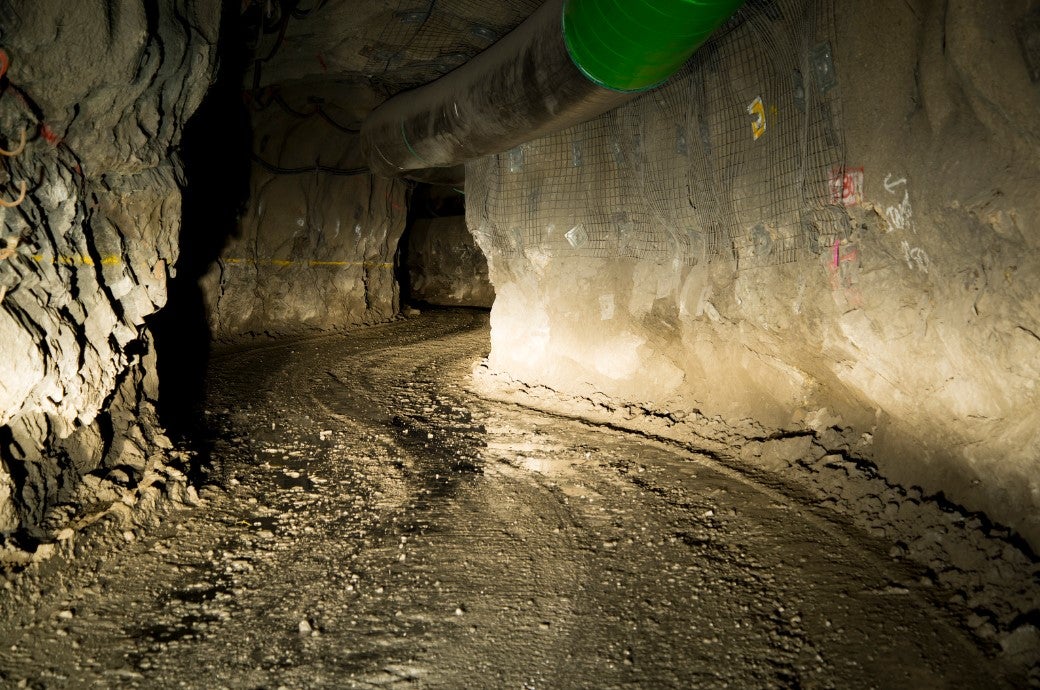
To successfully generate profit from underground mining, it’s essential to maximize the extraction of desired minerals while controlling costs. This requires constant judgment calls and balancing expenditures with ore volume, ore grade, while cost-reducing equipment and processes. Among the significant costs in underground mining, ventilation stands out due to its necessity for safe and efficient operations.
Importance of Ventilation in Mining
Underground mine ventilation is a critical operational cost. Large primary fans draw surface air through the mine, while smaller secondary fans blow air to the working faces. The mine layout evolves as decline and drives are developed, necessitating sophisticated ventilation systems designed by experts. These systems are often modelled using specialized ventilation modelling tools.
Traditional Ventilation Challenges and Costs
Historically, the capital expenditure (CAPEX) on ventilation system components was a major part of total ventilation costs, leading to standardised inventory with limited fan size options. This often results in oversized fans running inefficiently, especially during shorter development stages of a drive. Previously, the primary concern was ensuring adequate airflow with reliable fan operation, without much emphasis on efficiency.
Modern Focus on Energy Costs
Today, energy costs for ventilation have become a significant portion of a mine’s total expenses, and can have a significant impact on key financial metrics such as the All-In-Sustaining-Cost (AISC) used to compare gold miners. Reducing AISC by 10% can significantly enhance a company’s profitability and influence ratings and stock price. Optimising ventilation for energy savings is a key aspect to optimising profitability.
Ventilation-On-Demand (VOD) Systems
Ventilation-On-Demand (VOD) systems provide a practical approach to energy savings by tailoring ventilation needs based on real-time demand, recognising that:
- Most mine drives are vacant a large portion of the working week.
- In a drive with a dual stage fan, both stages may be required during bogging, shotcreting and blast clearance; however at other times a single stage provides sufficient air for other activities.
Traditional whole-of-mine VOD systems designed by consultants involve substantial CAPEX. However, incremental approaches targeting ‘low-hanging fruit’ can yield significant savings with minimal investment.
Example of Energy Savings
Consider a gold mine aiming to reduce its AISC: Implementing VOD in key working areas can save up to 50% in ventilation energy costs. A mid-sized gold mine, deploying VOD in the 10 most active areas can reduce AISC by 10%, significantly enhancing profitability.
Key Components of VOD Systems
1. Method of Controlling Air Delivery; such as:
- Variable Speed Drive (VSD)
- Variable Output Fan
- Dual-Stage Fan
- Dual-Speed Fan
- Dampers
2. Demand Control Signal: the most significant influence on energy savings.
3. Monitoring and Reporting: Continuous performance tracking ensures that the system operates efficiently.
Implementation of VOD
There are three main methods used to implement VOD:
- Manual Control; most commonly manual control by an operator on the surface, controlling underground fans using a SCADA system.
- Schedule Based Control; where the shift work schedule is entered into scheduling software, which controls fans using a SCADA system.
- Automatic Control; in which air delivery is controlled based on vehicles in a ventilation zone, the mix of activities being performed, and optionally including other factors such as air quality.
VOD as a service
A recent addition to the VOD arena is VOD-As-a-Service. This can be implemented in a single working area or across several working areas in a mine. The system can additionally control Primary ventilation fans for further savings, speed up blast gas exhaust, and allow accelerated return to mining operations after a blast.
Conclusion: Strategic Implementation for Cost Savings
Starting with ‘low-hanging fruit’ in VOD implementation, such as controlling dual-stage fans in key areas, can yield substantial energy savings without significant upfront costs.
When deployed as a service, VOD offers an adaptable, scalable solution. It enables mines to achieve immediate and impactful cost reductions, ultimately improving their sustainability and profitability.