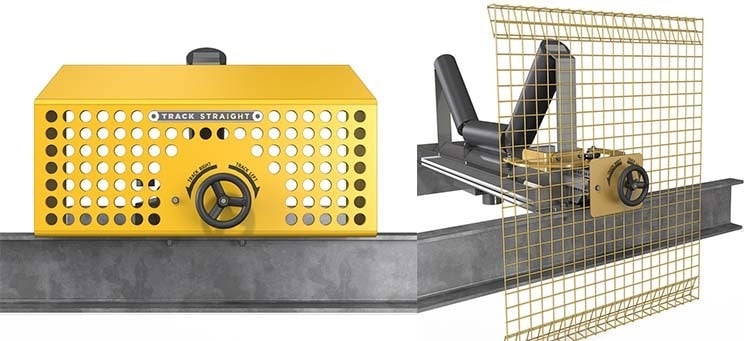
Question. What happens when a conveyor belt running 6,000 tonnes of iron ore every hour suffers from alignment issues? The answer potential damage, a lot of mess and potentially a serious injury as someone intervenes manually. As a way of preventing just this scenario, not to mention eliminating the risk of wasted time and energy along with the loss of productive time, mining companies have turned to Track Straight to install its conveyor belt alignment systems at iron ore mine sites in Western Australia.
As Russell Norman, technical manager at Track Straight explains, “One of our clients trialled our mechanical adjusters on their two worst-preforming conveyors for belt tracking. These belts are both 1800mm wide and running iron ore at 6000 tph. They implemented the Track Straight mechanical adjusters to eliminate the perceived pressure their operators might feel when belt drift occurs. In the past they had found that this was when unsafe interventions happen. It’s when employees force tracking frames with ropes or chains to temporarily align conveyor belts to overcome issues causing misalignment.”
Norman admits that tying up tracking frames to rectify belt drift is not a new problem. But while such interventions are effective in correcting drift events, it’s less than ideal for several reasons. “It is an un-engineered solution and to be done safely should be done under isolation. The Track Straight system gives the operators a safe and engineered way to force tracking frames without isolation. It allows the operator to see the effects on the conveyor tracking as they make adjustments, while seeing the corrective action live and setting the tracking position accurately.”
Norman says that most clients see it as a pretty simple investment case. “The cost of a unit would be repaid multiple times over if it saved the belt from having to be isolated for half an hour to tie up a tracking frame. Of course, it’s an additional item and comes at an additional cost, but the safety and production benefits easily justify the financial case.”
Norman adds that after a six-week lead time the units were delivered, the installation was smooth and efficient, with four units fitted during a two-day shut down. “We sent a team and installed the units onsite, who were self-sufficient and clearly understood site policies and procedures… Some installations areas required custom guarding to adhere to guarding requirements in loading zones, but we were able to provide a custom guarding solution for these areas.”
The systems have now been in operation for over 12 months and, says Norman, it has been a great trial of the product, “Each unit has been used multiple times, and each time a unit is used it pays for itself. The units are now part of a preventative maintenance schedule to test the tracking frames correct operation while online. The system increases our clients’ productivity by eliminating downtime and most importantly eliminating live works risk to their employees, showing the commitment to continuous safety improvements.”