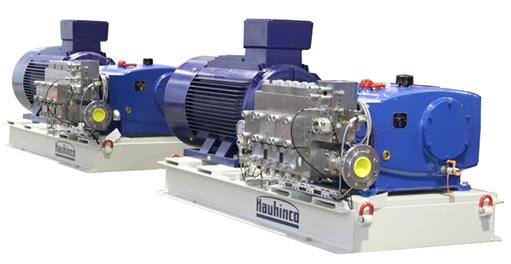
Hauhinco has been contracted by a customer to engineer a descaling system for a new rolling mill for stainless steel panels. The new descaling system should reach the best power and energy efficiency combination for the current requirements but should also have enough reserves for future work piece sizes.
Hauhinco mastered this challenge through an indirect drive solution consisting of a redundant high-pressure pump system and a high-pressure accumulator system. As a drive station, two EHP-3K200 high-pressure plunger pumps with a reduced input speed are used. By these measures a continuous pump operation for the current conditions is reached on the one hand and on the other hand enough power reserves for future enhancements are given.
The automatisation solution is specifically designed for the system and includes a typical charging mode of the high-pressure accumulator system in correlation with the storage level, however also allows a decrease and increase of the pressure level through parallel controls of the compressor and high-pressure pump. With regards to valve technology, Hauhinco uses the metal seat technology which has been proven in water hydraulics for decades. The valves use a wear resistant sealing system consisting of a special PU-compound, which has less seal friction and thus less heat development.
Besides the delivery of the mentioned products, Hauhinco supports the partner from the nozzle design and the performance calculations up to the commissioning including the integration of external delivery scopes. The support during the first days of operation after the commission guarantees the customer a sustainable optimisation of the production.