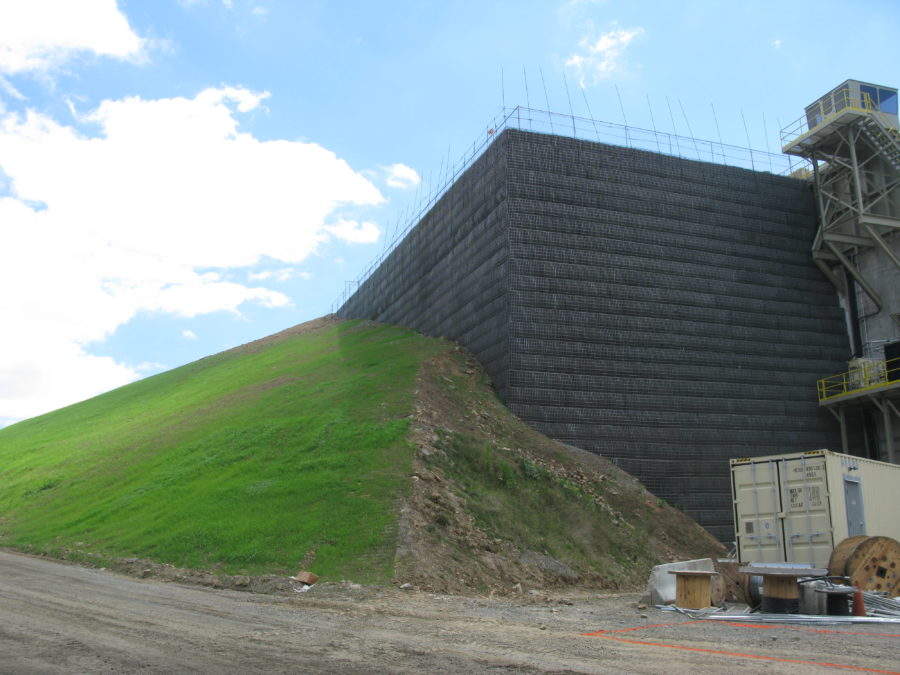
Dyer Quarry is located in Robeson Township, Berks County, Pennsylvania. The facility is strategically located and serviced by Norfolk Southern Rail lines. Dyer produces a wide variety of aggregate sizes meeting PA, NJ, DE and MD DOT’s and AASHTO requirements. Such aggregates are also used extensively in railway applications due to their hardness.
A primary crusher unit was being added to the quarry. The terrain at the proposed crusher location was challenging and a substantial height retaining wall was necessary to create a safe platform for the mine trucks unloading into the crusher.
The maximum exposed height of the reinforced soil wall was 21m-high with a fascia area of approximately 1,900m². The reinforced soil wall was built around the crusher to minimize the lateral earth pressure upon it. The wall was designed to support the live load of the CAT D773 haul trucks used in this facility, which have a payload of 100t. The geogrid reinforced soil structure provided the stabilized access platform for the haul trucks.
The project engineer, Titan Engineering PC determined that a mechanically stabilized earth wall using Maccaferri’s ParaGrid® geogrids would offer the optimum solution, due to its cost-effectiveness and ease of installation. The project also featured a welded wire mesh fascia element, which assisted with the installation process.
Working with Titan Engineering PC, Maccaferri provided engineering design services and materials for the walls and Golder Associates built them.
Products selected for use in this solution included:
- Fascia element: Welded wire panels
- Fascia stone retention: HDPE net
- Soil Reinforcement: ParaGrid 65, 100, 120, 150 & 200
- Drainage Geocomposite: MacDrain® W1051
- Separation / Filter Geotextile: MacTex® N35.1
Due to the complex topography, the wall showed several peculiarities and required special attention during the construction. Any field design changes to the original submittal were documented and duly reported to the project team.
ParaGrid® consists of aligned arrays of high tenacity polyester yarns encased in a thick protective sheath of Low-Density Polyethylene (LDPE). The LDPE coating is more robust and durable against biological and chemical degradation, which leads to excellent performance in terms of long-term tensile strength and durability.
The benefit of geogrid reinforced soil structures within mines is often the availability of structural backfill material as a byproduct of the mining or quarrying process. This reduces the number of imported materials compared to traditional reinforced concrete or sheet pile retaining structures.
The ParaGrid® geogrid is unrolled and positioned before the structural backfill is placed upon the geogrid and compacted. This process is repeated until the full height of the structure is reached. ParaGrid® geogrids with tensile strengths from 65kN/m to 200kN/m were used within the structure; each strength selected to optimise the design and therefore reducing the installed cost of the structure.
MacDrain® drainage geocomposite was placed between the structural backfill and the existing soil slope. This provided a drainage column to intercept, capture and remove groundwater, preventing it from entering the reinforced soil mass, potentially weakening it.
The project was constructed very rapidly due to the ease of installation of the system. Despite heavy rainfall throughout the construction phase, there were no recorded weather delays due to the selection of free-draining structural backfill material (AASHTO #57 stone).