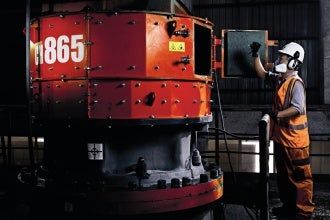
Sandvik Mining has expanded its CH800 series of mining cone crushers, launching two technologically advanced models that improve productivity and profitability in the mid-range segment.
Sandvik CH860 for high-capacity secondary crushing and Sandvik CH865 for high-reduction tertiary and pebble applications feature higher crushing forces relative to mantle diameter and a 500kW motor. The new crushers combine a range of advanced automation features for a more secure and productive process.
Product line manager for cone crushers at Sandvik Mining Andreas Christoffersson said: "We scaled down our larger Sandvik CH890 and Sandvik CH895 mining cone crushers to create two mid-range models that are even more productive, robust and reliable, and feature enhanced environmental, health and safety characteristics.
"Depending on the application Sandvik CH860 and Sandvik CH865 outperform competing equipment in the mid-range segment by as much as 30% and deliver a two-fold increase in performance range."
The intelligent systems in Sandvik CH860 and Sandvik CH865 enable real-time performance optimisation, while smart, compact design solutions reduce dynamic loads and minimise engineering and installation work. The crushers feature fewer moving parts than competing models, according to Christoffersson. Non-welded, bolted liners on the top and bottom shell enable safer, easier maintenance.
Both new crushers also feature the company’s automatic setting regulation control system (ASRi) and hydroset, to ensure automatic operation at peak performance around the clock. ASRi constantly monitors pressure, power draw and mainshaft position, and automatically adjusts the setting during full load.
The hydroset main shaft support system provides protection from overloads by permitting tramp iron and other uncrushables to pass through the crusher before automatically returning to the original setting. The system automatically compensates for crushing chamber wear to provide consistent product size.
"Hydroset enables us to incorporate our unique PLC-controlled electric dump valve for tramp iron protection, which significantly reduces pressure peaks and mechanical stress on the crusher, greatly improving reliability," Christoffersson added.
Close to one year of rigorous testing in a Chinese iron ore mine has produced excellent results.
"In these challenging times mines are often looking for increased productivity without necessarily expanding their plant," Christoffersson said.
"Sandvik CH860 and Sandvik CH865 are easy to install as replacements to achieve this. In the test site we replaced a similar sized crusher, on the same foundation, to greatly increase final product and significantly extend crushing chamber liner life. The electric dump valve repeatedly proved its tramp iron protection value, reducing costly unplanned breakdowns."
Visit the company website to learn more about Sandvik CH860 and Sandvik CH865.
Image: The new Sandvik CH865 for high-reduction tertiary and pebble applications. Photo: courtesy of Sandvik.