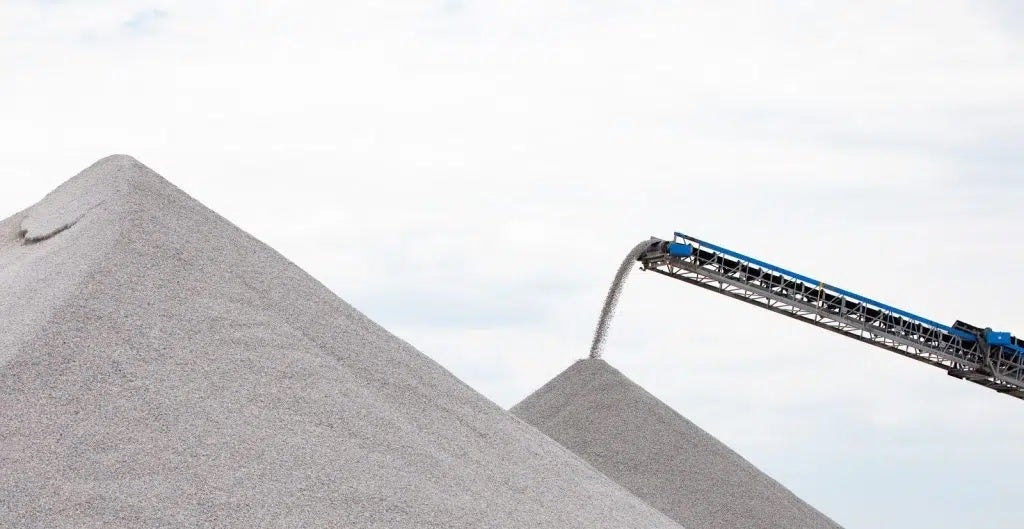
A well-designed radial stacker conveyor can bring efficiency and flexibility to your aggregate stockpiling process while reducing your material handling costs. Is it worth the investment? We take a closer look at radial stacker conveyor costs.
Why choose a radial stacker?
Radial stacker conveyors offer an effective solution to a common stockpiling challenge: while piling aggregate higher lets you make better use of your available space, higher stacks are also more difficult to work with efficiently and safely, limiting productivity and potential revenues.
Radial stacker conveyors lift your aggregate to a discharge point up to 40 feet above your stack while also rotating to deposit material in a higher and wider arc. That allows you to heap more material in your space while not having to reposition equipment.
That can help deliver enhanced safety and profitability, as well as reduced costs and wastage.
- With elevation grades up to 20° and lengths of 150 ft or longer, radial stackers can move some materials at rates up to 1,200 tons per hour (TPH) and can be built to handle a wide variety of common aggregates.
- Telescoping: Allowing the discharge head to move further from the loading point increases capacity by allowing even larger piles to be stacked.
- Portable: Lighter-weight structures are used in smaller portable units, designed to be moved between temporary locations, such as road camps or wellhead supply points.
Elements of a radial stacker conveyor
The steeply inclined conveyor of a radial stacker is instantly recognizable at any site or yard, but there are several key parts to any radial stacker system:
- Fabricated truss — the framework that supports both the conveyor and material load.
- Radial undercarriage — the moveable assembly that allows the stacker to rotate.
- Conveyor belt – Designed according to the nature and properties of the material being handled.
- Head section — at the discharge point at the end of the conveyor belt
- Tail section — the point where material is loaded onto the conveyor belt
- Drive unit — a motor and reducer mounted at the head section and connected to the discharge pulley.
Radial stacker cost drivers
Radial stacker conveyors are complex, custom-built pieces of equipment. The overall radial stacker cost is determined by several key cost drivers:
- TPH — the tonnage per hour you need your stacker to handle
- Elevation — the maximum height your equipment needs to stack to
- Width – the maximum arc your stacker needs to rotate through
- Material properties — the weight and density of your aggregate
- Material nature — specific properties of your material that need to be accounted for
- Portability — do you need to be able to move your unit to new sites?
Costs and options
Let’s take a look at how these considerations drive decisions about stacker design, starting with the conveyor belt itself.
Conveyor belts
The maximum TPH your stacker will need to handle will determine the width of your stacker’s conveyor belt and the speed at which it will need to run. Other critical properties in determining conveyor belt speed and width include weight and density of your aggregate, and moisture and dust levels.
Conveyor belts can be 36-48 inches wide and, depending on your material, will be either of steel-belted or multi-ply construction to withstand maximum load levels at loading. West River Conveyors estimates conveyor belts account directly for 3-5% of the total cost of your stacker, but also affect a wide range of other machine specifications.
Structure
Foremost among these is the fabricated framework that supports the conveyor system and its associated drive, reducer, and idlers. The actual dimensions of the structure are dictated by the elevation the radial stacker needs to serve, although this can be limited by the maximum grade slope up which a particular aggregate can be moved efficiently by the available drivers.
Conveyor structure can measure anywhere from 30-150 feet or longer, allowing discharge heights of up to 40 feet with elevation grades of 18-20°.
Fabricated truss
Larger conveyor structure will always require traditional steel truss construction but smaller units can be built using a 10×25 channel support structure. This is a major cost consideration: truss-built structures can cost 20% more overall than channel-supported conveyors.
Either way, conveyor structure needs to be able to support the full weight of the equipment plus the maximum rated load, as well as additional temporary loads from snow or wind. Constructors like West River Conveyors build equipment from a range of materials based on load requirements, cost, and the environments in which the stacker will operate.
Whatever material you choose, expect your conveyor structure and truss construction to account for at least a third of the total metal cost of your conveyor — or about 10% of the total cost of your unit.
Radial undercarriage
The radial undercarriage allows a conveyor to rotate so material can be discharged along an arc. The undercarriage typically accounts for about 15% of the cost of your unit.
However, while many smaller, portable units can be raised or lowered manually using a pulley system, larger conveyors come equipped with a dedicated hydraulic rise system. A dedicated hydraulic system, including a cylinder, motor, hydraulic pump, and power pack can add 5-10% to the cost of your unit, depending on the lift height required.
Drive unit and reducer
The capacity and elevation of your conveyor system will also affect the minimum size of the drive unit needed to power it and the reducer needed to effectively deliver power to the conveyor mechanism.
Usually mounted at the discharge head and attached to the discharge pulley, drive units need to be able to lift the maximum rated loading weight of your conveyor from a standing start. The drive unit and reducer will typically account for 7-10% of the total cost of a conveyor. Other important components that need to be costed into a unit include:
- Frame-mounted idlers to support the belt, accounting for about 7% of unit cost.
- Head section: Other power equipment mounted near the discharge head, such as the discharge pulley, take-up screw, and additional idlers can account for 5-10% of the total cost.
- Tail Section: Hoppers and other loading and safety equipment at the base of the conveyor belt can also account for 5-10% of your conveyor’s cost.
- Catwalks to access the conveyor belts on larger units.
Additional cleaners and skirting on the conveyor belt to reduce dust and protect workers from falling material.
Street-ready stackers
Smaller lightweight stackers can be supplied in a “street-ready” trailer format, allowing them to be towed to the site by a large truck or semi. These units feature specialized folding mechanisms, as well as required brakes and lighting, and are usually more expensive than a similar-sized fixed conveyor.
Radial stacker conveyor cost estimates
These percentages provide an overview of the variables that go into determining the price of each unit. Since radial stackers are custom-made equipment, it’s very difficult to provide “out of the box” per-foot prices for this type of machinery.
West River Conveyors suggests the following guidelines for radial stacking conveyor equipment:
- Fully-featured 150ft stacker with rise hydraulics and catwalks: $150,000-$170,000
- Entry-level 50ft stacker, manually raise and lower: Starting at $50,000
Why West River Conveyors?
Since the early 1980s, West River Conveyors has been engineering and building specialist conveying systems to move a wide range of materials in the most challenging environments. We also replace or rebuild equipment to extend the life of your existing conveyor system.
Talk to West River Conveyors today about how we can help you cut costs and build efficiencies by taking your materials handling capabilities to the next level.