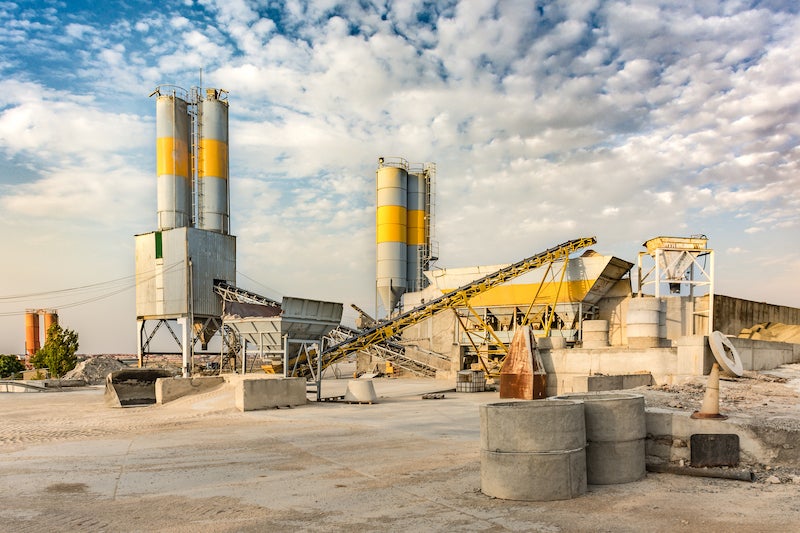
Ensuring you get the most out of your mining operation every day can be a challenge. But in order to keep productivity levels high and day-to-day efficiency at its optimum level, it’s necessary to remain as streamlined as possible.
Whether it’s minimising resources, improving productivity, or making cost or time savings, streamlining can have a significant impact on your overall operation.
Level measurement in buffer and production silos
While some streamlining routes may require an initial expense, such as new purchases or changes to equipment and processes, it’s important to consider the long-term cost. Over the course of the mine’s lifetime, that initial investment could create greater savings in time and resources down the line.
According to John Leadbetter, managing director at leading mining equipment provider Vega: “Many manufacturers are now creating less choice, and choosing instead to create equipment which can perform multiple tasks.
“For a mine site, or any operation in the industry, the less variety of products they keep on site, the easier it is for operators to manage their equipment.
“So if you have a piece of equipment that can be used across half a dozen different applications, operators can keep costs, ongoing maintenance expenses, and issues around holding and obtaining machinery spares to a minimum.
“This makes things a lot easier for the customer, cutting down their necessity to carry a heap of units, which all cost money and may never even be used.”
For example, Vega’s VEGAPULS 69, a radar sensor for the continuous level measurement of bulk solids, can be used across multiple operations and in several tasks. When it comes to level measurement in buffer and production silos, the VEGAPULS 69 will continuously tell operators the level of material inside the bin. So, as they’re filling that bin ready for the next batch, the device will indicate when they reach a certain point in order to stop filling as it has calculated it to be at the right capacity or tonnage.
It is a process that is mainly performed in the alumina and mineral sands industries. In both of these cases, this will typically be the final stage of the mine as operators load the material into rail carriages. In fact, any material that is granular or in powder form will use this type of operation.
However, the VEGAPULS 69 can also be used to perform level measurement of stockpiles and the level measurement of lime powder silos among other essential mining processes.
Similarly, the VEGAPULS 64, a sensor for the continuous level measurement of liquids, offers a range of special advantages when used with small tanks or narrow spaces, as well as an improved signal focus to enable use in vessels with many installations.
“We sell in excess of 100,000 units of the VEGAPULS 69 a year, worldwide,” says Leadbetter. “They are one of our most popular products and we have spent the last five or six years ensuring we develop it correctly and to the customer’s satisfaction.
“Because of our years of experience, we’ve been listed as a preferred supplier in a lot of Australian mining operations. But while these units have been on the market for a while and have proven themselves, we have continuously improved them to meet our customer’s requirements and ensure the best possible results, every time.”