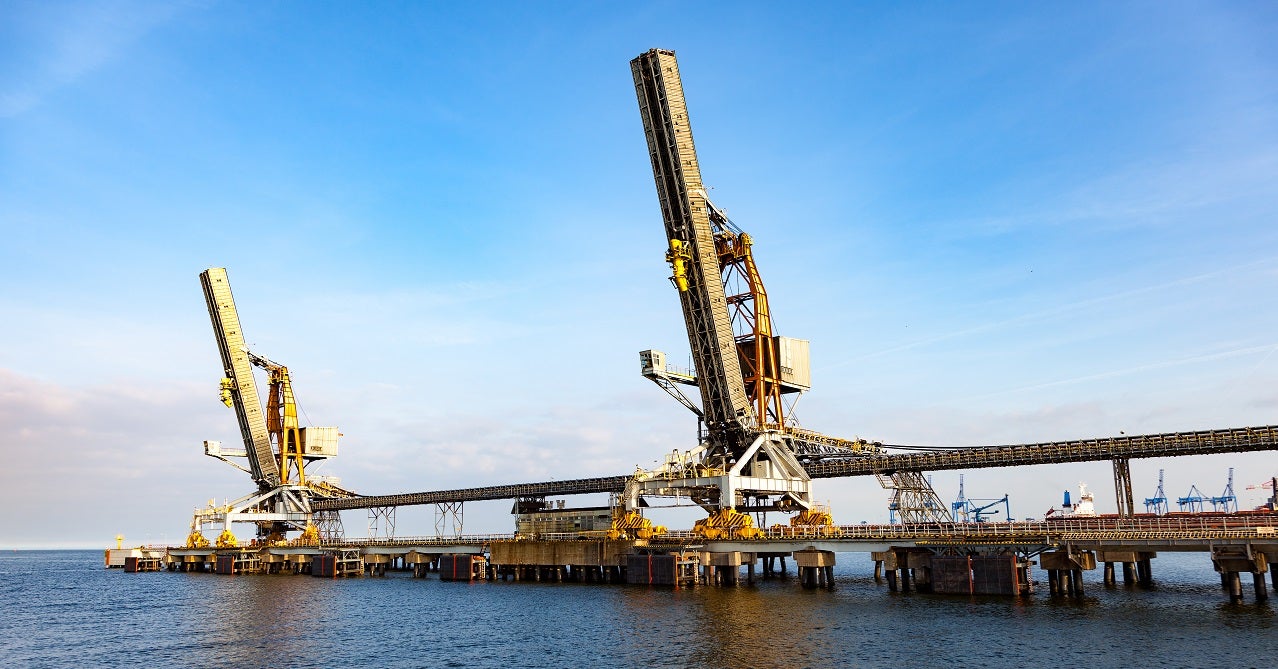
Conditions in mining are very tough. The presence of dirt and dust puts extreme stress on all components and equipment, as well as the surrounding environment. By installing sealed bearings instead of open bearings on all conveyors in their shipping port, one mining company secured uptime for critical conveyors, overall equipment efficiency for the entire site, and reduced environmental impact in a sensitive ocean area.
Sealed bearings on all conveyors
We are in the beautifully situated modern shipping port of one of the world’s largest mining companies. We are surrounded by some 50 conveyors, which are used to unload iron ore from rail wagons, transport it to depots on the dock and load ships. There are both old and new conveyors, and critical and non-critical conveyors. In total, there are about 500 bearing positions on these conveyors. All of them have sealed SKF Explorer spherical roller bearings – a choice that has led to positive results for the entire shipping port.
Fewer unplanned stops
The most critical conveyors are those that are used for loading ships. Any delay caused by a breakdown here would quickly result in high costs. According to the maintenance manager, sealed spherical roller bearings are the ‘obvious tonic against unpleasant bearing-related breakdowns when ships are loaded’.
Longer bearing service life
In addition to fewer unplanned stops, the use of sealed bearings has reduced the amount of planned maintenance stops too, on both critical and non-critical conveyors. Calculations made by the mining company indicate that switching to sealed bearings has prolonged their service life from 1.5-2 years to five years. That’s the same lifetime as for the pulley lagging, so the reward is not only fewer bearings to purchase and manage, but also better-aligned service stops – as well as improved overall equipment efficiency for the entire site.
Lower grease consumption, longer relubrication intervals
Having a large shipping port in a beautiful coastal area where fishing is a large part of the local economy of course means that environmental impact has to be kept to a minimum. By using sealed bearings, the mining company has been able to reduce grease leakage significantly. The change to sealed bearings has reduced grease consumption from 2kg/month down to refilling only a small amount every three months. In the course of just one year, approximately 10t (or 50 barrels) of grease is now being saved.
Lean maintenance
By reducing the lubrication interval significantly, the company has also been able to streamline the staffing requirements of its maintenance operations. The work of relubricating the entire line of conveyors is now performed by just two people, where four people were previously required to do this work. Less need for lubrication also means less exposure to dangerous lubrication points, which has reduced the risk of injury.
An uncomplicated design
The use of sealed bearings has reduced the need for central lubrication systems for conveyors. The less complicated design with fewer components means fewer problems and less maintenance.
Economic profit, environmental gains and peace of mind
The shift from open bearings to sealed SKF Explorer spherical roller bearings has meant a lot for this mining company. The significantly longer service life, minimal grease consumption, longer relubrication intervals and the uncomplicated conveyor design have led to higher overall equipment efficiency, economic profit and environmental gains – as well as peace of mind for the site and maintenance managers.
Longer service life
- Bearings last until the planned maintenance stop
- Reduced risk of failure
- Secured uptime for critical conveyors
- Lower total cost of bearing purchase
Reduced grease consumption
- Lower grease purchase cost
- Lower grease destruction cost
- Smaller environmental footprint
Longer relubrication intervals
- Reduced need for maintenance
- Easier to perform maintenance according to plan
- Less risk of injury due to less exposure
The shift to sealed bearings meant for the mining customer
- Only half of the people working with relubrication were required
- Reduction of grease consumption equivalent to 50 barrels (or 10t).
- Elimination of complicated lubrication systems
- Secured uptime for critical conveyors
- Reduced risk of injury due to less exposure