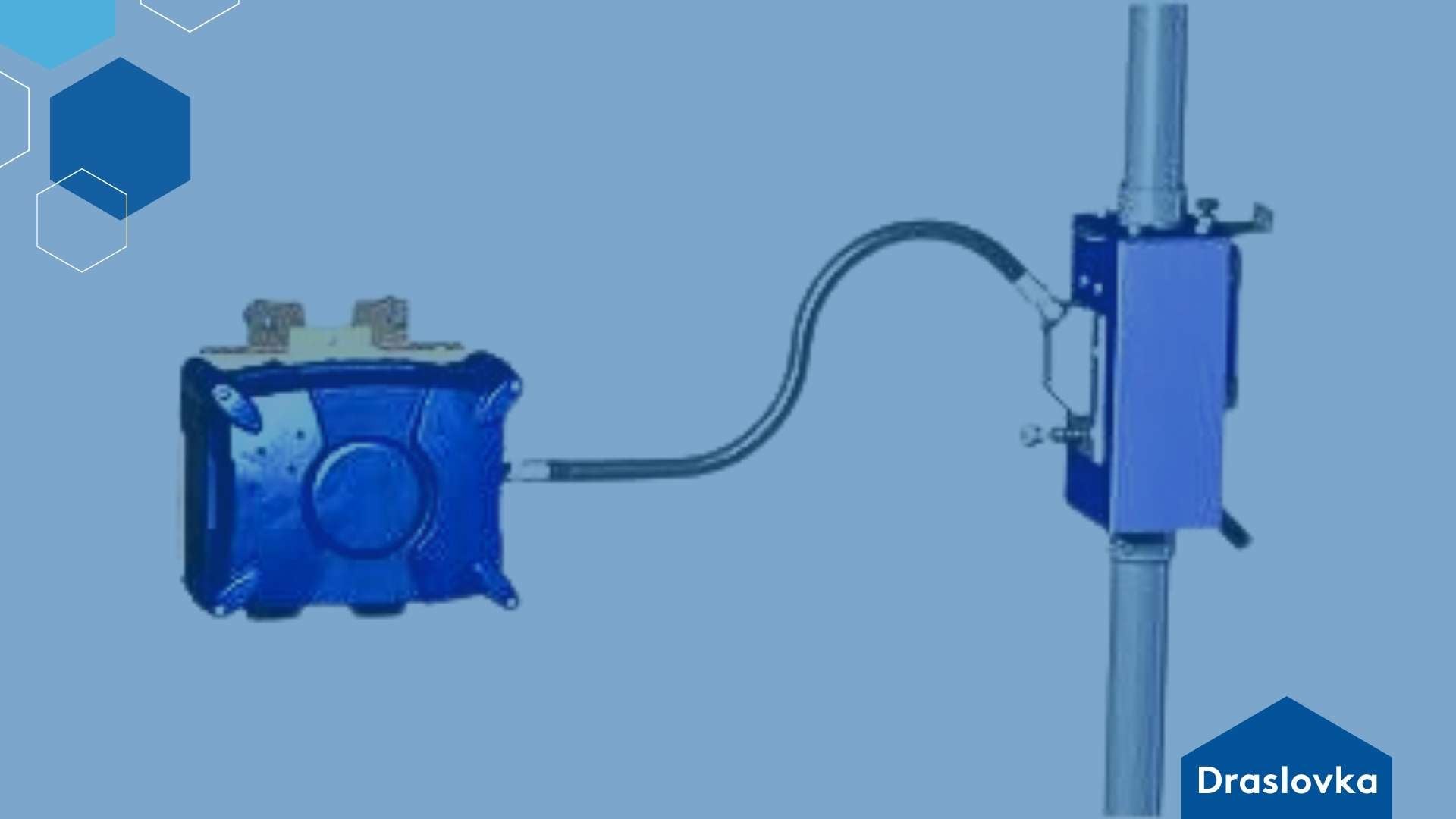
The Blue Cube Dry Analyzer provides multiple measurements with a single instrument. These measurements include elemental, mineral, and particle size (site dependent), but can also be used to model other lab analyzes such as total heavy minerals. State-of-the-art spectroscopy and mathematical modelling are used to provide these real-time measurements to enable process control.
This analyzer is used for the in-line measurement of dry free flowing ore streams with grain sizes below 2mm. The analyzer was specifically developed for the mineral sands industry, however it can be adapted to other applications.
Benefits
- The non-contact measurement approach results in a low maintenance
- Collection of data from a broad light spectrum combined with state-of-the-art data-science techniques provides the capability to identify and adjust measurements over the lifetime of the analyzer to suit changing process needs.
- Modular design enables simple installation with minimal investment in new infrastructure.
Features
Measure:
- The scanner head is designed to receive a free-flowing ore stream vertically downwards.
- Mineral grade, elemental grade and particle size are measured in-line and in real-time.
- BlueCube Dry Analyzers are suitable for installation in any plant environment and in process lines of any diameter.
Control:
- Data made available by an installed BlueCube Dry Analyzer on a high tension roll (HTR) separator is an example of real-time control in the mineral sands industry.
- Through the manipulation of the corona wire high voltage settings, it is possible to control the product grade in real-time.
Optimize:
- With the availability of the real-time data, it is possible to track the effect of process changes on the grade without full plant surveys.
- Product grade can be optimized and impurities minimized, all in real-time.
How It Works
Our state-of-the-art mineral analyzers use advanced mathematical modelling combined with Diffuse Reflectance Spectroscopy (DRS) techniques to provide real-time measurements that enable process control and optimization. DRS uses a broad band of light, from ultraviolet, through visible and into near-infra-red to determine mineral and elemental composition based on the spectra reflected from particles in the slurry.
Our optical technology can be applied to any quantifiable property that affects the spectra in this broad range of light. Compared to XRF, DRS covers a much broader range of electromagnetic frequencies and therefore can measure a much broader range of elements and minerals. It also requires shorter integration periods for detection.
- Light is directed through a sapphire window onto the ore stream as it passes through the pipe and the light reflected by the stream particles captured. The reflected light is digitized and used together with a calibration model to extract spectral features of interest and provide 15-second updates to the measured parameters.
- The BlueCube Dry Analyzer monitors the process and automatically extracts one calibration sample per day when process conditions are appropriate using the integrated pneumatic sampler.
- The spectra captured while the calibration sample is drawn are recorded and uploaded to an off-site data centre via the cloud. The laboratory assays of the calibration samples (emailed to Draslovka weekly), are used together with the uploaded spectra to monitor performance and fine-tune the calibration model.
- The refined calibration model is automatically downloaded to the instrument to ensure accuracy is maintained through drifts in process conditions and lithology. This process is repeated on an ongoing basis, with new samples used to improve or adjust the model, and to report on the accuracy of the analyzer.
Maintenance Requirements
▪ Light Source replacement every 9 months.
▪ Inspection of Scan Head every 3-6 months (until actual wear rate is established).