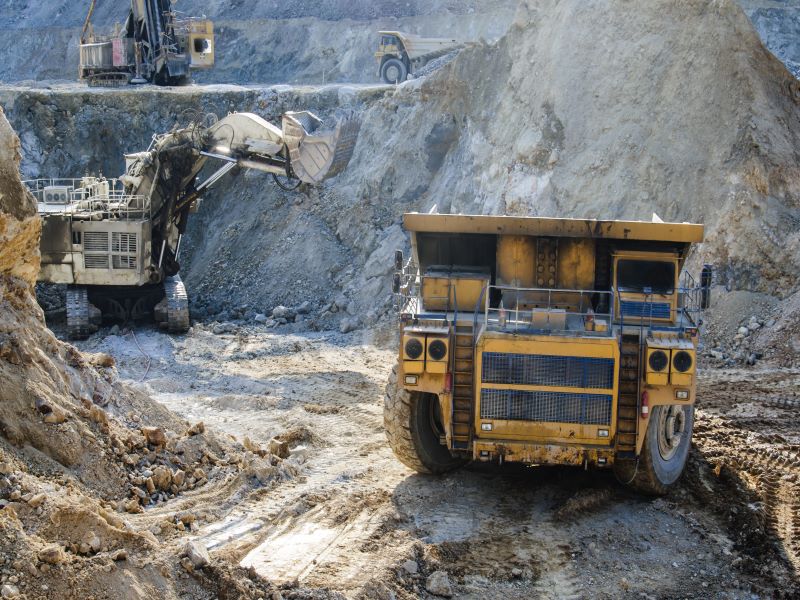
The mining industry is starting to benefit from a new generation of low emission “driverless” mine vehicles that are transforming the image of the industry and heading towards decarbonisation. Electric vehicles (EVs), for use in both open pit and underground operations, are added to fleets either through purchase or by the retrofit of existing diesel engine vehicle fleets. GlobalData, the parent company of MINE, believes that electrification is advancing in underground projects faster than open pits, but that both will become a focus in the 2030s.
Turning electric: 1 million mining EVs by 2030
Companies like Toyota Motor Corp are at the forefront of developing these new mine vehicles. In May 2023, Toyota and Komatsu announced the launch of a joint project to develop an autonomous light vehicle (ALV) that will run on Komatsu’s GPS enabled Autonomous Haulage System (AHS). The joint project seeks to alleviate one of the main drawbacks of AHS-enabled autonomous haul trucks when they work alongside manual light vehicles. Currently, there is a serious risk of collision when both types of trucks run on haulage roads at the same time. But by introducing a common AHS system for both ALVs and heavy-duty vehicles, Komatsu and Toyota hope their collaboration will reduce the risk of collision, increase mine worker safety and improve site productivity. A concept ALV is already being tested at proving grounds and a proof of concept is expected to be rolled out at a customer site by approximately January 2024.
In Ireland, decarbonisation systems company Cool Planet Group has signed a €50m deal with a “leading global mining company” to retrofit 8,500 diesel mining trucks into electric vehicles over the next three years. This retrofit, though, could be just the tip of the iceberg.
Crowley told the Irish Times: “As many as 1 million diesel mining vehicles will need to be retrofitted to electric by 2030. We’re working with five or six of the largest mining companies in the world and we’ve developed a bunch of vehicles that are electric, don’t emit diesel particulate matter, but also they are much safer. They have collision avoidance systems so they can’t run people over.”
Autonomous mine trucks make inroads
Currently, Australia leads the way in having the largest number of autonomous mining trucks in the world. But a global race is underway, with dozens of tech companies worldwide aiming to bring this technology to a wider market.
In the US, commercial autonomous vehicles company RRAI aims to integrate its technology into heavy duty Class 8 trucks that provide haulage for a variety of materials in and around mining operations. RR’s approach is to be “vehicle agnostic”, making “kits” suitable for companies with a mixed fleet of vehicles.
Meanwhile, Swedish miner ABB and British environmental technology company First Mode have announced a purchase order for ABB to supply First Mode with 80 lithium-ion battery systems totalling 2.6MWh. The batteries will be assembled into larger battery packs and used in the construction of hybrid hydrogen and battery “power plants” to power ultra-class haul trucks.
“The mining environment presents a unique combination of high-power charge and discharge, continuous operation, and significant thermal management challenges that are not found in many other applications,” Krunal Desai, First Mode’s director of electrical engineering explained on the company website. “Lithium titanate oxide-based cells are an ideal fit for this application, with excellent power performance and inherent safety that meets our operational needs,” he added.
New electric mine haul trucks rolled out
Elsewhere, the Oxfordshire-based automotive technology firm WAE Technologies is developing what it describes as “the largest battery it has ever produced.”
The battery is designed for use in a zero-emission electric mining haul truck. The company, now owned by the Australian mining giant Fortescue Metals Group, is working alongside Liebherr, the Swiss-German equipment manufacturer, to develop a fully electric mine haul truck weighing up to 240-tonnes. The battery is expected to be an important part of the Australian firm’s $6.2bn decarbonisation strategy by swapping its fleet of diesel trucks with battery or hydrogen powered machines at its iron ore mining operations.
Fortescue CEO Elizabeth Gaines added: “With around a quarter of our [Scope 1 and 2] emissions attributed to our mobile haul fleet, this represents a significant opportunity to drive our pathway to being diesel-free.”
In January, WAE Technologies completed and delivered the battery that is now ready to be installed in the prototype electric truck. Managing director Craig Wilson said: “This high-performance power system not only boasts the highest energy storage of its kind, but will also be the first to offer 30 minute fast charging.”
Meanwhile, industrial vehicles giant Caterpillar recently unveiled its own fully electric mine truck, the 793 prototype. The firm claims that the new electric machine achieved a top speed of 37.3mph, when fully loaded. The battery-powered mine truck is being tested at Caterpillar’s Arizona proving ground, which is being transformed into a test bed for a sustainable ‘mine of the future’. While some electric designs differ significantly from their predecessors, the machine is effectively an electric version of Caterpillar’s existing diesel powered 793F mine truck.
Canada providing tax credits for “clean” mine vehicles
In Canada, the decarbonisation of mining and construction vehicles is already well underway. From spring this year, the mining and construction industries will receive a boost for transitioning to zero-emission heavy-duty vehicles through a new tax credit from the federal government. The 30% refundable tax credit will apply to both hydrogen and electric heavy duty equipment used in those industries, as well as charging and refuelling infrastructure. However, the credits will only give short-term relief, as the government will phase them out from 2032 and end their availability from 2035.
Stephen Gravel, manager of the Centre for Smart Mining at Cambrian College in Sudbury, Ontario, told Electric Autonomy Canada: “Electric versions of traditional underground mining equipment can be significantly more expensive than their diesel counterparts. The upfront capital investment for ditching diesel can make adopting the greener vehicles out of reach for some companies. I think this tax credit will work to enable more mining companies to adopt electric equipment. It may also accelerate the rollout of electric vehicles at mine sites that have already started to make this transition.”
Aside from the environmental benefits, electric haulage vehicles provide readily apparent advantages to miners, eliminating particulate emissions and noxious fumes. This has helped drive the electrification of fleets, and soon the electrification of smaller sites seems like an inevitability.