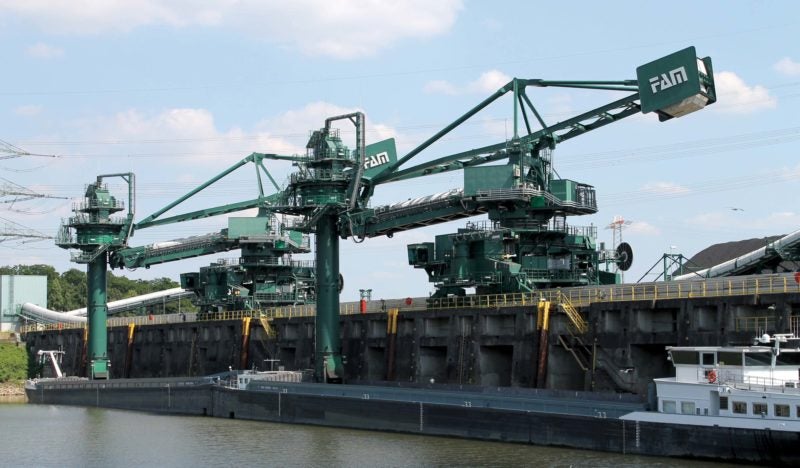
FAM Magdeburger Förderanlagen und Baumaschinen is a medium-sized company headquartered in Magdeburg, Germany. It has a long history as a manufacturer of handling and conveying systems with a heritage dating back to the 19th century. Employees of the FAM Group have expertise in bulk materials handling, mining machinery, stockyard systems, mineral processing, loading equipment, conveying facilities and port technology. Well over half of the FAM workforce are engaged in engineering.
One of the FAM’s major sectors of activity is focused in the bulk cargo handling market, amongst others, in the field of ship unloading technology. For bulk materials unloading, two types of handling systems are basically deployed: continuous and discontinuous. In the continuous mode ship unloading by means of bucket elevators prevails, while in the discontinuous operation the main device used for unloading is a rope grab. Though, given the growing development of scooping-up bucket elevators, continuously working unloading systems are now being increasingly used to efficiently handle large mass flows.
Bucket elevators are also more efficient and flexible in the residual emptying of a cargo hold than grab-type unloaders. Moreover, the continuous mode of operation helps reduce the environmental footprint. It allows for dust-free and low-noise operation being at the same time very gentle on the material handled.
The bucket elevator’s high flexibility is facilitated by its specific design typical of CONTI ship unloaders. The machine’s superstructure with an unloading boom and a counterweight boom is rested on a portal and can turn around vertical axis, while the machine travels along the jetty. The rotating discharge bucket elevator is located at the head of the unloading boom, which can be adjusted in height.
While the vertical and horizontal conveying pathways are fully enclosed to prevent noise and dust emissions, the bucket elevator boot incl. a triangular chain guide is not covered. This design enables extraction by the scooping buckets in a similar way to the bucket wheel or bucket ladder principle. The material is taken up on the lower horizontal section of the bucket chain strand.
At the bucket elevator head, the material is dumped onto a horizontal turntable which transfers it further to the boom conveyor. Compared to the various chutes systems, this particular design allows for considerable reduction of the bulk material’s height of fall and the installation height of the revolving bucket elevator, as well as helps eliminate dust and noise at the bucket elevator head.
The boom conveyor transports the material to the feeding hopper arranged at the ship unloader’s pivoting axis from where it is further transferred by a reversible hopper discharge conveyor to the terminal’s jetty conveyors.
The two steel link chains of the bucket elevator strand are permanently lubricated. For this reason, they require little maintenance and are subject to minimum wear. The chains are selected with smaller chain pitches to allow the drive sprockets and the deflection sprockets to be furnished with a maximum amount of teeth. This arrangement helps reduce the development of noise resulting from the ‘polygonal effect’.
Depending on the port facility conditions, it is often necessary to discharge a number of different material types. This is when discontinuous ship unloaders are often deployed due to their ability to handle bulk materials of any particles sizes and properties. These machines are very flexible owing to their simply exchangeable grabs of diverse shapes and sizes which facilitates relatively rapid adaptation to the bulk material to be handled. When small or medium unloading capacities are required, grab-type unloaders with a movable superstructure and a single-link or double-link luffing boom are put into operation.
When high handling capacities are required, grab-type unloaders with rail-mounted portal bridge are employed. These machines have a horizontal bridge girder with one or two cantilever arms (also foldable) on which a rope-controlled trolley moves the grab both horizontally and vertically at high traveling speeds (up to 4m/s) and lifting speeds (up to 3m/s). The load cycle of the grab is similar to that of the grab unloader with a rotatable superstructure, just instead of the horizontal movement of the grab performed by the luffing boom, the grab’s is moved along the bridge girder by the trolley.
This is where FAM are involved. We supply installations, components and know-how to resolve your handling tasks.
FAM is the address you should challenge.