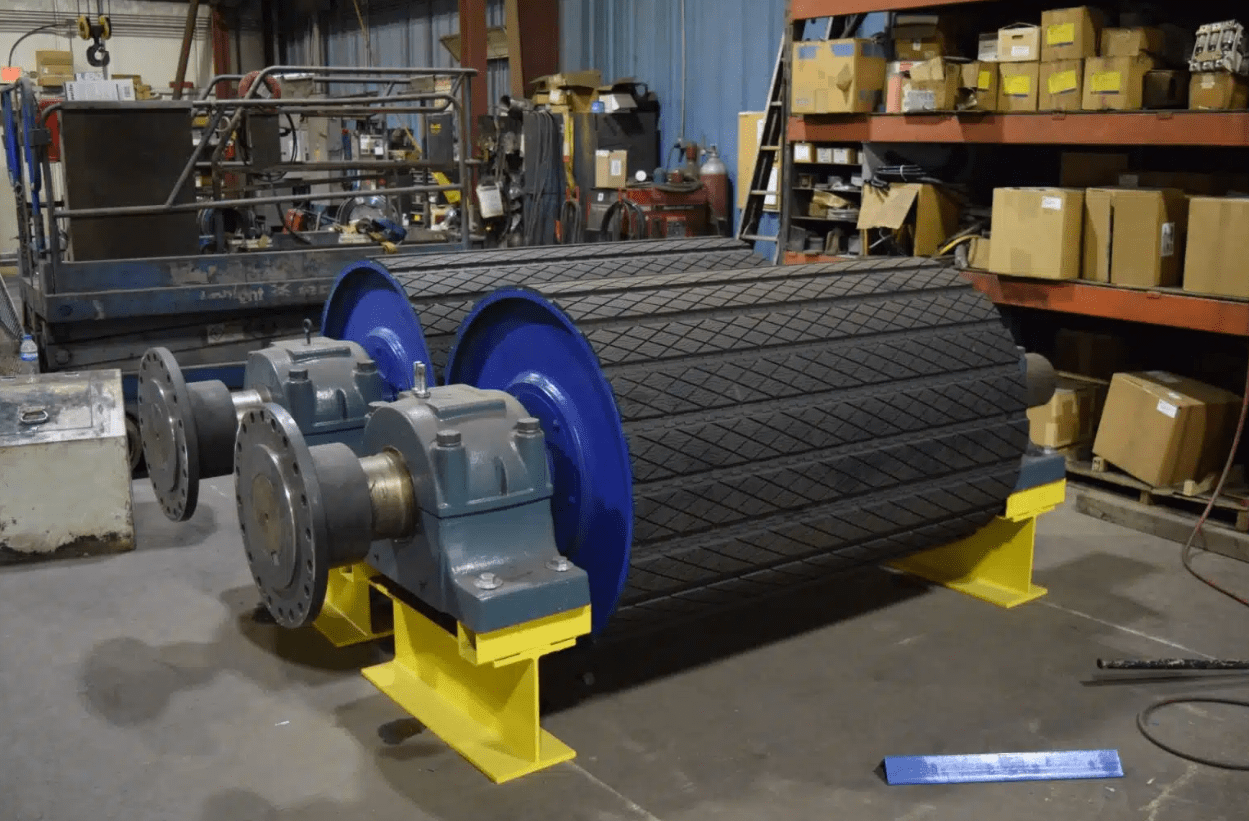
A pulley is always a pulley, right?
Unfortunately not. Very similar mining conveyor systems often require different components, sometimes leaving operators drowning in spares that they may or may not need.
All that inventory is cumbersome and expensive to maintain. Worse, in the event of a failure, it can leave your on-site team scrambling to find the right part during a costly shutdown of your underground or overland operations.
It doesn’t have to be that way. While conveyor systems do need to be customized for particular loads and terrains, the systems driving them rely on very similar technology. It’s possible to do a lot better building conveyors that make use of common, standardized parts to get the job done.
PLUG AND PLAY: GETTING SMART ABOUT CONVEYOR PARTS
Although it might not be topmost in engineers’ minds when designing a new conveyor system, it is important to think ahead about the availability of critical parts to avoid big headaches down the line, especially at remote sites. Similarly, taking the time to plan ahead for parts availability and redundancy can reap some rich rewards.
In this blog, we consider the problems caused when conveyors designed with unique or hard-to-find components break down, as well as the benefits of prioritizing standardized parts and design practices across all your conveying equipment.
DOWNSIDES OF NON-STANDARDIZED CONVEYOR PARTS
Most large underground or overland conveyors are customized for each application. When designers choose different parts to achieve the same basic conveyor functionality, it comes with some real-world consequences.
1. HIGHER COSTS
Unique parts are generally more expensive to purchase, replace, and store as spares. Plus, the need to maintain a large and diverse inventory ties up capital and storage space, both for end-users and parts suppliers.
2. DOWNTIME AND LOST PRODUCTIVITY
When critical parts fail without a replacement accessible, particularly at remote sites, the result can be hours or even days of downtime and production disruption. It also means more of your staff are involved in trying to trace parts or improvise a solution.
3. COMPLEX MAINTENANCE AND REPAIRS
Non-standard parts make maintenance and repair efforts more complicated. Technicians need to be familiar with a wide variety of parts and systems, which can lead to longer repair times and a greater chance of mistakes or do-overs.
4. OBSOLESCENCE AND SCALABILITY
Being reliant on large inventories of parts from diverse suppliers may make it more likely that specific parts become obsolete or no longer supported. Broad inventories also make scaling up or expanding your operation more difficult.
BENEFITS OF STANDARDIZING CONVEYOR DESIGN ELEMENTS
While it may involve more work at the design stage, taking the time to ensure parts are interchangeable can offer big financial and operational benefits.
1. OPTIMIZED RESOURCES
Standardized parts streamline procurement processes and reduce the need to keep a large, varied inventory available, saving money and simplifying inventory management for both end-users and suppliers.
2. REDUCED DOWNTIME, SIMPLIFIED REPAIRS
Having readily available spares means quicker repairs and less downtime, ensuring more production uptime and less production. Technicians will become more familiar with replacing the same parts, saving time on money on training and support.
3. EASIER DESIGN AND UPSCALING
Standardization also simplifies the design process for future conveyor systems. Engineers familiar with standardized components can design new systems more quickly and efficiently with real-world information on how specific components work with certain loads and belt tensions.
KEY COMPONENTS FOR STANDARDIZATION
Realistically speaking, there are limits on how much standardization is possible given the different distances, grades, and belt loading requirements individual conveyor systems will have. Standardization works best for high-value components that are the most expensive to keep on hand or duplicate in inventory.
STANDARDIZING CONVEYOR COMPONENTS: BEST PRACTICES
How can you get ahead when it comes to standardizing pulleys and other parts for your conveyors? Leading players in the field adopt the following best practices to limit costs and save time when it matters.
- Maintain an inventory of critical spares: Work with your equipment supplier to pare down your on-hand inventory of essential parts like motors, gearboxes, and pulleys. It’s important to have the parts you need, but equally important to limit over-duplication.
- Document and label components: Create and maintain a proper database of the parts you do have using parts numbers or other identifiers. Finding the parts you do have quickly can be a game-changer during an unplanned stoppage.
- Leverage design software: Tools like Belt Analyst can help estimate load capacities and ensure proper pulley sizing and belt tensioning, preventing premature failures. Running the numbers now can identify the best components to keep stocked for switchouts.
- Develop strong supplier relationships: Partner with a reliable, experienced parts supplier like West River Conveyors to identify standardization opportunities. We’ll ensure you have the parts you need and back you up with our own in-stock inventory.
CASE STUDY: SLEEK DRIVES OUTFIT FOR BLACK PANTHER
What do conveyor parts standardizations and reduction look like in practice? West River Conveyors, a leading manufacturer of bulk materials handling equipment, worked with Black Panther Mining to minimize spare parts and pulleys needed for the company’s coal operations.
Black Panther approached West River to design and deliver conveyor systems at their Oaktown Fuels 1 and 2 mines. The aim from the outset was to power the company’s belt line using the minimum number of belt drives and other parts.
It’s common to encounter conveyor equipment from the same company at a mining operation, yet with significantly different components, which can cause problems down the road.
By optimizing design early in the project planning process, West River was able to provide Black Panther with an effective underground handling solution using just two belt drives. The Dual 150HP and Dual 300HP alignment-free conveyors in use at the site use only two styles of terminal group packages, including the pulleys, take-up units, and tail sections
The company now operates over 30 of the West River-supplied terminal packages at Oaktown Fuels, all with standardized drives, pulleys, and other critical components.
“From the beginning, we wanted to standardize our conveyor equipment,” explains Black Panther General Manager Brad Rigsby. “We knew we wanted to minimize the number of spare parts and pulleys. This is the first time in my career that we’ve been able to accomplish this.”
WEST RIVER CONVEYORS: YOUR SMALL PARTS PARTNER
When you’re hauling materials day in and day out, small things matter — like the spares you need in the event of an equipment failure.
At West River Conveyors we aim to simplify conveyor ownership by building equipment with simple, repeatable designs that use the same components to deliver the powerful, predictable material moving performance you need.
That helps you keep your operation running smoothly and makes it easier to scale up or repurpose equipment down the line. We’ll also advise you on the best mix of components to keep on-site for equipment switchouts and back you up by keeping your parts on hand in our own inventory.
You’ve got enough to think about without having to worry about spare parts. Talk to us about your underground and overland bulk transport challenges. We’ll work with you to develop robust, reliable conveyor solutions that run longer than the competition and are simpler and more cost-effective to keep operating.
Click below to call or contact us today to get started.