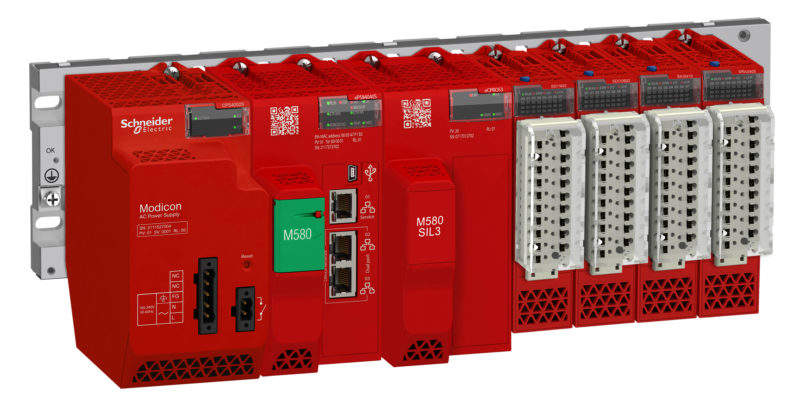
- Provides up to 100% measurable ROI within three months
- Better access to operating data improves uptime, yield and energy costs compared to legacy safety systems
- Improves the real-time security, safety, efficiency, reliability and profitability of industrial operations
Schneider Electric, the leader in digital transformation of energy management and automation, has introduced the Modicon M580 Safety Controller, an Industrial Internet of Things-enabled safety and process controller that drives new levels of safety and operational profitability.
The Modicon M580 Safety Controller combines the performance, cybersecurity and networking capabilities of Schneider Electric’s award-winning Modicon M580 Ethernet-enabled programmable automation controller with the functionality of a safety programmable logic controller. When applied correctly, it is the only combined control and safety PAC on the market that offers measurable 100% return on investment within three months of application.
Changing the industrial landscape with EcoStruxure™
“The hybrid industries have traditionally kept their control and safety systems separate from one another. That approach minimizes risk, but it can make for costly systems that are cumbersome, inflexible and difficult to maintain. However, Schneider Electric’s M580 Safety Controller allows companies to align technology architectures with risk tolerances via an IIoT-enabled control and safety system that saves time, money and effort,” said Matt Littlefield, president and principal analyst, LNS Research.
“Additionally, as the speed of business continues to accelerate, especially as industry variables such as energy and raw material costs fluctuate more frequently, operators need better approaches to ensure the safety of their assets while better controlling the performance and profitability of their operations. By integrating key capabilities of its Modicon M580 ePAC into the M580 Safety Controller, Schneider Electric is changing the way industry can approach operational safety, moving it from a cost center to a profit center, while also protecting the plant’s most important assets: its people, production, and profits.”
Part of the company’s EcoStruxure™ Plant IIoT platform, the controller uses the same software tools, wiring methods and the X80 I/O structure as the M580 ePAC to reduce spare part inventory and maintenance costs. The controller also provides the workforce with better access and visibility to operating data and diagnostics via a unique and secure Ethernet communications backbone. Additionally, mobile device compatibility makes safety and operating data available anytime, anywhere, including system performance that is monitored centrally to spur continuous improvement. When combined with change-on-the-fly configuration, event logging capabilities and one of the largest programming memories in the industry, the M580 ePAC empowers the workforce to drive their operations to world-class performance.
EcoStruxure is Schneider Electric’s interoperable, IoT-enabled system architecture and platform that delivers enhanced safety, reliability, efficiency, connectivity and sustainability.
“Our EcoStruxure development principles build safety functionality for industry into the very core of our process automation and control offers,” adds Jose Bonomo, Vice President, Edge Control Offers for Schneider. “In this case, the result is an advanced, IIoT-enabled controller that does not compromise safety performance for the sake of process control, nor process control performance for the sake of safety. It means we can provide better flexibility and communications in a safety controller that has dual TÜV certification for process and machine safety, is compliant with most fire and gas standards and is certified at Achilles Level 2 for better cybersecurity protection.”
Increasing operational profitability, safely
As manufacturers seek to measure and control their real-time business risks, particularly the risks to the safety, security, efficiency, reliability and profitability of their operations, they must have real-time access to and information about key operating variables, as well as other data required to make better real-time business decisions.
For example, the M580 Safety Controller provides total transparency and real-time data flow across the control architecture which allows users to better balance energy consumption and asset performance. The synergies provided are proven to reduce energy costs by as much as 30 percent, while ensuring full, measurable ROI sooner. According to the Water Research Foundation, a water treatment facility supplying approximately 220 million gallons of water per day could consume 1,500kWh per one million gallons. At $0.05/kWh, the typical operating expense would be approximately $6m annually. If that water facility were operating on the M580 Safety Controller platform, the potential savings would be $1.8m per year or more.
“We have multiple examples and studies to show that with its new functionality, including better access to real-time data, more diagnostics and better HMI functionality, the Modicon M580 Safety Controller can enable hybrid industry users to increase system uptime and yield by more than 30 percent compared to legacy safety systems, while driving additional savings in energy and operating costs,” Bonomo concluded.
“No other programmable controller on the market today provides such quick return on investment and ongoing, measurable operational profitability improvements.”