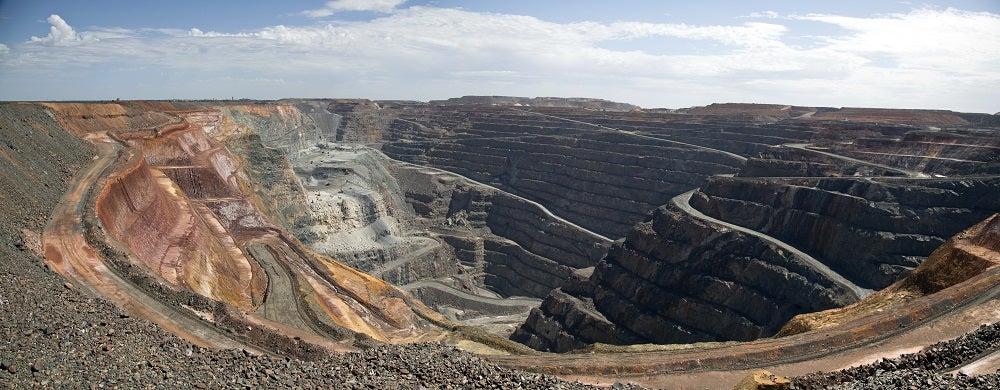
According to Mine magazine, technology is set to revolutionise the Australian mining sector. A report commissioned in 2019 by the Minerals Council of Australia (MCA) found that in the next five years, more than 77% of jobs in the country’s mining sector will be altered by technological innovations, increasing productivity by up to 23%.
To get there, Australia’s education and training system will require transformation, combining mining skills with “the latest scientific, technical and trade skills” such as data analytics, computing and change management.
Following stagnant productivity from 2009 to 2013 trends, in mining productivity have been positive with improvements largely the result of decreased capital expenditure (capex) and operational expenditure (opex). Increases in production in the Australian region are expected to remain at the forefront of new technology adoption (McKinsey & Company, 2020).
Technology adoption, particularly autonomous solutions alone, without consideration of end-to-end mining throughput, is at best challenging and at worst represents business failure. It seems obvious to consider the “whole of mining process” as an engineered system where all parts should be considered and prioritised before embarking on technology change, however that has not always been the case.
As a visible success story, the introduction of 80 driverless trucks in 2008 by Rio Tint’s Pilbara iron ore mine yielded massive increases in productivity. BHP Billiton and Suncor followed suit and the presence of Caterpillar, Sandvik, Komatsu and Atlas Copco continues to drive autonomous vehicle innovation, with additional semi-automated or automated equipment either planned or underway in minerals and coal mines across Australia, often supported by remote operations centres in or near capital cities.
In contrast, the introduction of any new technology, automated or semi-automated equipment or mining process has not always considered the full range of change required in management systems and organisational culture. Failure symptoms are often most visible:
- In equipment support through gaps in maintenance/repair skills/parts supply.
- Lack of suitable data, to support appropriate decision making, including having too much data leading to “paralysis by analysis.”
- Through personnel disengagement with newly introduced technology leading to poor safety outcomes, poor system performance or failure to achieve even basic production improvement aims.
Whilst blast hole drilling and off shore oil drilling have been successfully automated, other drilling types have not, although some underground rigs are progressing towards it. Land based exploration drilling rigs from some manufacturers have hands-free drill pipe/rod handling, but hands-free core barrel handling is mostly not available. Land production drilling rigs handle a wide variety of wellbore sizes and types, which has eluded automation to date. Oilfield rigs, particularly off shore rigs, have had either semi-automation or full automation for a decade or more due to high value of the wells and the resource.
Drilling is only one part in the onshore exploration value chain of locating, understanding and categorising a resource. The lack of technology in the drilling function is often not seen as an issue from a customer perspective, they’d rather concentrate on higher value functions such as core analysis or mineral grading technology.
Drilling for production, or the installation of dewatering, gas risers and the like is heavily influenced by installing the final casing and completing the wellbore which means that the actual drilling plays a smaller part in the process.
Directional drilling for resource definition or for gas drainage is the balance of power and finesse, and it relies on a solid geo-model for wellbore design and execution. Adoption of oilfield technology in the last three years has allowed integration of geological sensing tools with a greater depth of investigation into the drilling assembly, offering greater insight into geological model accuracy and supporting enhanced drilling decision making.
Drilling clients often search for improvements that push the boundaries of what’s possible, either for wellbore length, diameter or information required from the drilling process. Automation is often asked about, however it hasn’t been a high priority in final decision making when it comes to drilling. Rather, mine operators are focused on safety and technology change to deliver more applicable data from the drilling process.
AJ Lucas
Lucas has gained enormous experience since the drilling business began in 2000 and has been involved on the cutting edge of drilling developments for underground mining, directional drilling and production wells for water and gas. In the previous 22 years, Lucas developed an internal drilling engineering and directional drilling service to support the business and drive the uptake of engineered technology.
Lucas Drilling focuses on the combination of engineering expertise and appropriately changed technology to drive data driven decision making and positive outcomes for clients.
Engineering based technology improvements that have been adopted include:
- Rack and pinion rigs, first used in 2004, and since developed into high capacity PLC controlled rigs capable of drilling over 3000m. Normally used for extended reach lateral directional drilling the larger capacity rigs are used for gas drainage and support the deployment of the geological sensing tools to greater depths as part of a structured data collection plan to support better mineable horizon planning.
- Integration of drilling engineering software with real time rig data acquisition has evolved from planning drilling programs and leaving the field team to execute operations to a closed loop plan, drill, check, modify process with a head office drilling engineering team to support real time decision making on the rig.
- Off-site directional control, where applicable, has allowed a single directional drilling specialist to support multiple rigs, improving efficiency. Off-site operations are supported by the real time data acquisition and downhole drilling tool data streamed over a secure network developed in conjunction with the downhole tool provider.
- Integration of rig data acquisition and the improvement in downhole geo-sensing tool technology has facilitated geo-steering. Geo-steering is where real time sensing data is used by experienced personnel to actively interpret “as-drilled” geology, compare it to the modelled geology and make real time wellbore adjustments and maintain the well in the desired geological horizon. Geo-steering can be carried out either in the rig site or remotely if required.
- Development of large diameter threaded casing, in conjunction with a key supplier, to engineer boreholes to avoid on-site welding, significantly reduced installation time. Historically, a borehole has to remain open for long periods whilst the liner casing is installed and welded, increasing the risk of potential wellbore collapse and, in the case of an underground mine, increasing the volume of groundwater to be dealt with. Large diameter threaded casing connections reduce installation time from weeks to days.
- Large diameter casing packers that permit high quality casing cementing, especially on breakthrough holes, greatly reducing underground interaction and reducing completion timeframes. Historically, where wellbore liners breakthrough into underground workings the initial cement seal is installed from underground and a staged cement seal is installed from surface to complete the wellbore. Use of a larger diameter casing packer permits a single pass cement job to be pumped and completed in less time.
New technology will continue to be a combination of engineered solutions moving towards semi-automation and eventually full automation if the value add to the drilling process warrants it. The “trickle down” effect of other automation techniques and technology, particularly where mining operators are seeing demonstrated value, will provide the customer pull to balance the supplier push and should achieve a fit for purpose outcome.