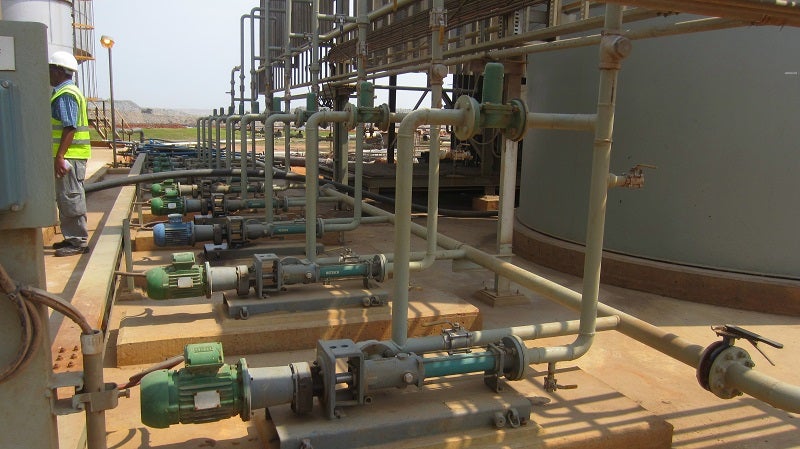
Until January 2017, a copper beneficiation plant in Zambia was using pumps from six different manufacturers, including units from NETZSCH Pumpen & Systeme. This resulted in a steadily growing inventory of similar spare parts and maintenance procedures.
Thereby, the effort and costs for maintenance of the pumps were constantly increasing. Following a thorough review of the reliability and service life of the pumps, the plant operator decided to only use pumps from a single supplier. NETZSCH, represented by its subsidiary in South Africa, was chosen for the reliability of its pumps. By the consequential reduction of its spare parts inventory, the Zambian company saved $1m.
"A lot of separate processes are running in beneficiation plants, each needing its own special equipment. The heart of each process is typically a pump, to convey mineral sludge or chemicals needed for the process," explains Roger Willis, chemical, pulp and paper business field manager from NETZSCH.
"It is also typical that the plant systems are fitted with lots of similar pumps from different manufacturers."
As a result the number of similar components increases, which overall means complex maintenance processes that require a lot of time and money. This was the case for a copper beneficiation plant in Zambia.
"NETZSCH found out incidentally from a third-party about the existence and location of some of its own pumps," adds Roger Willis.
The plants service personnel did not know about the pumps, because they had been operating very reliably and had not yet made it onto the maintenance plan. The plant maintenance department then checked the maintenance costs of all their existing pumps. This involved analysing the average disruption-free time, as well as the spare parts inventory for all pumps from the various manufacturers. It turned out that standardising to one manufacturer would produce significant savings. The plant operator chose to switch to NETZSCH because of the reliability and stability of the pumps already installed.
In total, the Bavarian manufacturer supplied 36 pumps for polymer applications. The changes allowed the plant operator to reduce its spare parts inventory substantially and save $1m.