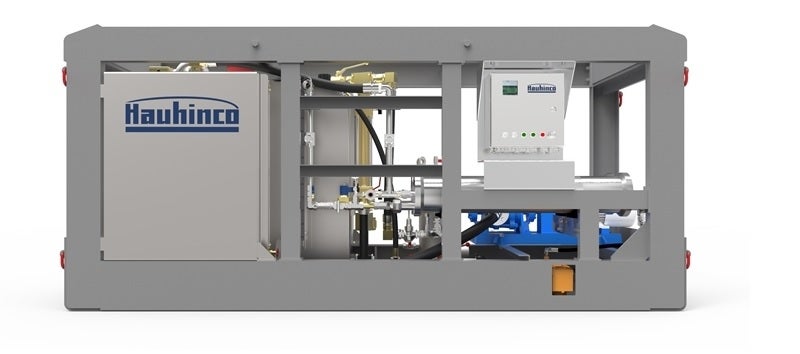
High-pressure pumps generate the necessary pressure for the roof supports in the longwall. The pump stations also enable roof supports to move along the face of the coal seam. The necessary performance in terms of litres and pressure is dependent on the excavation rate and the supporting power required by the supports. In high-capacity longwall applications, flow rates of up to 1,270l/min at an average of 340bar are currently required.
Water-spray pump stations minimise dust formation in the longwall. Plunger pumps supply the shearer water-spray, or the coal plow water-spray and the cooling systems of the drive motors with the necessary pressure and volumetric flow rates. The pumps typically deliver 6,00l/min at 90bar.
A close collaboration has also taken place with Caterpillar Global Mining Europe in Lünen, Germany, jointly looking for a solution to significantly improve the water quality in an underground longwall in a Polish mine. At the time, Caterpillar was implementing a complete longwall in the mine, but was concerned about the durability of the hydraulics props, due to the high salt concentrations in the water.
As a result, an extensive analysis of the mixing water was prepared. It is well known that salt accelerates corrosion.
Experience has shown that this is not the only mine with such contaminated water and that it has already led to problems in longwall operations.
A solution to corrosion
In collaboration with Caterpillar, Hauhinco developed a solution for this problem and tested it on its own test-bench. Using a reverse osmosis unit, it was possible to filter out the salt content and other substances identified within the mixing water; a quick and simple solution for the problem was needed. However, it was necessary to develop this into a system for underground mining, which needed to be suitable for the hard conditions in underground mining and able to supply the required flow rate of cleaned water for the longwall. After less than five months, the result was a high-performance water treatment unit with the necessary approvals for underground mining.
The system is installed in a 3,300mm x 1,519mm x 1,100mm base frame and can be simply integrated into an overall system. Therefore, an upgrade of an existing high pressure station is also possible and an immediate improvement in water quality can be achieved. Cavitation problems in the props of the roof supports can be prevented from the start, reducing lifecycle costs and protecting mine investments.
Design and functions of the water treatment system
The integral components of the water treatment system are the filtration unit, the reverse osmosis unit, the tank and the control system.
In the first stage of the treatment process, the raw water enters a multi-stage filter. In the next step, the water enters the reverse osmosis unit.
In the standard design, this unit consists of one pressure pipe with a membrane, a metering pump, a dispersant tank, two flow monitors and a needle valve. For pressure-monitoring purposes, there are also two pressure gauges installed in the raw water feed pipe and the concentrate drain of this assembly. A metering pump mixes the raw water with a dispersant mixture and pumps it through the pressure pipe.
The membrane separates the raw water into permeate, i.e. purified process water and concentrate, wastewater. Optimally, the ratio of permeate to concentrate should be 1:1, which is set using the two flow monitors and the needle valve. The standard design includes an integrated 1,000l tank for storing the process water. The customisable tank is equipped with an electrical level monitoring system and a visual display to monitor the filling level.
The ‘automatic operation’ and ‘test operation’ modes are pre-programmed in the control system. The former allows the automatic treatment of the raw water and delivery of the process water from the tank to the pump station. In ‘test operation’, water treatment system components can be individually activated and deactivated.
Results of the first system
The first water treatment system was put into operation in 2010. From 2,000l/h of salty raw water, it was possible to prepare 1,000l/h of clean water. The raw water had a conductivity of 1,990µS. After treatment, the value for the clean process water was just 19.5µS, showing the effectiveness of the system. The system itself runs fully automatic in the treatment process, so no manual operation is required. The degree of contamination of the filters is displayed. The maintenance-friendly structure allows fast, cost-effective and simple replacement of the filter elements. Even after five years of underground operation, the system still runs flawlessly and supplies the roof supports with clean medium.
Caterpillar Global Mining Europe engineering for roof support head Hydraulics Franz-Heinrich Suilmann sees the preparation of the emulsion for the longwall hydraulics by a water treatment system based on reverse osmosis as a practical alternative. Corrosion damage in the hydraulic systems can be avoided, ensuring sustained compliance with Caterpillar’s quality requirements for the hydraulic fluid.
Adaptation to water quality and required flow rates
Since the launch, Hauhinco has already commissioned a number of systems in coal mines. The system has also been continually developed since its launch and adapted to the increasing requirements and respective circumstances. In addition to high salt content, the water samples from the mines also contained high levels of chalk, iron and other solids.
Due to the increasing requirements regarding required water volumes in the longwall, several system variants have already been developed over recent years. Tank sizes and treatment volumes can now be flexibly adapted to the requirements. The largest system designed so far has eight membranes and can supply up to 8,000l/h of water.
Conclusion
In underground mining, a water treatment system is a logical and reasonable addition to a longwall hydraulic system. Its compact design and the manufacturer-independent, problem-free integration into a pressure supply station can be fundamental in achieving effective operations, while minimising lifecycle costs. Compared with the overall costs of a longwall, the additional investment is small and, considering the lifecycle costs and the service life of roof supports, it pays off.