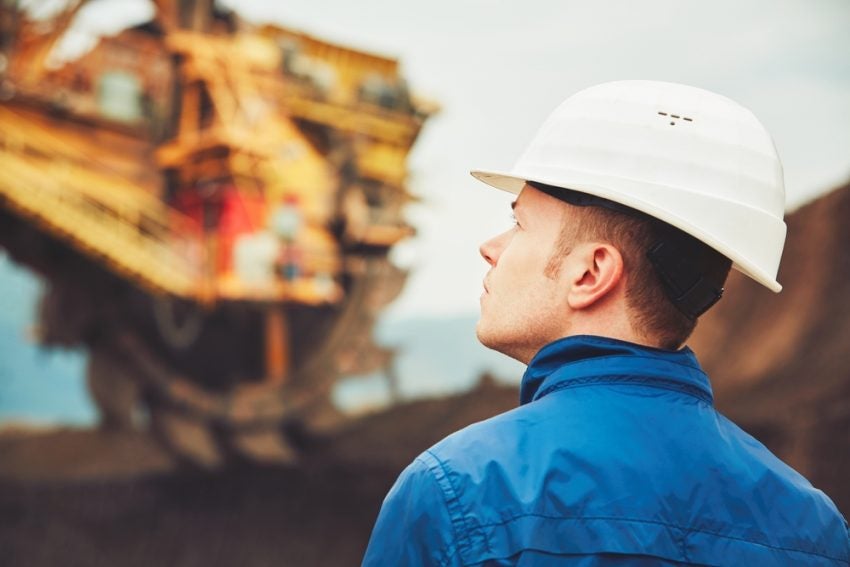
Mining Technology spoke with John Leadbetter, managing director at leading process instrumentation manufacturer Vega, about the true cost of an unplanned or extended mine shutdown and how they can be avoided.
Why do mines run planned shutdowns and how often do these happen?
John Leadbetter: Operators must schedule in shutdowns so that they can conduct proper maintenance and replacement programmes. A shutdown can last as little as three days or can as much as two weeks. Unless there’s been an absolute disaster, these planned maintenance shutdowns are an intentional action to carry out essential repairs.
Depending on the mine site, some may have a shutdown once every eight to 12 weeks but that’s really up to the operation itself. If you look at iron ore mining for instance, the average mine probably processes around 6,000 tons of processing per hour.
This results in a significant amount of wear and tear on the materials so they would probably have a closer shutdown schedule than a gold mine, for example, which will typically have less wear and tear and a different types of processing.
So the type of mine and the type of material that they mine are important factors but a lot of it comes down to whether the operator has adequate equipment.
What is the financial impact of a mine shutdown?
JL: During planned maintenance, operators tend to run the mine at full capacity during normal operation so that they have buffer material to ship during the shutdown. In other words, the mine doesn’t close completely as they are still shipping goods out.
The consequence is that if they have planned a shutdown for three days and they run over time, it starts costing a lot of money for the mine because they have lost production and they will run out of buffer materials to ship.
These unforeseen events could be due to a number of different factors, for example, the goods that were due to be replaced didn’t turn up in time from the supplier, or there could be a weather impact – after all, a lot of these mines in Australia are in cyclone zones.
Are there any other repercussions, for example reputational damage or a broader industry impact?
JL: Looking at coal and iron ore in particular, these mines have contracts with companies that they have to meet; if your shutdown is extended and you’re not shipping tonnage to your customers, operators are then breaching these contracts. This could also affect the operator’s reputation in the market place, particularly when mining operations are all in direct competition with one another.
But if you conduct proper maintenance and run your equipment efficiently, the chances of something going wrong are significantly reduced.
The big thing in the last ten years has been work health and safety. With these changes in workplace regulations, mining companies have an obligation or a mandate to ensure that all personnel are working safely and that equipment is not going to cause problems. By conducting regular maintenance or even by installing the latest in technology, safety improvements can be made.
How can mines avoid unplanned or extended shutdowns?
JL: What it really comes down to is better work practices. In other words, don’t push machinery to its limit; operate it as per the manufacturer’s recommendations.
For example, we were approached by a mining company a number of years ago because they found that their production wasn’t meeting the required tonnage per hour. They looked at a certain part of their operation and found that the equipment they were using at that stage was probably not performing to the best of its abilities.
A plan was formulated between the engineers and the suppliers of the equipment which looked at whether the performance of the current machinery could be improved or whether a replacement could perform better.
By Vega offering them an upgraded model in radar level control which gave an improved performance, along with other changes that were made, the operator experienced a 31% increase in production. That was a significant improvement for this particular provider, but any small percentage increase can have a massive impact on an operator’s bottom line.
How does investing in quality equipment help to safeguard against unplanned shutdowns?
JL: You can invest in the equipment and the technology but operators must also invest in training their personnel. Staff must be trained to work with the new equipment; if they don’t know how to operate it, it won’t be operated efficiently.
Over the last 15 years, Vega has offered clients the opportunity for us to come on-site and attend technical training courses. Those courses cover how the equipment works, how you can get it to work better in your operation, how to properly maintain it, and how to deal with something going wrong.
We have found that the companies that have attended our training courses will generally increase their turnover because they are more confident and trusting of the equipment.
Ultimately, suppliers of equipment now have a better understanding of their customer’s need and requirements, and they are working better together because of this.