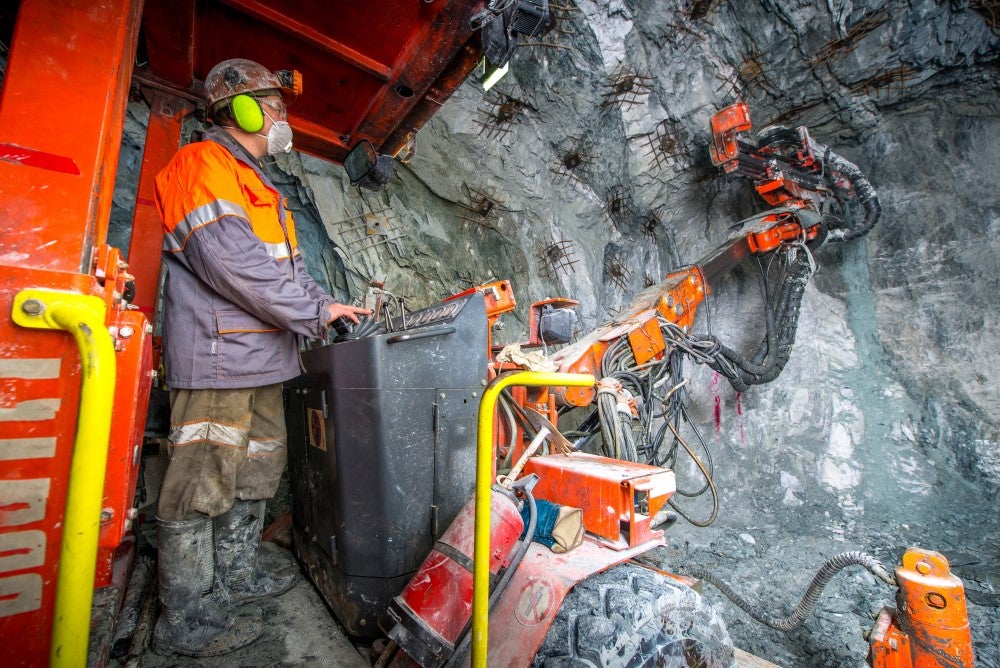
A recent analysis of AMC smart data reveals trends in Australian hard rock underground mining. Director of AMC Consultants Andrew Hall explains what the data reveals about the role of new technologies, including digitisation and automation, as well as the value of existing equipment.
Trends in key mining activities
The analysis considered key mining activities: jumbo underground mining development, long-hole drilling, load haul dumping and trucking. The top-line trends show:
- Jumbo advance rates have increased by around 40 percent over the last 20 years
- Long-hole drilling productivity has increased by around 20 percent
- Average loading rate has increased by around 15 percent.
These trends have been largely driven by introducing more powerful equipment, including improved mining drill bits, larger mining trucks and more powerful blasting equipment.
Data indicates room for improvement in the mining sector
“The key thing is that for all the key mining activities, mechanical availabilities and utilisation haven’t materially changed in over a decade,” Hall explains. “That’s unexpected, given the significant investment in digitalisation and automation, which should reduce operational delays, enabling better predictive maintenance and meaning we can respond to breakdown more quickly.”
What the data shows is that there is room for improvement.
Communication is key for underground hard rock mines
“The key issues for underground hard rock mines are around communication,” says Hall. “A lot of that stems from having good planning practices and communication with crews. That’s one of the huge opportunities for the underground hard rock mines today to cut into non-productive time.”
Why Australian long-haul operations are world’s most productive
Australian long-hole operations are, on average, the most productive in the world. This is down to the widespread adoption of mining methods and practices that are highly productive. For example, the average Australian operation uses jumbos to bore, scale and bolt, a practice that has significant productivity advantages in most mines.
Mining digitisation and automation provide huge potential
When it comes to new technologies, including digitisation and automation, the potential is enormous, and the prospects are exciting. Some of the areas where the impact can already be seen include teleremote loading, which boosts worker safety and improves connectivity and response. However, this technology is yet to deliver significant results regarding higher productivity across the board.
“There’s a big push on the use of automation and digitalisation, but it hasn’t made the returns that the industry should have expected,” says Hall. “Part of that is ensuring we’re selecting the right technologies for the right circumstances. Retrofitting those technologies into an existing mine is really challenging.”
Don’t dismiss existing mining equipment just yet
New technologies are never a silver bullet, and the mining industry is no exception. While emerging technologies, including digitisation and automation, have great promise to transform mining, starting with safety and connectivity, miners should ensure they implement them thoughtfully. The biggest efficiency gains may be found in using existing equipment to its best advantage.