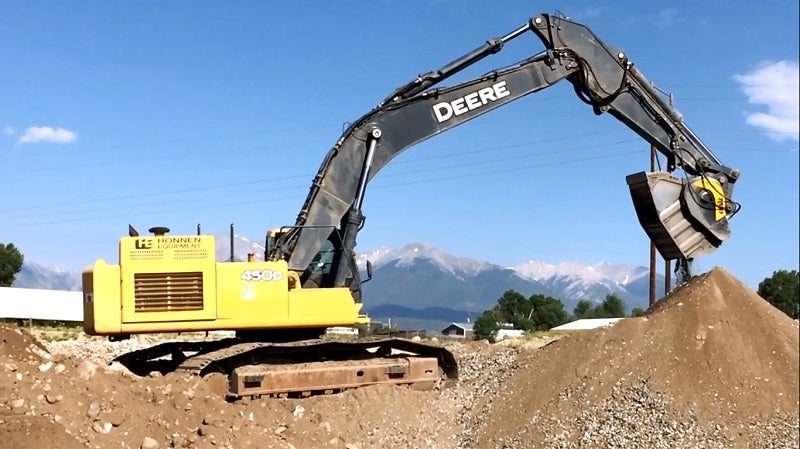
When Avalanche Excavating was awarded a project in April 2015 that dealt with 11 blocks of underground utilities, storm sewers, and water lines in Salida, Colorado, US, the company knew it would not have much room to navigate the spoils it would encounter.
Both Howard Houghton III and Tabitha Hapl from Avalanche Excavating foresaw the challenges of hauling off the waste material to be processed. So, they set out to search the web for a solution and came across the MB crusher bucket through YouTube.
Houghton and Hapl were impressed by the machine crushing large piles of concrete and rocks. Soon, they contacted MB Crusher America to find out more about the product.
"A lot of people have never seen anything remotely similar to what this machine is capable of doing," Hapl said.
"Feasibly, we save money by not having to buy land to set up a crushing service when you can do it right on the job site."
With the BF90.3 crushing attachment, Houghton and Hapl could use the unit to crush the waste material on-site without having to transport it to a processing facility, solving their concerns with their 2015 project. The BF90.3 crushing attachment is a mid-sized MB jaw crusher designed for excavators weighing more than 46,300lb.
Houghton and Hapl purchased the BF90.3 crusher bucket for their Salida project, and then later used it to produce product that classified as Class 5 and Class 6 material.
"Our Class 5 product is straight from the spoils that we had tested through a certified lab and it came through our gradation and passed it with flying colours," Houghton said.
Hapl added: "The crusher bucket has also helped us with not having to buy Class 6 and Class 5 from an outside source and bringing it into our projects, so we don’t have to haul as much and we can stay on the job site. We are able to do everything right then and right there, and move it around and shuffle it to where we need it to be."
Once Avalanche Excavating began using the crusher bucket regularly, the company started to see an increase in savings, not only from creating its own Class 5 and Class 6 material.
"We have saved tremendously from our total trucking purchasing, our hauling, our overall expenses, our fuel, everything by at least 30% to 35%," Houghton said.
"We typically use the unit daily, anywhere from eight to ten hours. Weather doesn’t really shut us down."
The company has also begun to sell part of its Class 5 and Class 6 product as structural fill. Since its initial purchase of the BF90.3 crushing attachment, Avalanche Excavating has added a MB-S14 trommel screening attachment to its equipment line-up to further cut cost. Its MB-S14 screening attachment will screen the already crushed material to create more product the company is also selling.
The MB-S14 is one of MB’s screening models designed for excavators weighing between 19,900lb and 44,000lb. It is built with several different screening panels to accommodate the needs of the job or project.