
No matter what you mine, you have a lot on your plate. You need to maximize equipment availability, reduce fuel costs, find ways to reduce your cost per ton and more!
While you may use different tools to achieve these goals, one thing that can make a huge impact all around is an efficient maintenance strategy.
But, building that maintenance strategy isn’t easy. With many different pieces of equipment – often made by different manufacturers with their own operating requirements – and with the increasing complexity of today’s integrated mines, it might even seem impossible.
Our Mobil mining experts and thought leaders have decades of experience helping mines address all types of maintenance challenges. And since we have our own mining operation at the Kearl Oil Sands project in Alberta, Canada – we know what it takes to keep a mine running.
To help address these commonly faced maintenance challenges, we’ve pulled together three best practices you should consider when building a best-in-class strategy.
1. Maximize truck availability while preserving warranties
When every minute of uptime is critical, it can be difficult to assess the optimal service interval for your equipment – one that’s not too cautious nor too risky. For many mines, there is opportunity to extend them or reduce the time in shop to get more productivity from your equipment without sacrificing reliability.
You need to work with OEMs, your lube supplier, to design an optimal service schedule and program. These relationships can help your technicians meet service requirements without violating warranty requirements – a critical safeguard. As a result, you’ll drive higher availability and lower your mine’s cost per ton.
In one instance, selecting the right lubricant for Kearl Oil Sands’ saved more than US $1.6 million by safely extending the oil drain intervals of its hydraulic equipment by six times the OEM-recommended limit.*
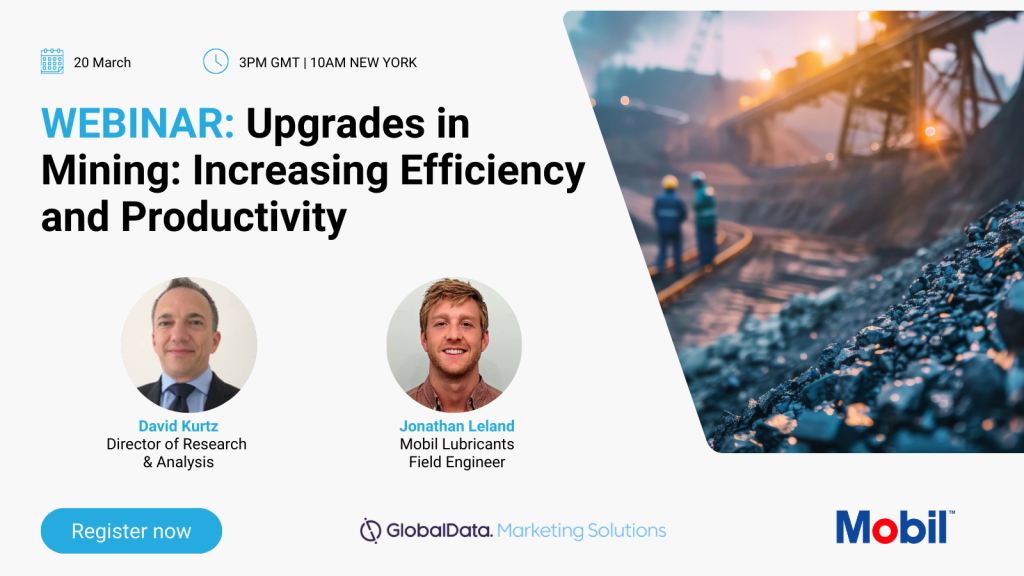
Disclaimer: * This Proof of Performance is based on the experience of a single customer. Actual results can vary depending upon the type of equipment used and its maintenance, operating conditions and environment, and any prior lubricant used.
2. Ensure your team is working as efficiently as possible, regardless of experience level
Due to frequent personnel changeover associated with mining operations, the loss of information among personnel can often lead to loss of tribal knowledge create a scarcity of knowledge among the new, young talent. Unfortunately, this means that maintenance teams are often challenged.
As experts in mining equipment and maintenance, lubricant suppliers effectively help mines overcome this challenge by providing more advanced products that require less frequent maintenance. Furthermore, lubricant suppliers can help train staff in accomplishing everyday tasks, helping them better understand how an effective lubrication and maintenance program should look.
3. Digitize your maintenance program
Mining personnel are no strangers to digitization, given that many sites have already integrated new digital technologies to monitor critical equipment performance and boost productivity. However, to truly benefit from digitization, it is important to focus on the human factor as well.