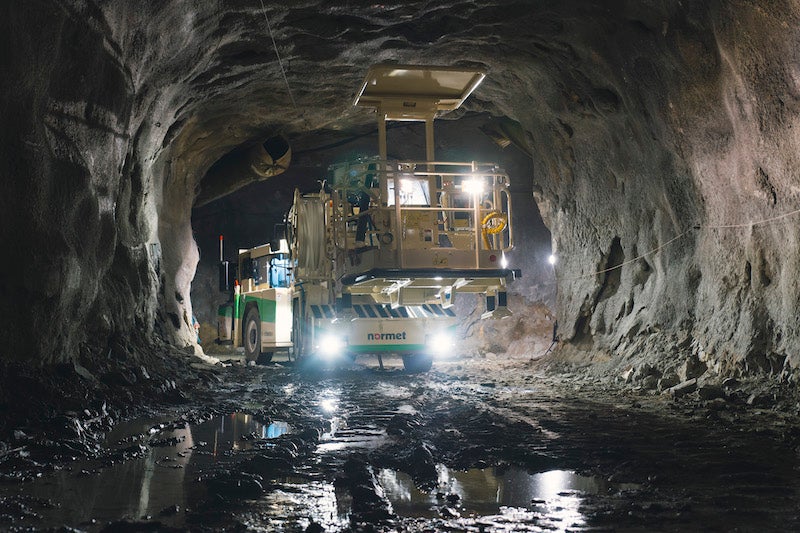
Before the invention of Tunnel Boring Machines (TBMs), drilling and blasting was the only cost-efficient way of creating long tunnels through harder rock types. Today it is often used in situations in which the use of TBMs wouldn’t make financial sense – as TBMs are often a costly technology – or in which they are unsuitable for ground conditions.
The process involves drilling several holes into the rock and filling them with explosives. The locations and size of these holes are carefully determined by mining engineers based on geological surveys, as well as the quantity of explosives. When detonated, these explosives cause the rock to collapse. Detonations are precisely patterned and timed to have the desired effect.
Blasting mats may be used to suppress sound and dust, prevent rock fly and to help direct and contain the dust. However, in underground mining, blast mats are not used as it is not necessary to suppress sound and rock can fly freely. As detonating explosives releases toxic gases, such as nitrogen oxide (NO), nitrogen dioxide (NO2) and carbon monoxide (CO), workers must wait until gas has dissipated and the area is ventilated before resuming work or seriously risk their lives and health. A portable gas monitor will help to ensure that the air is breathable before proceeding.
Once it is safe to do so, any remaining rubble is then removed and loose rock is scaled and the new tunnel reinforced to prevent any additional, unwanted collapse. This process is then repeated until the desired tunnel length is reached.
Explosives must be charged in order to detonate. All high production underground operations use modern site sensitised emulsions with original emulsion water gel now playing a relatively in minor role. Normet’s Charmec range is a series of emulsion trucks that have the capability to charge explosives to development and production holes once they have been driven to the blasting site.
Charging and blasting solutions for mines
While pumpable emulsions and other modern alternatives have almost entirely replaced outdated explosives such as nitro-glycerine (NG), ammonium nitrate fuel oil (ANFO) is still widely used in mining countries such as Australia, Russia and China. The use of emulsion has made blasting significantly safer than it was for the majority of the twentieth century due to their nature as a 5.1 oxidiser. They are safe to transport and handle underground until placed in the drill hole and charged.
Other advantages of underground emulsion charging over ANFO charging are a 20% to 25% total cost savings, 100 to 200% less power consumption of charging EQ at work face, and less nitrate emissions, meaning it is more environmentally friendly.
In order to optimise the benefits of using these materials, the charging process must be mechanised correctly. This means they must meet the productivity and quality requirements of the mining industry as well as being safe and reliable. Even perfect drilling can be made ineffectual if charging is poor-quality or done incorrectly.
The Charmec range from Normet was created with close cooperation from global bulk explosive manufacturers, as well as tunneling and mining customers. Authorities usually regard the units in which explosives are sensitised as explosive factories and therefore are required to meet stringent safety standards.
Traditionally, charging devices are diesel driven or hooked up to a mine’s electrical grid. With the Charmec MC 605 VE SD, Normet was the first company to bring out a commercially available battery-powered charging device. While much of Normet’s Charmec range applies the traditional electrical grid-powered system, battery-powered charging represents an improvement in safety, ease-of-use and energy and cost-efficiency.
Normet integrated emulsion charging technology into its SmartDrive battery-electric vehicle (BEV) range. The BEV range represents another positive development in the modern-day mining industry, with diesel vehicles falling out of favour as carbon emissions have become an increasing concern and businesses set zero-emissions targets.
All Charmec charging devices, whether diesel or battery-powered, come with extensive safety features. Their self-extinguishing marine type wire harnesses come with tinned wires and watertight conduits that are specially designed for safe and reliable operation in tough underground conditions. Necessary safety checks that must be done daily on these vehicles can also be performed above ground.