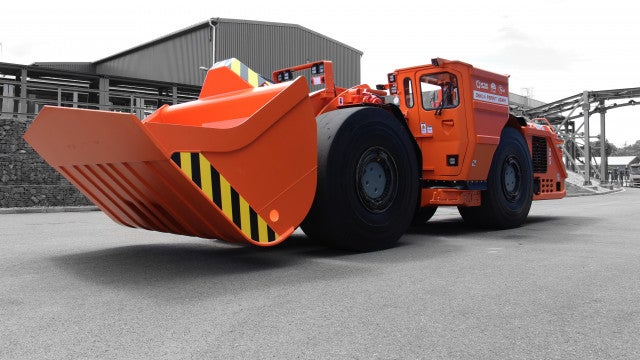
Mining LHD (Load, Haul, Dump) trucks are widely used to transport material to and from mines around the world. They are extremely robust and efficient in helping management streamline the critical movements of ore and debris from tunnels to the surface.
They are available with diesel- or electric-powered engines and can be manual or autonomous. Fossil-fuel LHDs are being replaced gradually by electric alternatives for the future, to increase compliance with global environmental, social, and governance (ESG) regulations and targets sooner.
They are usually narrow, low-profile vehicles that can navigate mine tunnels easily, carrying up to 20,000 kgs in one trip, and capable of repeatedly moving thousands of tons of material in one day. Some of them can be fairly long, to improve axial weight distribution and bucket capacity.
Ferrit LHD loaders
Ferrit has a range of world-leading LHD loader models. These are:
All these machines are designed to shift massive volumes of materials in and around underground mines efficiently and safely. Ferrit supplies them with a full support and after-sales service that is globally available 24/7/365.
Varying buckets are available, and their size and dimensions are determined by the transport route and how much material they need to carry. Flexible locomotion is ensured by a pair of axles, driven by Cardan shafts via a gearbox and a hydrodynamic torque converter, all driven by a powerful diesel combustion engine.
However, Ferrit is investing heavily in R&D to increase its range of electric-powered solutions, including all its wheeled and tracked mining material transportation range, to reduce the company’s own carbon footprint and improve worker safety, while helping customers meet ESG targets.
Common features across the range include:
- Bucket Vibration – allows for easier and more complete emptying of bucket loads
- Engine Brake and Lock Up System (locking hydrodynamic clutch) – extends brake service life by adding to braking efficiency when travelling downhill
- Downhill Driving Assistant – increases safety and shortens transport time by automatically ensuring required speeds are maintained on declines
- Autonomous Fire Extinguishing System – ensures further safety by automatically detecting excessive temperatures or fires in designated areas of the loader and activating an on-board fire extinguisher
- Elevated Battery – helps extend machine service life by preventing water from entering the battery that could damage it or the loader’s electrical system
- ROPS/FOPS Cab – has been designed and certified as a ROPS / FOPS protection structure for ensuring operator safety
- Kickdown – shortens work cycles by allowing faster Y-cycle execution during loading
- Automatic Lubrication System – increases loader service life by automatically lubricating key areas at selected intervals
- Measuring Bar – shortens service intervals by monitoring and displaying hydraulic pressure in different areas of the loader in one central location
Technical specifications for the DNK-10 include:
- Bucket capacity: 10 000 ±2 % kg
- Dimension (L-W-H): 9.76 x 2.58 x 2.42 m
- Inner turning radius: 3,285 mm
- Outer turning radius: 6,480 mm
- Weight (operating): 30,100 ±5 % kg
- Engine power: 239 kW
The DNK-14 and DNK-17 loaders have these features in addition to those of DNK-10:
- Hydraulic damping increases loader service life by automatically slowing down the steering, boom, and bucket just before the mechanical stop
- Immediate bucket discharge shortens working time without the use of a hydro generator, i.e. max. hydraulic fluid from the hydraulic cylinder flows into the tank
- Combined boom-bucket functions shorten work time by allowing for simultaneous operation
- Three modes of boom and bucket speeds (slow, medium, fast) are advantageous for beginners and during operator training
- Saving basic bucket-boom position pre-sets shortens working and transport time, e.g. transport position, max. lift of the boom (bucket) with respect to the profile, etc.
- Angle sensors determine the position of the boom, arm, and machine rotation.
- Bucket weight sensor instantly calculates weight, weight for a given interval, and totals
- Active Damping shortens transport time by actively damping the bucket and boom, thereby preventing machine vibration
- Fan Drive extends service life by regulating motor cooling (fan speed) based on temperature
- Automatic Brake Release System for releasing the loader using a towing hook when towing from a hazardous area
Technical specifications for the DNK-14 include:
- Bucket capacity: 14 000 ±2 % kg
- Dimension (L-W-H): 10,47 x 2, 96 x 2,6 m
- Inner turning radius: 3 140 mm
- Outer turning radius: 6 860 mm
- Weight (operating): 39 920 ±5 % kg
- Engine power: 280 kW
Technical specifications for the DNK-17 include:
- Bucket capacity: 17 000 ±2 % kg
- Dimension (L-W-H): 11,1 x 3,15 x 2,85 m
- Inner turning radius: 3 550 mm
- Outer turning radius: 7 350 mm
- Weight (operating): 48 000 ±5 % kg
- Engine power: 298 kW
Optional equipment available across all DNK models include:
- Enclosed cab design
- Air conditioning and heating
- Radio with USB
- Onboard Hydraulic Tank Filling Pump (24v) powered directly by the loader
- “MUR-T” Mobile Registration Device for registering machines/workers in the positioning system
- Remote control with image transmission
- Radiator-stop for pausing radiator fans on demand to prevent damage, e.g. in sections with excessive amounts of water, etc.
- Camera system
- Autonomous machine control system-ready
Further details:
For more details and sales information, please visit Ferrit’s LHD loaders page.