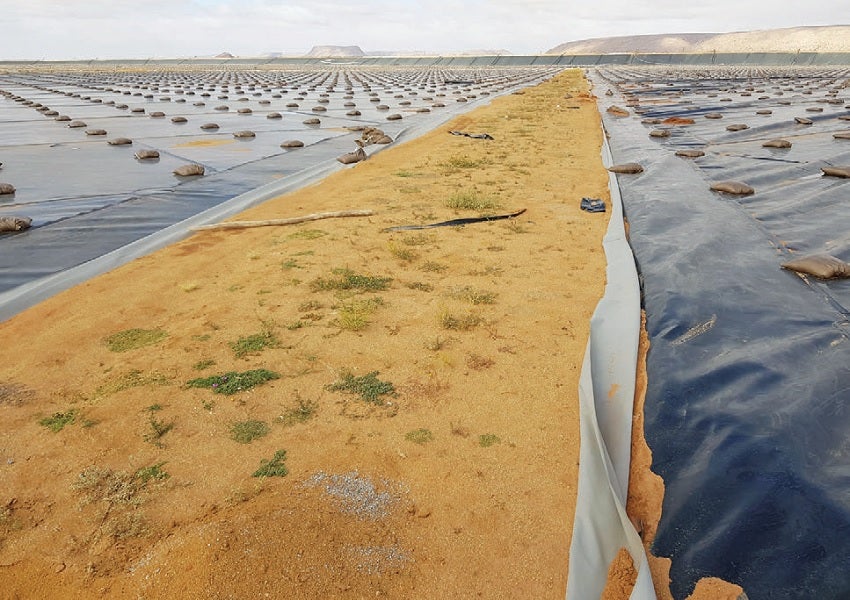
Tailings management in particular, an area neglected in the past, is now a priority. While lining have become the preferred option to reduce possible environmental impact of tailings material they pose their own set of risks which urgently need to be monitored and addressed, says Knight Piésold technical director for mining Andrew Copeland.
Up until a few years ago, the mining industry in South Africa took a reactive approach to environmental impacts caused by mining activities. Unfortunately, tailings-related impacts are severe – and can result in loss of life, long-term damage to the environment and ground water pollution.
“The combination of legislation covered by the National Environmental Management: Waste Act, 2008, and Government Notice 332, May 2014 in which residue deposits were deemed as a waste unless de-classified or exempted by the minister, has seen the mining industry’s determination to make amends by complying. Together with government, consultants such as ourselves are working closely with the sector to improve our environmental image,” Copeland starts.
The mines have subsequently turned primarily to linings as a means to ensure seepage from tailings deposits does not come into contact with the natural environment. The government has also shown favour for this route as it considers it a proactive and trusted mechanism which guarantees protection of the environment.
“It is commendable that our industry is embracing the need to reduce its impact on the environment and we are undoubtedly heading in the right direction but few are aware that the solution we are now deploying has its own potential risks,” Copeland reveals.
The incorporation of linings for example is not a finite solution. Like most plastic-based products, they degrade over time (20–100 years possibly, depending on the quality of the lining and the material it houses) and will leak. This means they cannot be considered a long-term option on their own, and may only function well during the operational life of the tailings facility.
But there is a far greater risk at play, Copeland highlights. “The incorporation of a lining, be it traditional synthetic material or a more natural substance such as clay which can be costly to use if it does not occur naturally on site, influences the design of the facility and more importantly, the stability of the structure. A layer between the ground and a large mass of loose/unconsolidated material weakens the facility, in most cases.”
Most tailings facilities are hydraulically deposited, and the excess water must be removed for the tailings to gain strength and impound itself (or be impounded by earthwork dams). By introducing an impervious layer, water that previously seeped into the ground or was intercepted by perimeter drains, must now be removed through a comprehensive under-drainage network. If this drainage system is inadequate or damaged during operations, unstable tailings structures will result and eventually collapse – and this will be catastrophic.
Copeland estimates that a lined facility with an inadequate drainage system might be operational for about ten years after which its potential to fail escalates substantially. In addition to the environmental implications of this (and the costs associated with the clean-up), there is the cost of having to prematurely build new facilities, an equally disastrous reality for the industry. “Considering that South Africa’s lined tailings facilities are <5 years in age, we are in a period of beginning to understand whether such designs are sustainable and if/when we reach the crossroad of having to build new tailings facilities to replace unsafe ones.”
What then is the solution?
The first step in addressing this challenge is acknowledging it and evaluating the threats – including costs.
Government has fortunately already made some inroads into changing legislation that will assist with this by deregulating mining waste from the waste act to allow companies to consider a risk-based approach – thereby eliminating the need for a lining in some cases. “Companies still need to establish if their tailings material is hazardous to the environment and in addition to motivating that their site is well positioned, can recommend a remediation approach supported by detailed scientific investigations.”
Such an approach would require a different tailings management solution. This might include interception/abstraction boreholes to remove tailings contaminated water as it leaves the site.
A grout curtain/interception point which seals off flow of contaminated water to an area which can be controlled is another option. Fracturing the rock underground to create a natural pathway for contaminated water to flow is a third option although this is only a concept at present.
“Ultimately, this system also has weaknesses as it relies on trusting the industry to correctly operate such a remedial system, but if properly managed can largely eliminate environmental impacts in the short-term and more importantly, in the long-term – post closure.”
The government and the Minerals Council South Africa have both approved a risk-based approach where applicable and Knight Piésold is already working with clients in South Africa to consider this methodology. “This is something we also need to share across Africa, as well where some international mining houses are by default lining their tailings facilities.”
“In reality, it pays to overdesign your tailings facility’s under-drainage and/or seepage interception system, to minimise the risks to the environment, regardless of the method and design used. This may be a costlier exercise upfront but can undoubtedly save not only the environment but also unnecessary/unplanned costs down the line,” Copeland concludes.