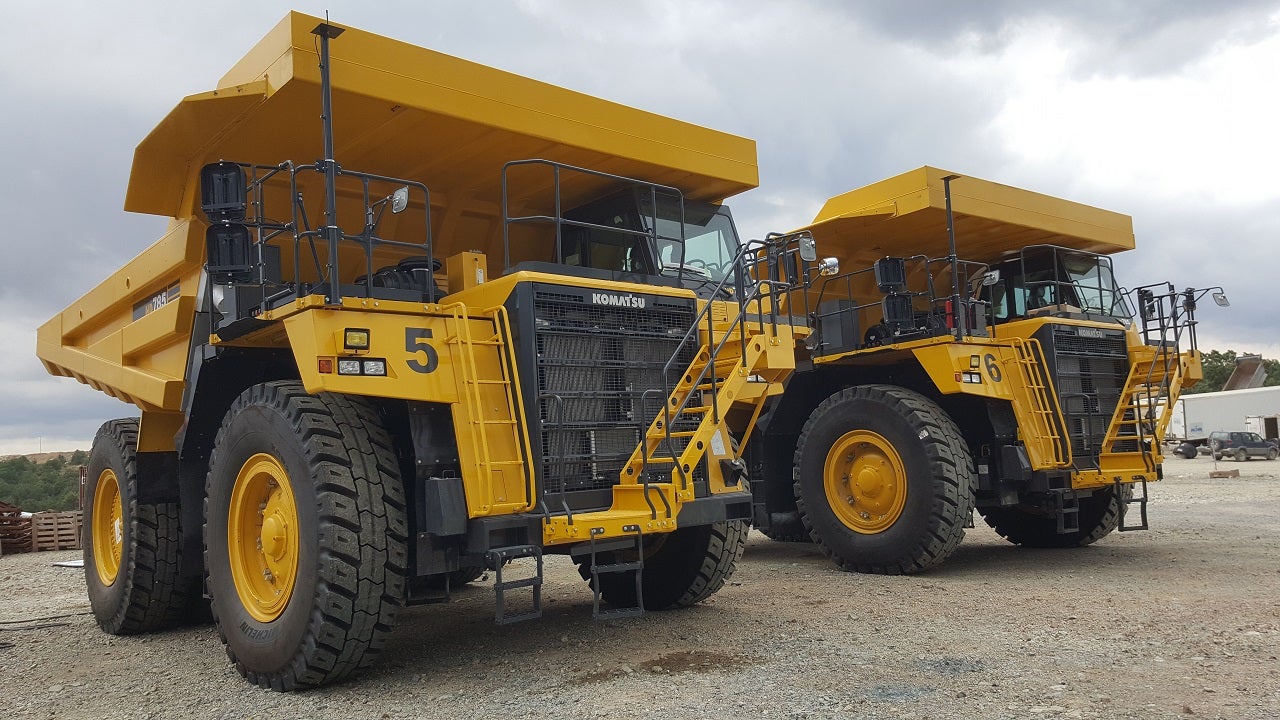
When a copper mine in eastern Europe needed to update their dump truck fleet, they chose SKF to deliver the automatic lubrication systems. In the face of challenging competition, it was the robust SKF solution, adapted to harsh conditions and specific customer needs, that was deemed best to meet the demands for uptime and reliability.
Updating the mining equipment, one machine at a time
The copper mine has been in service for a long time, and a large part of the equipment is over 40 years old. After the privatization of the mine, the new management has stipulated new requirements on profitability, efficiency and cost control, and is gradually replacing the old equipment to help meet those requirements. Since this particular mine has a rather low ore grade, the amount of extracted mineral makes haul trucking critical to ensure enough rock is moved to processing to extract the copper profitably. The mine management chose to purchase ten Komatsu HD 785-7 dumper trucks, and they wanted them to be equipped with automatic lubrication systems.
The right lubricant, in the right quantity, at the right time, to the right lubrication point
Centralized automatic lubrication systems are an effective way of increasing machine availability while reducing reliance on relubrication personnel and reducing the need for maintenance planning. These systems provide the appropriate lubrication quantity at the correct intervals, minimizing friction and wear and optimizing bearing and machinery service life.
Facts and figures
The mine
- Conventional open-pit copper and gold mine and flotation mill
- Produces premium flotation concentrate containing copper and gold
- Processes over 4.5 million tons of ore annually
- Over 40 000 tons of copper concentrate containing gold are produced each year
- Ore contains 0.2-0.3% of copper and 0.2-0.3 gram per ton (g/t) of gold
The dumper truck
- Komatsu rigid haul truck HD 785-7
- Engine power 1200 HP
- Max speed 65km/h
- Body capacity 60m³
- Rated payload 91 t
The lubrication solution
- Progressive system
- SKF KFGS5FX pump with 10l reservoir
- 3 pump elements
- Grease filter
- Minimum level sensor
- Internal control unit
- Operation monitored by proximity sensor
- Number of lubrication points: 35
A tailor-made aftermarket solution
In this case, the mining company found that an aftermarket solution would better meet their needs than lubrication systems delivered with the dumper trucks from the truck company. They issued a request for quotation to a select group of suppliers, and after a thorough evaluation, they chose SKF.
Meeting customer-specific needs
SKF and our partner Alfatek combined our experience, expertise and understanding for the customer’s business to provide a solution to the request. Our suggested solution consisted of a progressive lubrication system, including an SKF KFGS5FX pump with a 10l reservoir.
A grease filter was also included, which is not standard but recommended in this particular environment. There is always a risk of dirt entering the system, no matter how careful you are.
Three pumping elements were included, instead of one. Three pumping elements can give three times the amount of grease, which means that all points can be lubricated in a third of the time.
The vital parts of the lubrication system were installed in a special cabinet, to further protect them from dust and dirt, and falling and flying rocks.
Ready for continuous operation
With automatic lubrication systems from SKF, the copper mine now has a robust solution, adapted to harsh working conditions. The automatic lubrication systems enable round-the-clock operation of the dumper trucks while minimizing the risk of human error. The result is maximized uptime for one of the most critical assets of the mine.