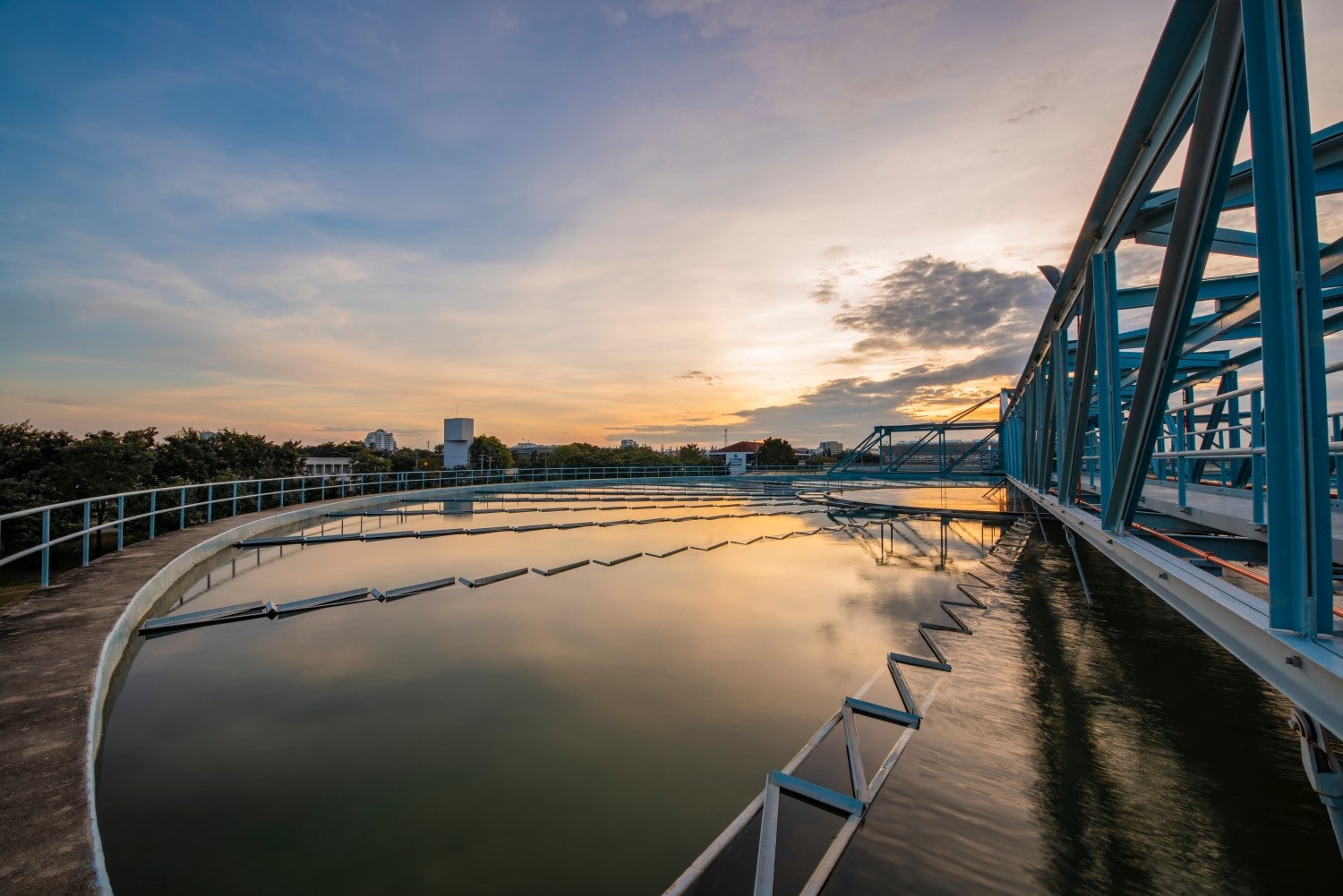
When components of wastewater systems corrode prematurely, the consequences can be costly. Operators may have to deal with unplanned stoppages, replace parts before the end of their reasonable lifespan, or pay to repair costly environmental damage caused by leaks and overflows.
Protective surface coatings for wastewater systems offer a cost-effective solution to premature corrosion by extending the life of components and reducing the risk of failure. However, the wide variety of components and materials used in wastewater management and the broad spectrum of surface treatments available have made choosing an appropriate product difficult.
A useful tool in determining what coating is needed is gaining a better understanding of common corrosion types in wastewater systems. By learning more about the various corrosion mechanisms and the forces involved, operators can select a surface coating that specifically addresses the challenges they face, greatly enhancing effectiveness.
Understanding corrosion types
Take the problem of pitting corrosion failures.
Pitting typically occurs on carbon steel and cast-iron alloys (say, within a thickener tank) when the natural oxide layer on the metallic surface is disturbed. This causes the exposed area to become anodic (i.e., to release electrons) while the covered areas remain cathodic. As the anodic region is likely to have a smaller surface area than the cathodic region, corrosion ‘pitting’ commences in the anodic region. As corrosion progresses the pitting deepens, and the pH levels continue to drop.
Understanding this mechanism can inform the decision-making process when it comes to choosing a long-lasting and effective surface coating. To be effective in an area prone to pitting, a coating will need to have high tensile adhesion to resist under-film corrosion and high abrasion resistance to resist losses by exposing regions that can become anodic. A suitable coating should have low permeability and be generally resistant to thermal and chemical exposure.
Similar conclusions can be drawn by examining problem areas such as graphitic corrosion (common in cast iron and ductile iron), galvanic corrosion, microbiologically influenced corrosion (MIC) in metal and concrete, and acid attack in concrete.
Choosing the right surface coating
The right protective surface coating can greatly extend the working life of components within wastewater systems. By understanding the types of corrosion that parts are prone to, operators can avoid using inappropriate products and zero in on the right coating for each application. Coating experts at leading sealing solutions provider Chesterton® can provide further advice based on individual circumstances and requirements.
Chesterton’s ARC range of coatings has a four-decade-long proven global track record of enhancing critical industrial equipment and structures. Their products are engineered to protect metal and concrete surfaces from the damaging effects of abrasion, erosion, and chemical attack.
Download the whitepaper below to understand the different types of corrosion experienced by metal and concrete in wastewater treatment environments and explore the KPI’s required by the surface treatments needed to address them. The research paper is based on Chesterton’s broad experience in the sector supplying ARC protective coatings.