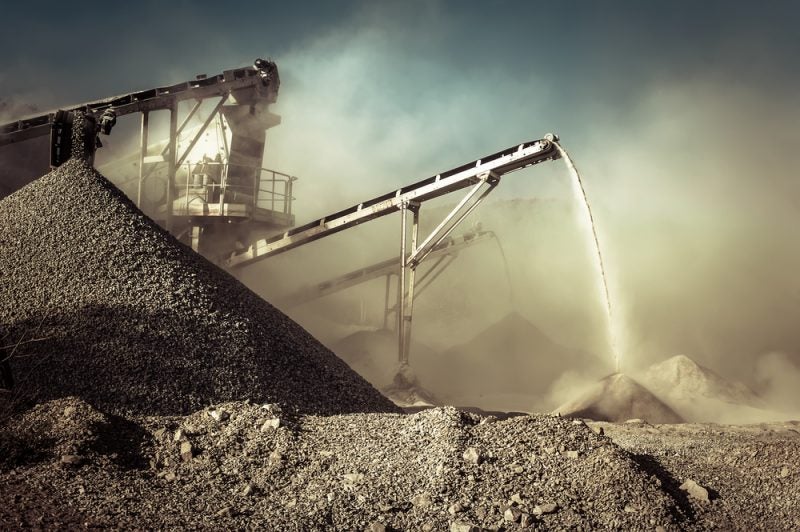
Extreme environments are common throughout the mining industry, meaning that operators need to have reliable equipment that can withstand the demands.
When it comes to reliability in level and density measurement, it is worth considering nucleonic instrumentation for mines. Radiation-based units take measurements that are not influenced by temperature, pressure or the potential volatility of a product.
The basic principle of nuclear measurements hasn’t changed in around 50 years. They involve a nuclear source being on one side of the pipe or container, with a detector on the opposite side.
As gamma rays are weakened when passing through matter, sensors are able to gain precise measurements of levels and density of the material inside based on the amount of radiation that is coming through. Measuring systems can be easily installed on the exterior of a vessel without interrupting production.
“With nuclear energy, there are certain misunderstandings about how it works, and so it becomes a last resort. Operators look at all other options and if none of them will perform as well as nuclear, then that is the solution to go with. Essentially, you only use nuclear when nothing else works,” says John Leadbetter, managing director of Vega – specialists in process instrumentation solutions.
Although the basic principle remains the same, the thing that has changed considerably is the advancements in technology. Modern detectors function more accurately and efficiently thanks to superior designs and components.
In mining, nucleonic measurement solutions are widely used by the aluminium sector, with the technology also popular in the gold and nickel industries.
“Depending on what you’re trying to achieve, nuclear can provide improved accuracy and efficiency than other approaches. But like all things there are limits to what you can do,” says Leadbetter.
“The biggest limit we have is the size of the nuclear source. By government law, we can only bring in up to a certain size, so it comes down to the application. We ask customers to give us as much information about the application, then we do an evaluation and from there we tell them whether we can do the job.”
Safety of nucleonic instrumentation for mines
Safety is one of the biggest concerns potential customers have with nuclear measurement devices. The thought of even having a small amount of nuclear material on site may be off-putting. Yet there are stringent requirements manufacturers of this equipment must obey. Furthermore, their proven accuracy in measurements makes them a wise investment.
“It is one of the safest products, and it is very heavily regulated by the government. There’s a lot of licensing and documentation involved, even for us to import the nuclear sources into the country,” explains Leadbetter.
“There’s a lot of traceability and it is a very controlled part of the industry. But benefits to the customer are, for those applications where nothing else will work, that they have the option to go with nuclear to achieve the results they need.”
Vega manufactures a series of nuclear-based measurement sensors. The SOLITRAC 31 offers continuous high-precision measurement of liquid and bulk solid levels. It can be fitted on vessels, autoclaves and reactors.
The MINITRAC 31 is used for non-contact measurement of product density and can be fitted on vessel walls or pipes. It is ideal for locations where space or access is limited. In addition, the WAYTRAC 31 is a continuous scale that measures the amount of material passing over a scale on a conveyor belt.
“Safety of our customers is always of paramount concern, but we also have to be careful of the fact that we hold a licence to work with this equipment. And if we made a mistake, we could jeopardise that licence,” adds Leadbetter.
“One of the things we always tell our customers is that we have specifically trained nuclear personnel to deal with their issues and queries. They’re not calling a department store and dealing with general customer service staff; they’re dealing with professionals who understand nuclear energy and the applications.
“At Vega, we have four people on the team here in Australia that are trained in nuclear, and they are the only people that will deal with nuclear queries and requirements.
“Over the last 50 or so years we’ve been focused on improving our design and introducing the latest components to make sure that what we are giving the customer is accurate and reliable.”