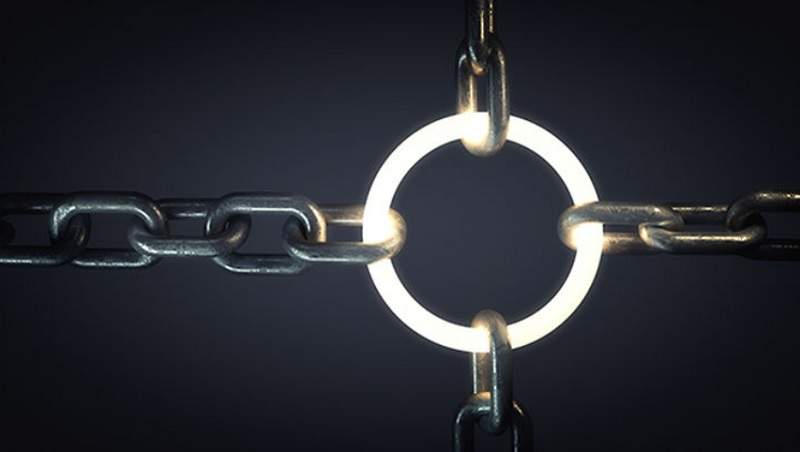
Our work at Davey Bickford Enaex is ultimately centered on the optimisation of workflows. When our Global Technical Solutions (GTS) experts configure next-generation blasting designs to individual mining sites, the immediate result is smarter and more controlled shots. The real benefit comes later, as downstream activities begin to accelerate. This includes everything from extraction to crushing and product yield.
Being of this mindset, we’re keenly interested in the larger discussion around supply chain optimisation in mining, and how existing concepts of workflow are being challenged by new modes of thinking.
From the research we’ve come across – and from many of the conversations we’ve had in the field – the sharing of quality information is synonymous with supply chain optimisation. Countless inefficiencies in the supply chain are the result of insufficient information and poor communication. Historically, key decisions have been made within the exclusive visual horizon of any one department or company. Other departments and companies react. A series of blind ripples goes up and down the supply chain. In large part, this is because we had limited means to generate and share key data. Mindsets and habits were developed accordingly.
Today, the means to generate and analyse key data are unprecedented. Advanced algorithms can highlight conflicts and streamline workflow. Different factors and approaches can be modelled, so that decisions are deeply informed and transparent. For effective decision making across the chain, data generation and shared analysis will be a critical currency moving forward.
Expertise will certainly be another. It’s one thing to have charts and graphs, and quite another to work with partners who have seen it and done it many times before. This is something that experienced players in the industry understand. It is something that new professionals entering the field will inevitably learn with the passage of time. Data generation and analysis are integral, but they cannot shift core inefficiencies within a single part of the chain.
Companies or departments that handle extraction may soon be asking their partners why automated transport is not being used to alleviate pressure on other links of the chain. Those who handle refinement or shipping may be asking their partners why modern digital blasting solutions are not leveraged in order to break rock more efficiently and unlock widespread gains. As methodological upgrades become available in each of the key areas of the mining supply chain, each partner owes due diligence to the others. The goal is to optimise the total value of the mining supply chain so that waste is minimised and gains are maximised across the board. Social and environmental demands must also be considered.
A 2018 article in South African-based publication Mining Weekly highlights the growing consensus that shipping and transportation logistics are particularly important to supply chain optimisation in mining, and that we should be thinking more about the total value of the supply chain. How can distinct entities develop shared skill sets to remove unneeded drag? This point is highlighted in the article where it states:
“Major challenges in mining supply chains in Africa were related to skills and the capabilities of suppliers around mines, said Govender, noting that mining houses should ensure that they develop skill sets with suppliers and companies around them.”
Knowledge sharing is a powerful antedote to the silo mentality and all its downstream effects. We have seen this approach increase productivity time and time again for our customers. After all, is it not naïve and counter-intuitive to believe that certain players on the chain can optimise their own processes, regardless of how other components of the process are operating?
Today, we’re seeing with greater clarity how inefficiencies are reflected up and down the chain. We’re seeing how the biggest creative shifts happen not behind closed doors, but out in the open amongst partners. Upgrading processes at the micro and macro levels is important if the industry is to be truly optimised.
Our body of work in the realm of digital blasting has always been about challenging the status quo, breaking down walls, and opening the way to mutual successes. This collaborative impulse is as much the future of mining as any robot, algorithm or data as a whole.