
Metals production is integral to achieving a low-carbon future, with renewable infrastructure and technologies relying on a myriad of these materials, including steel, aluminium, and lithium. Yet while they may be a necessary part of a clean future, current production processes are far from carbon free, being responsible for around 9% of global emissions – a more significant figure than all the cars on the road combined. Cutting emissions in this sector is a clear necessity and steel, used in everything from transport to infrastructure to communications, represents a major market for change.
While estimates vary on predicted future demand, steel’s annual growth rate could be between 1.4% and 3.3%, resulting in a projected demand as high as 2.4 billion tonnes by 2025. Given this scope, making changes to how the metal is sourced is a must, and decarbonising these processes is a fast growing priority as stakeholders and members of the public alike push harder for effective carbon strategies. With its abundant renewable energy industry and high quality iron ore deposits, Australia is placed in a prime position to lead the charge, and strides are already being made to capture the green steel market.
How well do you really know your competitors?
Access the most comprehensive Company Profiles on the market, powered by GlobalData. Save hours of research. Gain competitive edge.
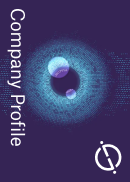
Thank you!
Your download email will arrive shortly
Not ready to buy yet? Download a free sample
We are confident about the unique quality of our Company Profiles. However, we want you to make the most beneficial decision for your business, so we offer a free sample that you can download by submitting the below form
By GlobalDataA market ripe for the taking
Australia is currently the largest exporter of iron ore, with the Australian National University (ANU) finding that the country’s exports account for roughly half of the global iron ore trade. Yet despite its prolific production, Australia rarely uses the raw material to create steel – a situation that has only recently been flagged as problematic as the iron market faces a squeeze, from global calls for emission reductions to rumours that China will be halting imports of Australian ore.
“Our main trading partners for iron ore (China, Japan, and Korea) have all established net-zero emissions deadlines of either 2050 or 2060,” says Dr John Pye, a senior lecturer from ANU. “Some of our biggest iron and steel companies in Australia have done the same, [including] Rio Tinto and Liberty GFG. This means that Australian exports of thermal and metallurgical coal (as well as natural gas), all have a ‘use-by’ date on them.”
“We need to start looking at other exports that can produce revenues for Australia competitively on the global stage, at a scale similar to what we currently do with coal and gas,” he adds.
Gaining a monopoly on the steel industry would prove a new (and very promising) window of opportunity, using the already abundant iron ore to create the increasingly popular steel.
“The biggest value to Australia is upgrading our currently low-value exports into higher value products,” says Professor Gus Nathan, director at the University of Adelaide’s Centre for Energy Technology. “These will become more in demand as a green product as the world decarbonizes.”
So, how do we decarbonise the steelmaking process?
The role of hydrogen
According to Nathan, hydrogen-based reduction of iron-ore is the ‘most logical pathway’ moving forward, and indeed this solution has been seen as something of a holy grail for carbon-free technologies for several decades. Yet the technology is not yet economically viable, and due to its novelty, the industry is somewhat unreliable.
“This is a classic case where what you’re trying to do is build supply at the same time as demand. And it’s not easy to do,” says Tony Wood, Energy Program Director at the Grattan Institute. “The demand for green steel is going to come from either businesses that are prepared to pay a premium for green steel or governments that are going to put some form of carbon price or carbon constraint on emissions from steel in the long run.”
Finding a way to kick the hydrogen industry into gear is crucial and a number of initiatives are already underway in Australia to pursue this alternative, harnessing electrolysis from renewable energy to produce hydrogen. Progress in the field is also being seen elsewhere, with the Swedish consortium Hybrit using hydrogen to replace metallurgical coal in the creation of zero-carbon steel. Despite its challenges, optimism seems solid for Australia’s potential to follow Sweden’s lead and crack this industry.
“We’ve done the economic analysis as to what we need to do next. The government has a technology investment development roadmap, and has set stretch targets for the cost of green steel,” Wood says. “Things are starting to move. There are a number of Australian cities and regions that are really excited about the possibility of being one of the hydrogen hubs.”
While important, hydrogen is only one area of opportunity, and alternative routes also need to be pursued if a stable sector is to be achieved.
“I think what we would say is that hydrogen will probably play the biggest role in future high-temperature industrial processes, but it will be part of a more diverse mix. It will not be a single solution,” says Nathan.
Harnessing renewable power
Speaking with Pye, he says deploying local iron ore production plants in the Pilbara could be an effective avenue to break into this industry.
“I believe that if the world is moving to decarbonise all industry, electricity, transport and buildings, then Australia will find itself in quite a competitive position at least to produce reduced iron ore,” he says. “For example, in the form of ‘hot briquetted iron’, which could be shipped overseas for the final (and more labour intensive) stages of production.”
Integrating renewables and carbon capture technology into the current processes is also a major area of opportunity. Implementing a mixture of solutions into the supply chain could also mean that while not every step is itself zero carbon, the net emissions from the entire process could be.
“We’re looking at the industrial ecosystem needed to achieve net carbon neutral across the sector,” says Nathan. “While some individual processes may not be carbon neutral – these would be balanced by others that are carbon negative. Some CO2 capture and re-use is also likely, which could get converted into something like ethanol for the plastics industry.”
However it’s achieved, adapting the current supply chain model is widely acknowledged as inevitable for Australia, adding a longevity and strategic advantage to the industry that has been recently destabilised. Initiatives have also been made to allow the implementation of this transition, with the ANU and University of Adelaide collaborating to establish a new Cooperative Research Centre to identify and address potential issues.
“There are challenges,” says Wood. “But they’re not insurmountable conceptually. Whether or not we have the capacity to turn the opportunities into commercial successes will depend upon a degree of coordination, cooperation, and leadership between industry and government.”
Indeed, while industry drive and government action seems to be aligned in pursuing this blossoming sector, exactly how this opportunity will be seized remains to be seen.