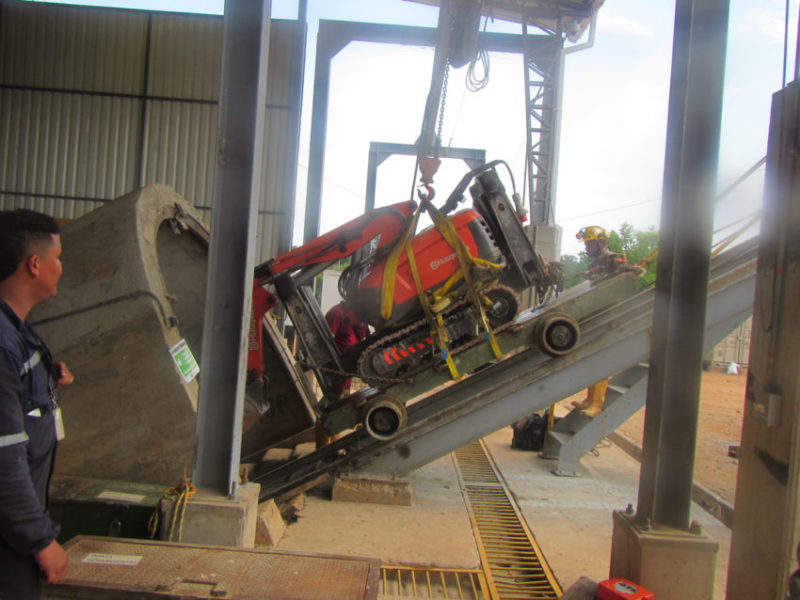
In a remote part of Colombia, surrounded by muddy waters and dense, humid jungle, there is an area full of tunnels into the Earth. These tunnels are owned by Operadora Minera and it is in these tunnels that 3.5t of gold are hauled out of a year. With the help of dynamite, rails and large 32in (W) × 96in (L) × 48in (H) carts, three men work to load 3t – 4t of blasted material by hand into the carts, normally two, a day. The blasted material is then processed further to find the gold hiding within.
The tunnels are created at a 35° angle. Working at a 35° angle in a hot, humid environment, lifting heavy rock takes a toll on the workers over time. Therefore, they work in shifts and are at the site for only three weeks at a time before heading home for a break. Campo Elías Gómez Merchán, Director General of Operadora Minera, and his team were looking for ways to increase worker safety, alleviate stress on workers’ bodies and increase the amount of material generated during a shift. After a lot of research into various solutions, they started looking at electric demolition robots.
Demolition robots can execute the manual digging and hauling tasks the workers were performing, thus moving the workers away from hazardous areas. The robot’s compact size enables it to be used in tight spaces, while its steel track helps the machine move over sharp rocks and withstand the hot, humid environment (rubber tracks would crack or could be cut).
The availability of different attachments enables the machine to switch between breaking loose rock from the sides of the tunnel walls and excavating the fallen rock. The electric-power does not produce harmful emissions, keeping workers safer. All these features help Operadora Minera accomplish their goals, but now the decision of what robot to choose.
Selecting a robot
Gómez Merchán reached out to Gonzalo Becerra co-owner of DiamantBec located in Bogotá, Colombia to try out a Husqvarna DXR 270 demolition robot. After putting the robot through a rigorous test in the mine to see if it could withstand high heat, swinging large loads of material that could stress a machine, as well as how well it maneuvered and ease-of-operation, Gómez Merchán and his team ultimately decided the Husqvarna DXR 270 demolition robot would be the robot for the job. It is powerful, agile, easy-to-operate and they were impressed by the level of service and support Husqvarna offered with the machine. After the robot was sent, Johan Ekström, Product Manager, Demolition Robots from Husqvarna Construction Products – Americas, followed. To reach the remote site, Ekström flew from the USA to Medellín, Colombia. From Medellín, he took a small plane to Caucasia, where he travelled 1.5 hours via car to El Bagre. From El Bagre a 20-minute boat ride on the Rio Bagre river to a docked, where he traveled another 20 minutes via car to finally reach the gold mining operation. Ekström came to help train the Operator Minera team.
Training takes teamwork and skills
Ekström does not speak Spanish and the Operadora Minera team only speaks Spanish. To help, Aleksandar Stankovic, District Manager at Husqvarna, and Mauricio Becerra Valbuena from DiamantBec, served as translators and additional trainers. After the training team taught the four operators basic operation and maintenance of the DXR 270, they then started to instruct them on how to perform the specific tasks the DXR would handle in the mine. This included using the bucket attachment to dig, pick up and unload the material in carts all at a 35° angle, as well as learning maneuvering and balancing the machine at different levels. To ensure the four operators were well trained, Gómez Merchán asked Ekström to develop a practice plan for them and to come back in 4–5 weeks to evaluate the operators.
When Ekström returned in March, along with Becerra Valbuena from Diamant Bec as translator, the four operators passed their practice plan evaluation and it was now time to apply their new skills in the mine. Ekström accompanied four men into the mine and fine-tuned the operator’s performance on their specific tasks. By the end of the training week, the DXR and agile operators were accomplishing in two hours what it took the three man team to manually load during a 12-hour shift. Needless to say, everyone was pleased with the result. The DXR is able to increase the mine’s efficiency as well as increase worker safety. A win-win!