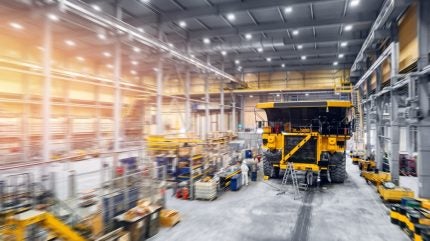
Mines operate in highly competitive and sometimes volatile environments where managing costs is crucial for maintaining profitability and long-term sustainability. One area that has a direct impact on operational expenses, productivity and overall efficiency, is prolonging the lifespan of mining equipment such as truck and excavator fleets.
Investing in predictive maintenance systems can play a crucial role in increasing the longevity of site equipment. This proactive method helps reduce downtime and extends the lifespan of mining machinery* by discovering issues early on before they become significant issues and cause a breakdown.
The adoption of advanced technologies, including automation and robotics, also plays a role in enhancing the longevity of mining equipment. Automated systems can operate continuously in challenging environments, which not only improves asset utilisation but can help lead to significant cost savings over time.
Advancements in lubricant technology are also extending machine life and cutting costs*. The selection of optimal lubricants leads to a substantial reduction in wear and tear on equipment. This not only lowers fuel costs, which typically account for about 25% of operational expenses[i], but enhances overall productivity, with less maintenance and fewer breakdowns as miners can maintain their equipment in better condition. This approach allows operators to choose the right products as well as integrate lubricant management into mining businesses’ overall operational plans.
Extending machinery life
Well maintained equipment leads to lower repair costs overall and extends the lifespan of machinery. By implementing predictive maintenance strategies, miners can monitor equipment conditions closely and identify potential failures before they occur, thus scheduling maintenance proactively. This approach minimises unexpected downtime and reduces costs associated with unscheduled repairs and forced reallocation of resources. By improving maintenance schedules and practices, companies can also increase machine utilisation. Equipment can operate more often and generate more output, which effectively lowers the production cost per ton*.
The mining sector is also seeing more efficient use of equipment due to the rise of tele-remote and autonomous vehicles. According to a recent report by GlobalData, the robotics industry will be worth US$218bn by 2030[ii], as automation offers increased mine productivity for processes such as hauling, drilling, blasting and exploration.
Automated mining equipment, equipped with advanced sensors and software, can navigate flooded passages autonomously, withstand extreme weather or dust, monitor performance, detect potential issues and prevent accidents. With 1,145 autonomous vehicles reported in operation in mines in May 2024[iii], these trucks optimise routes, reduce fuel consumption, increase productivity and reduce accident risks.
The report notes that robotic technology can surpass human capabilities in performing tasks with precision, which results in increased efficiency, reduced waste across mining operations and less accidental equipment damage. Additionally, robotic maintenance machines can help with repair issues and less downtime. For instance, an idler on a belt can be changed without the conveyor belt needing to be stopped.
The importance of lubricants
Whether operated by a human or autonomously, miners rely on lubrication to keep a mine’s machinery working smoothly and effectively.
Using recommendations based on equipment requirements is a strategic approach that can help lead to significant cost savings for miners*. This practice revolves around selecting the correct lubricants tailored to the specific needs of their mining equipment. The right lubricants can help enhance the efficiency of mining equipment while efficient lubrication minimises friction and wear, leading to better fuel consumption and extended equipment life.
Solutions from Mobil™
Mining operators worldwide rely on Mobil’s™ comprehensive portfolio of world-class lubricants and robust services to achieve and sustain success in the face of fluctuating commodity prices, market forces and increasing shareholder expectations. Long-lasting, advanced-technology Mobil™ lubricants are designed to help ensure the reliability of equipment and lower maintenance costs*, while also helping minimise maintenance.
Mobil’s™ synthetic lubricants and services aim to improve productivity, protecting mining equipment and providing trouble-free performance, helping to reduce equipment breakdowns and maintenance costs.
To discover how your mine operations can benefit from expert lubrication solutions, download the free paper below.
[i] https://www.mining-technology.com/features/fuels-lubricants-navigating-emissions-reductions-in-off-highway-mining-fleets/
[ii] GlobalData: Robotics in Mining, March 2024.
[iii] GlobalData: Development of tele-remote and autonomous equipment in the global underground mining sector, May 2024
* Results are based on the experience of a single customer. Actual results can vary depending upon the type of equipment used and its maintenance, operating conditions and environment, and any prior lubricant used.