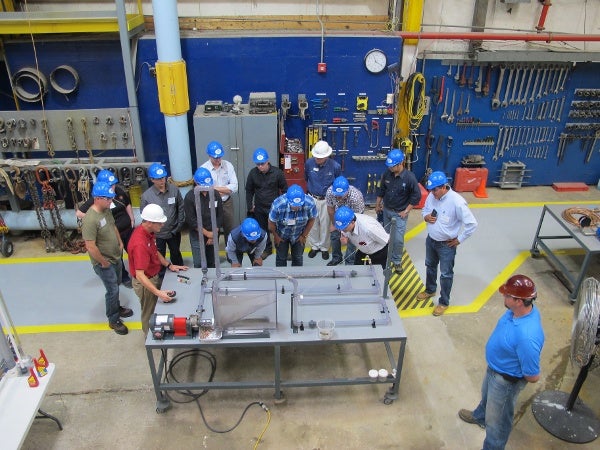
When it comes to efficient slurry pumping, understanding how the solids within a slurry behave is very important. Depending on the particle size, distribution, concentration, and character of solids, the slurry can be either ‘settling’ or ‘non-settling’. Non-settling slurries affect pump and pipeline performance in different ways from settling slurries. But what distinguishes a settling slurry from a non-settling slurry?
Settling vs. non-settling slurries
A settling slurry contains particles that have a tendency to settle out of the liquid and form a bed at the bottom of the pipe. Larger and denser particles are typically settling, with the particle size limit usually considered to be somewhere between 40-75 microns.
In contrast, a non-settling slurry contains smaller particles that won’t settle to the bottom of the pipe within the industrially relevant range of pipeline velocities. Instead, the particles remain suspended within the flow field. Non-settling slurries often have very high viscosities compared to water and are often non-Newtonian, which in the case of mineral slurries means that the viscosity varies with the applied strain rate. This can make assessing a pump’s head and efficiency more complicated. For non-settling slurries, an important factor to consider is the viscous losses or the loss of pressure (or head) that occurs in the pipeline and pump due to the slurry’s viscosity.
An accurate prediction of the pipeline friction losses and pump performance derates allows pump operators to determine what type of slurry pumps are needed and how to configure them. The settling behaviour of solids has a big effect on pipeline friction losses and pump performance derates, according to GIW Industries, Inc., Senior Hydraulic Engineer John Furlan.
“If you’re pumping something with a higher density but similar viscosity, like mercury, the pump will put up the same amount of head, expressed in height of liquid being pumped, as it would on water,” Dr Furlan explains.
“But when you start adding solids, you have to derate the head and efficiency to account for their presence. Partly because the solids’ densities are different from that of the liquid, the slurry stops acting like another pure liquid would. The particles don’t faithfully follow the flow, and settling slurries segregate as they go through the pump — so you get additional losses due to the particles stratifying and from the Coulombic friction they generate when sliding against the inner hydraulic surfaces of the pump. Additionally, since the particles are solid, they do not transmit pressure as a liquid would, which also induces further degradation of the pump performance.”
Non-settling slurries often have high viscosities and small particles, so they flow differently than settling slurries; there is much less segregation of the particles, and the particle concentration within the pipeline is nearly constant, or homogeneous. However, the number of variables associated with their flow behaviour, or rheology, can make a prediction of the losses difficult and means that some type of testing or prior experience pumping a particular slurry is required in order to accurately predict pump and pipeline performance.
“In the case of the non-Newtonian slurries, viscous effects are primarily responsible for the increased losses, and they typically end up causing the efficiency to be affected more than the head — and the pump derates to increase with increasing flow rate, for constant pump speed,” Dr Furlan says.
“Depending on the type of slurry, there are different reasons for why you get the losses, but either way you often end up with pump head and efficiency curves that are lower and pipeline system loss curves that are higher than the corresponding water curves.”
Since the physics at play in the pump and pipeline are different for settling and non-settling slurries, different models are used to predict pipeline friction and pump performance derates for the two different slurry types. In either case, calculating losses in the most accurate way possible is vital to ensure the pump is operating optimally.