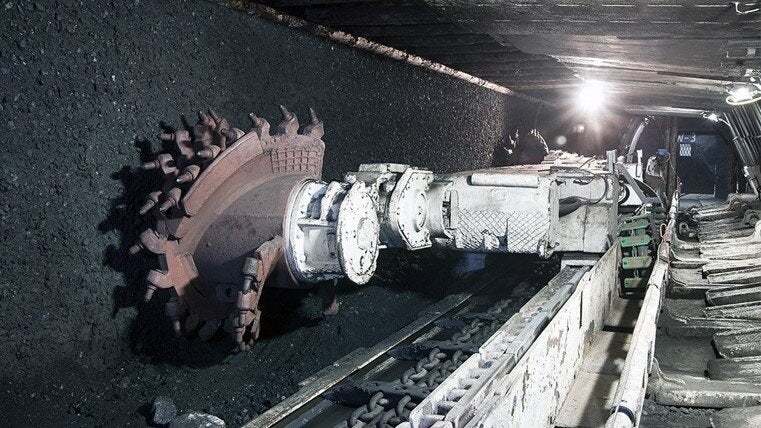
Key takeaways
- As Australia’s shallow mining reserves become depleted, mines are progressively becoming deeper. This creates some unique geotechnical design challenges with pillar design, due to increased vertical and horizontal stresses.
- It is becoming increasingly apparent that traditional empirical pillar design approaches alone might not be adequate at depths outside the current Australian underground coal database.
- Cartledge Geotechnics and Mining (CM&G) believes a more appropriate design approach is to use a combination of empirical, numerical, analytical, and operational benchmarking to both maximise production and maintain site safety.
By Bongani Dlamini, Associate Geotechnical Engineer at Cartledge Mining and Geotechnics
As Australia’s shallow mining reserves become depleted, mines are progressively becoming deeper.
This creates some unique geotechnical design challenges with pillar design, due to increased vertical and horizontal stresses.
Pillars ensure the stability of underground workings and understanding the stresses they can handle is central to the balance between maximizing extraction and maintaining site safety.
Design challenges are becoming increasingly significant in Australian underground coal mines, where some mines are operating at the 500m depth threshold and progressively getting deeper.
At these depths there is little or no Australian underground coal precedence and pillar design will be critical to safety and production.
Pillar performance and design approaches are well documented at shallower depths. However, at depths of more than 500m there are some knowledge gaps in terms of pillar performance and design approaches.
So, it is becoming increasingly apparent that traditional empirical pillar design approaches alone might not be adequate at depths outside the current Australian underground coal database.
At Cartledge Geotechnics and Mining (CM&G), we believe a more appropriate design approach is to use a combination of empirical, numerical, analytical, and operational benchmarking.
Experience tells us what has worked in the past but as we enter relatively unknown territory above 500m, we need to use this combination of methods, in conjunction with the professional experience of our team members.
CM&G recently demonstrated how this combined design approach can work when completing a study for a client.
We were engaged by a major mining company to conduct a comprehensive pillar design for a proposed underground coal mine. The scope included completing designs for barrier, chain and main pillars at depths ranging between 450m and 800m.
Cartledge team members were able to use their collective experience in underground mining to analyse the information from the various methods and make decisions that provided best outcomes for the client.
In this particular case, we used the combined design approach to optimise the pillar size requirements by reducing pillar widths where possible and increasing pillar width where necessary.
That significantly maximised the coal reserves that could be extracted from each longwall panel while maintaining the stability of underground workings, and therefore the safety of the mineworkers.
We believe that relying on just one design method will never be enough once mines go past the 500m mark.
But it’s one thing to build models and crunch numbers. Knowing how to analyse and interpret the results to boost mine production and safety is the key to the future of the underground mining industry.